After an approved referendum and a lengthy selection process, Kraemer Brothers was awarded the Aquatics Renovation Project for the Kickapoo Area School District located in Viola, Wisconsin. This project encompasses remodeling existing space in the building to include locker rooms, a multi-purpose room, and a natatorium. Starting in the middle of March, Kraemer Brothers has been at work demolishing the team locker room area as well as the pool deck. After 2 weeks of demolition, the rough underground MEP systems will be installed with a new concrete slab being poured in the team locker room while the pool will continue to be demolished until we are able to back-fill the multi-purpose room area. Once finished, the new 43’ x 38’ pool and 1,600 square foot multi-purpose room will be open for the community to use for wrestling competitions and practices, exercise classes, community meetings, activity training, and scheduled events.
Promega Kepler Center Taking Shape
After months of pouring footings and foundations at Promega’s distribution and logistics facility, the Kepler Center Expansion is starting to take shape with structural steel under way, along with the mezzanine and metal roof decking. The Kepler Center, originally finished in Fall of 2015, was designed and built for future expansion. On the heels of recent major growth, Promega finalized their expansion plans, which resulted in a 196,500 square foot expansion to the existing 126,500 square foot building. Once complete, the project will total nearly 323,000 square feet or nearly 7.5 acres of floor space! The new expansion includes additional Vertical Lift Modules (VLM’s), a large freezer farm room, and an enormous warehouse space for fixed and mobile high bay racking systems. This expansion will allow Promega to continue with their growing product lines of kit assembling, packaging, and shipping internationally and domestically.
Woodland Crest
RETAIL PORTFOLIO
Woodland Crest Retail Development
Waunakee, WI
Overview
ARCHITECT
Gary Brink & Associates, Inc.
Square Footage
19,000 (Phase I)
8,900 (Phase II)
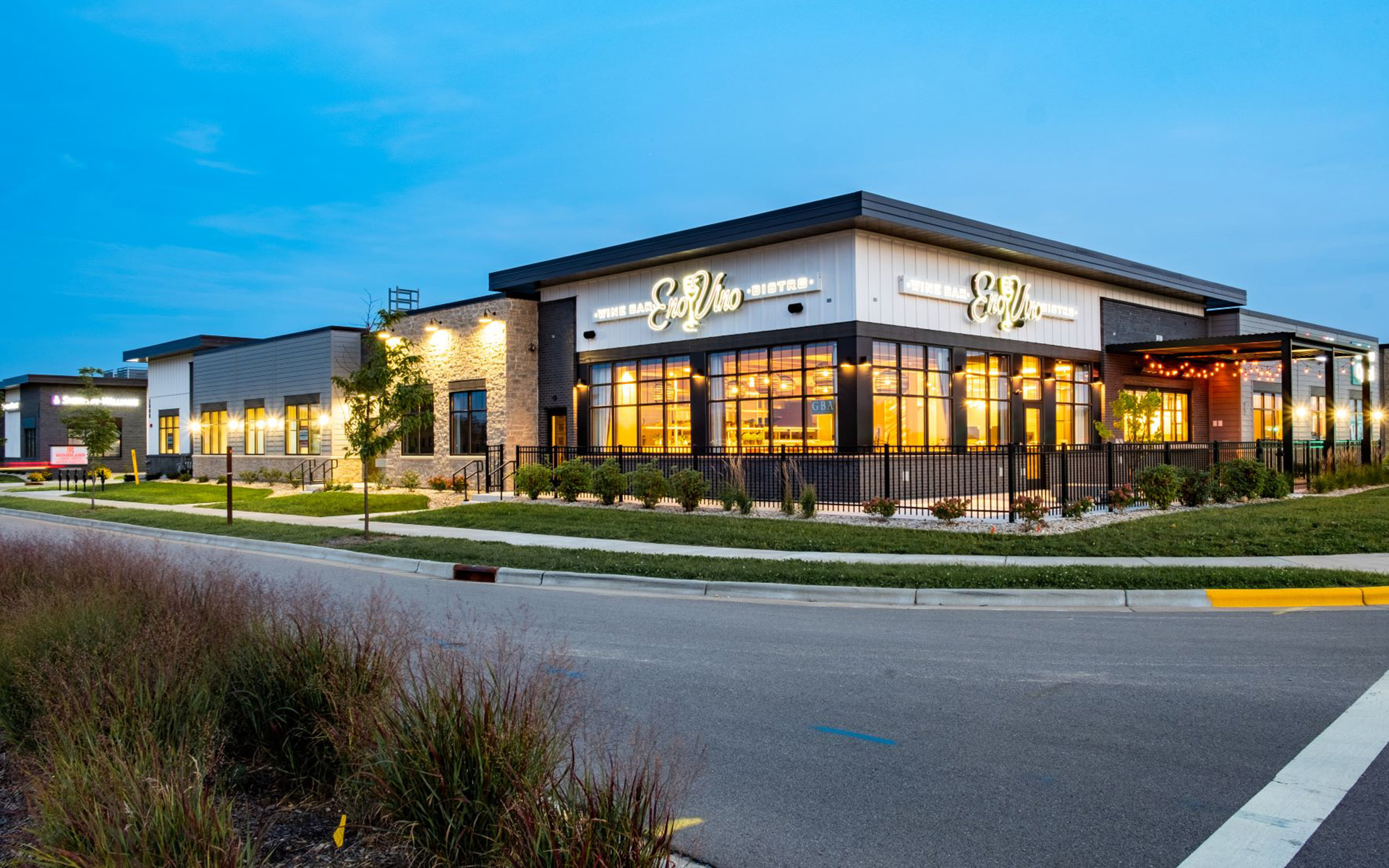
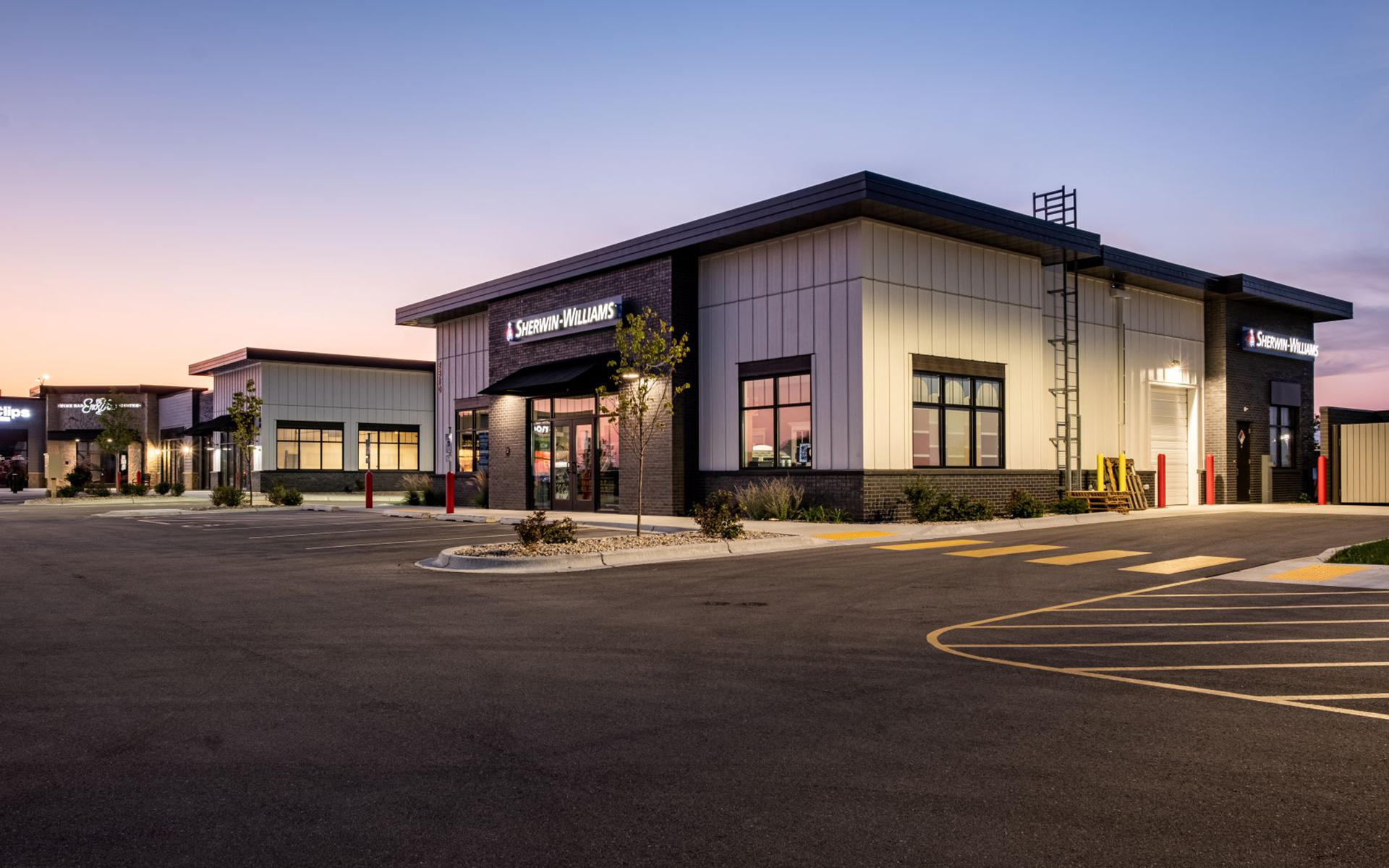
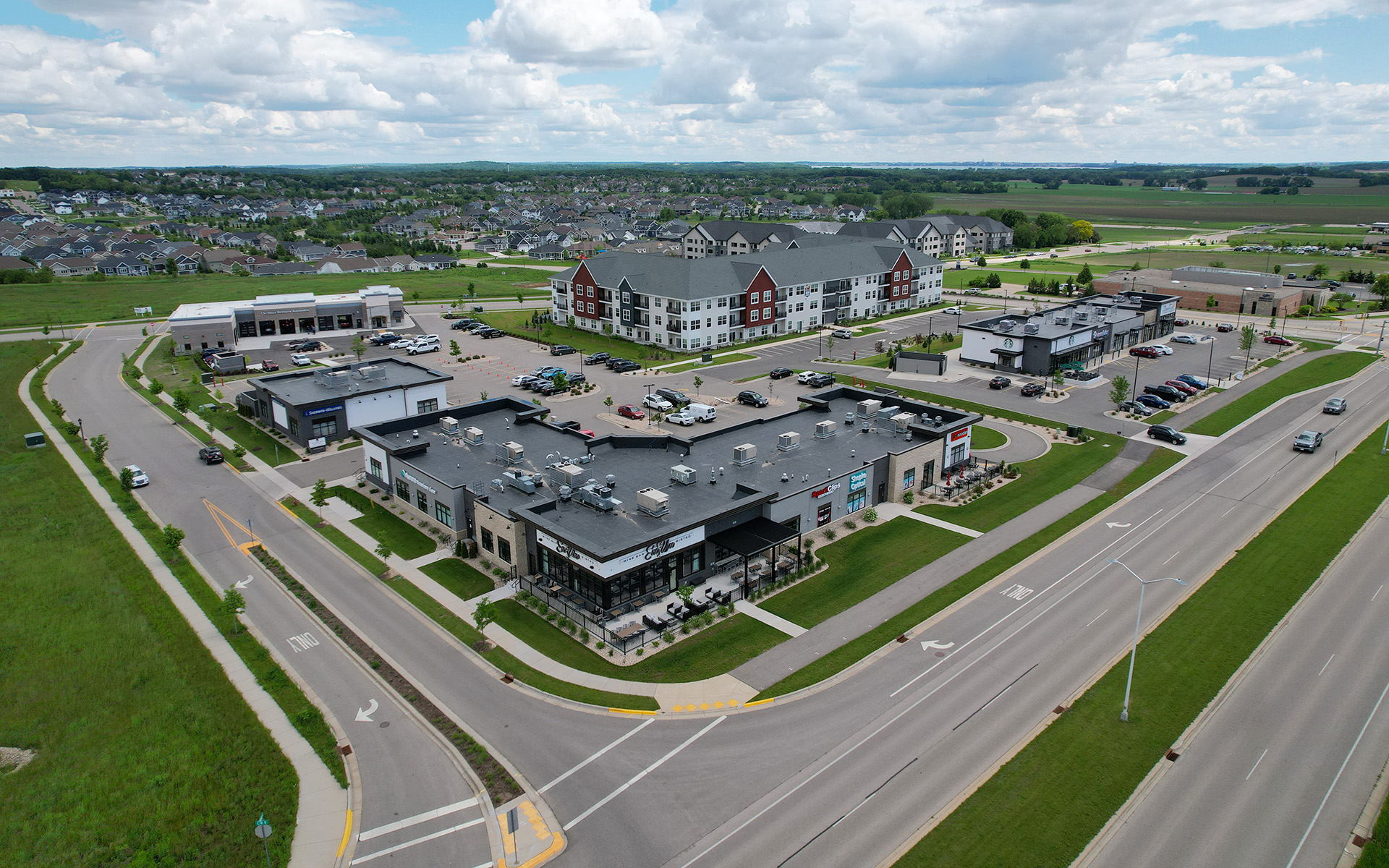
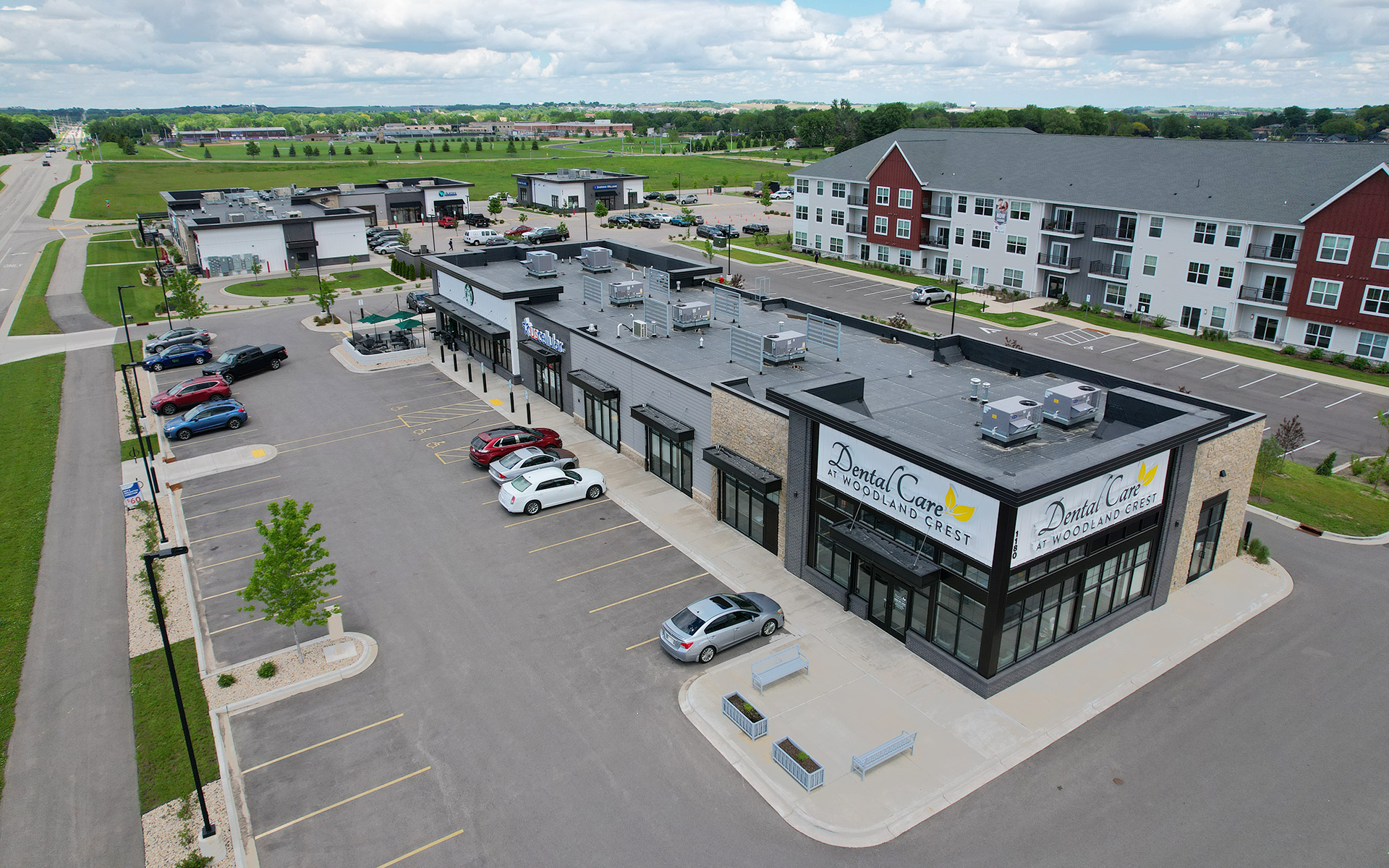
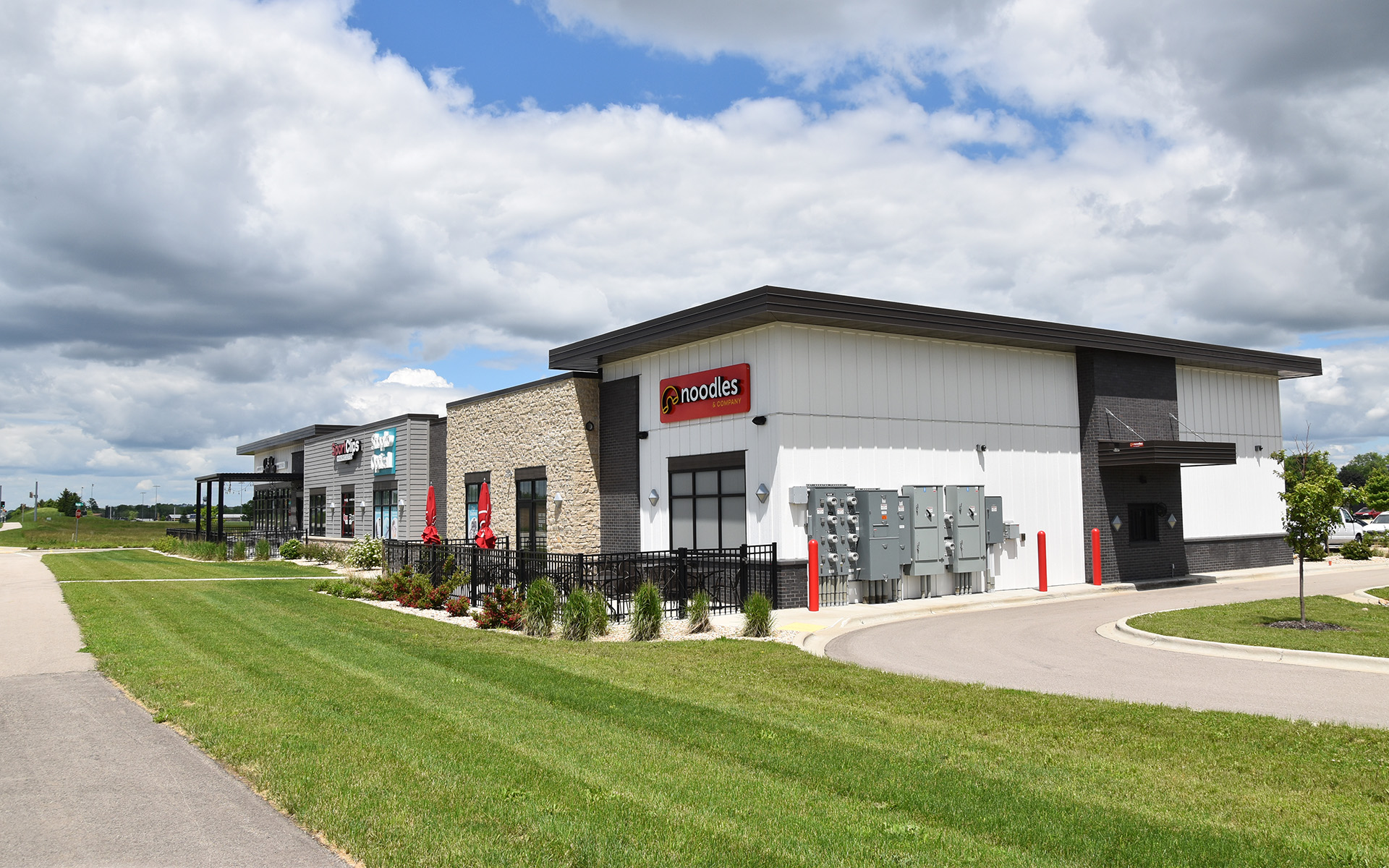
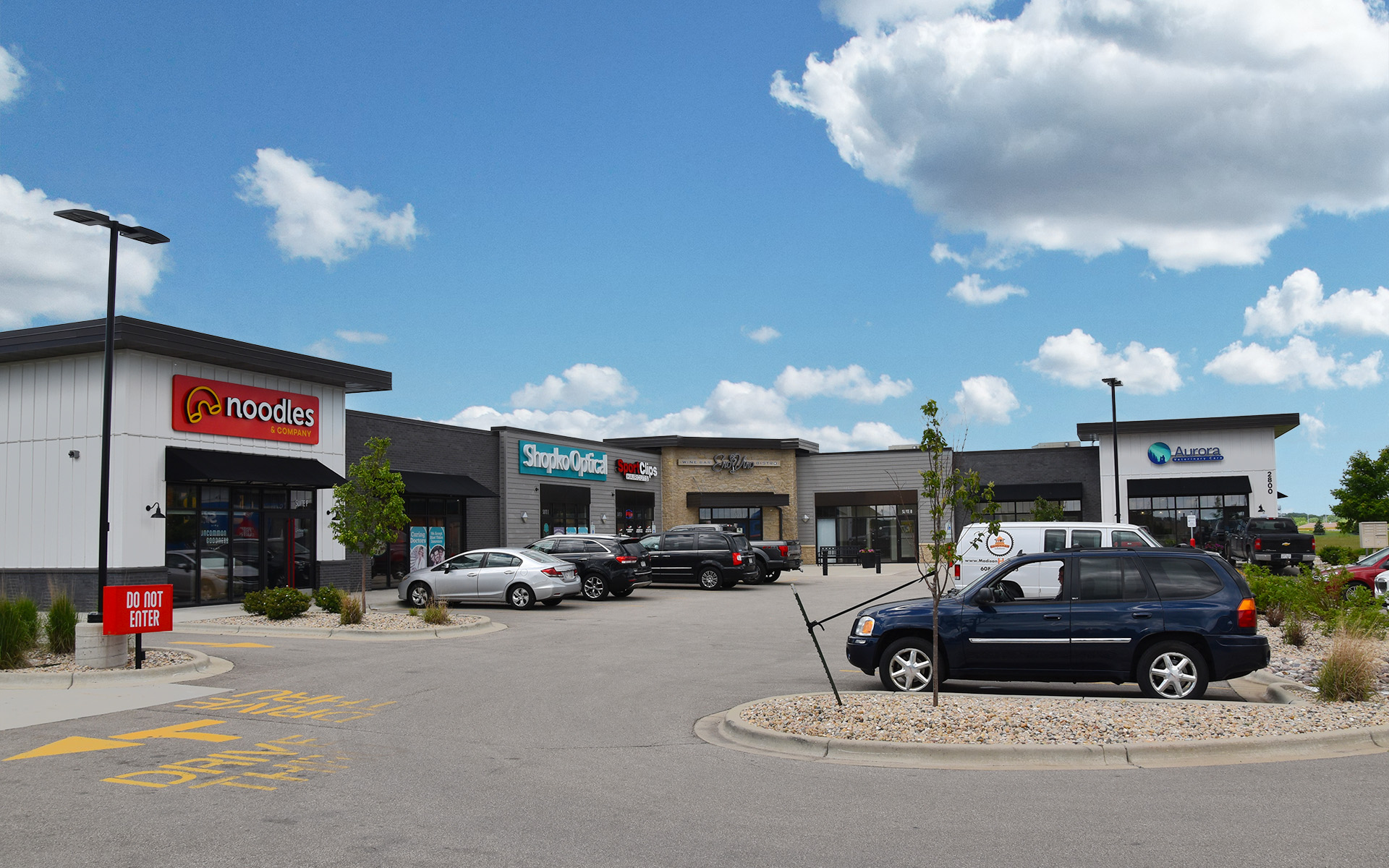
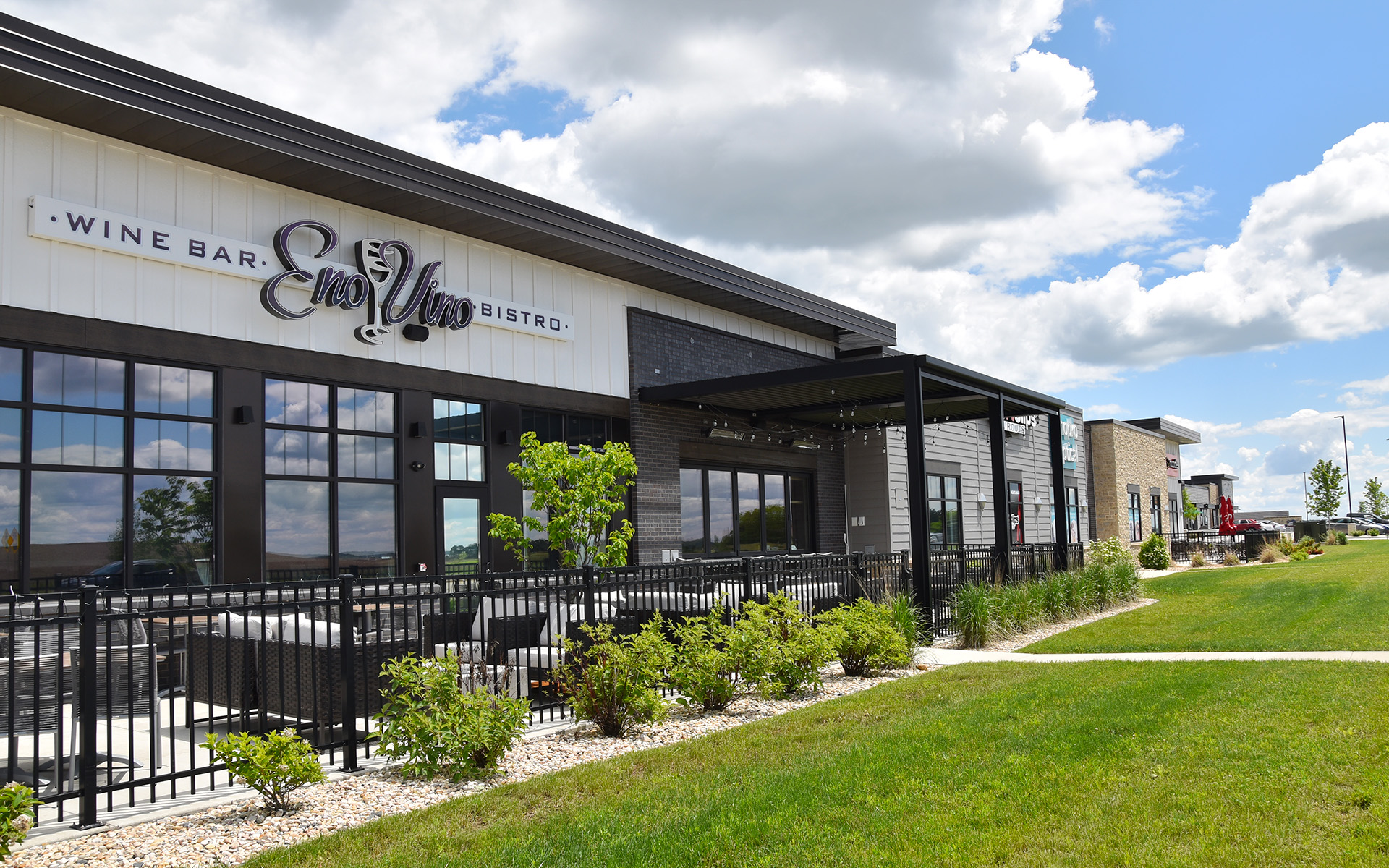
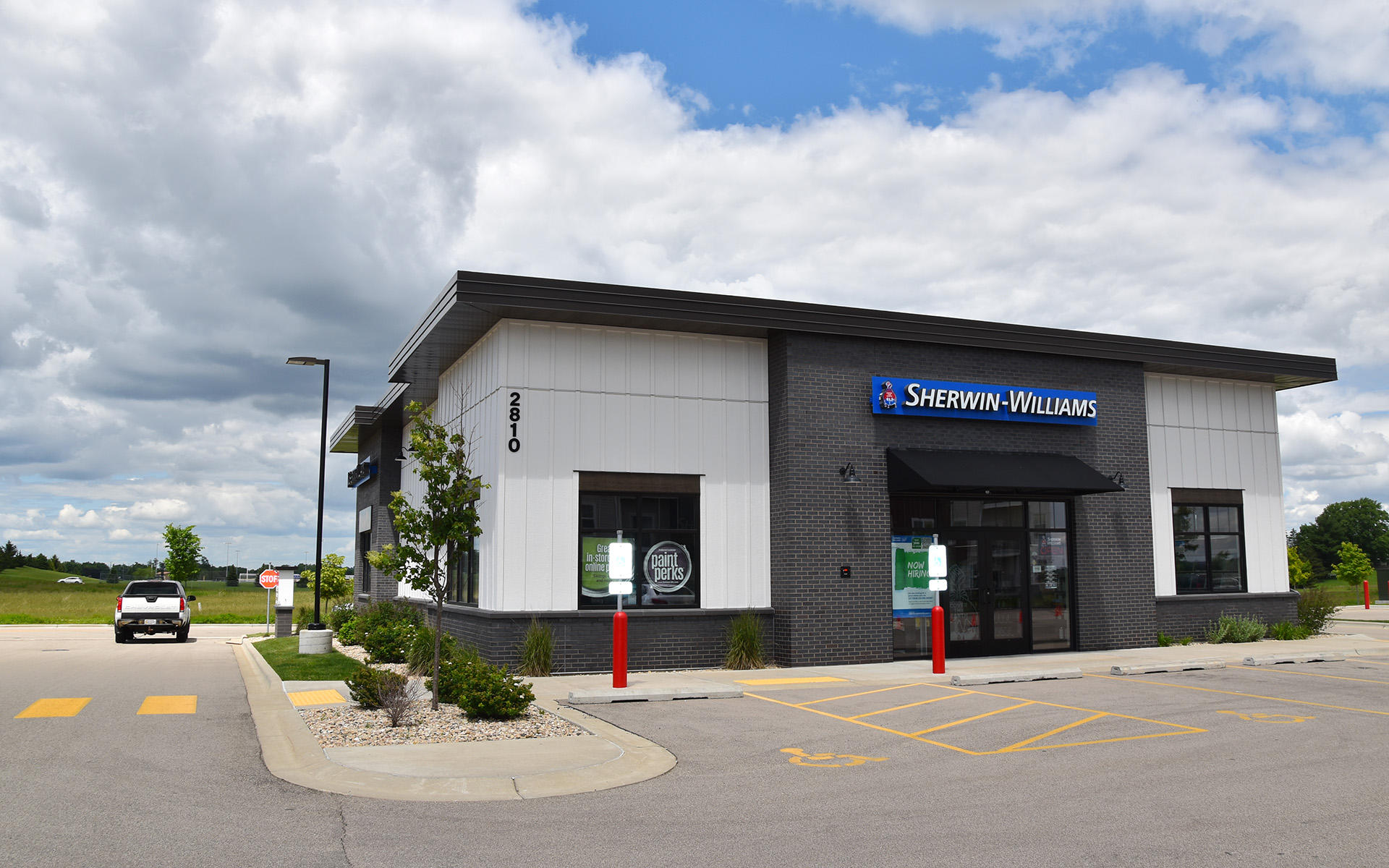
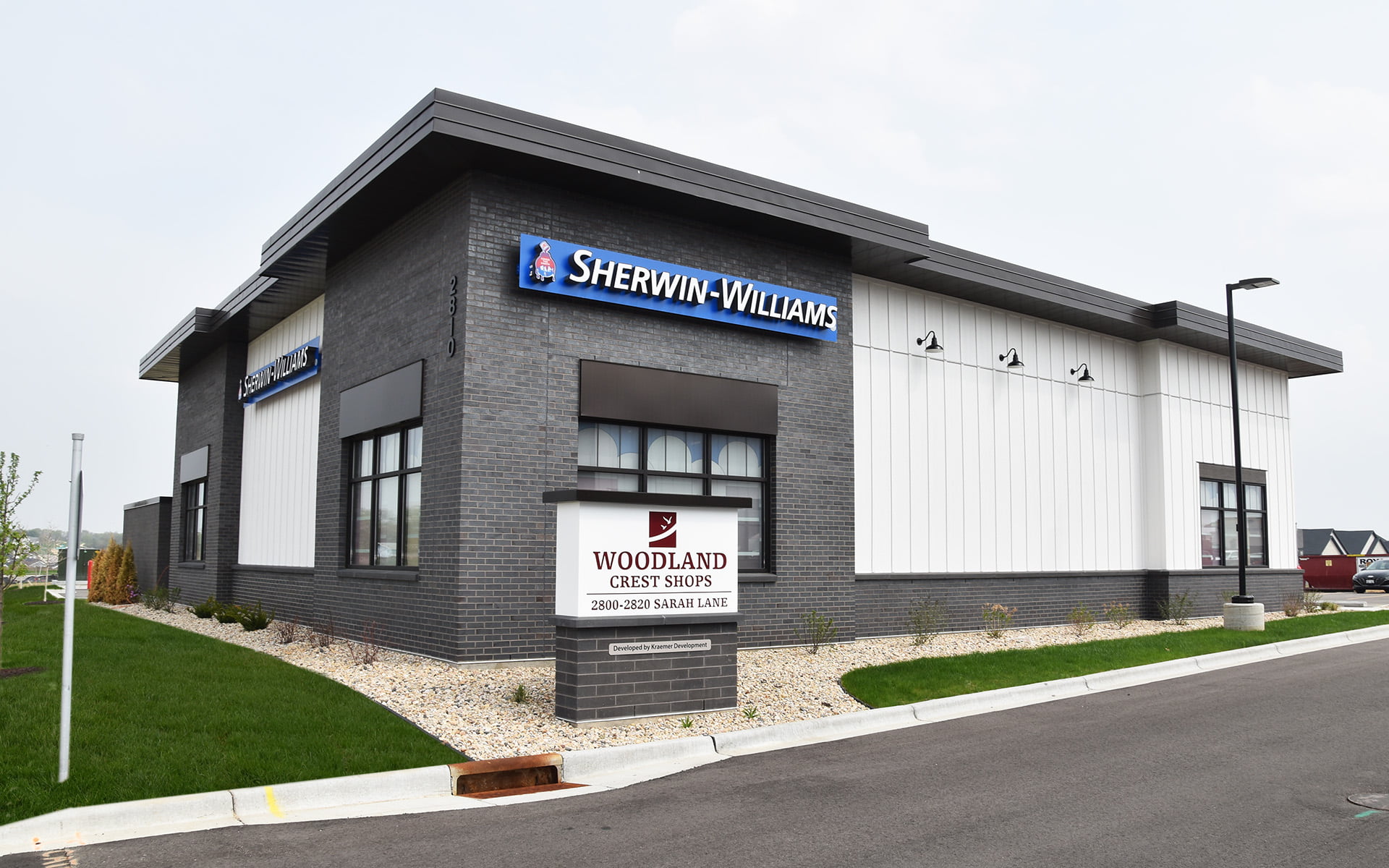
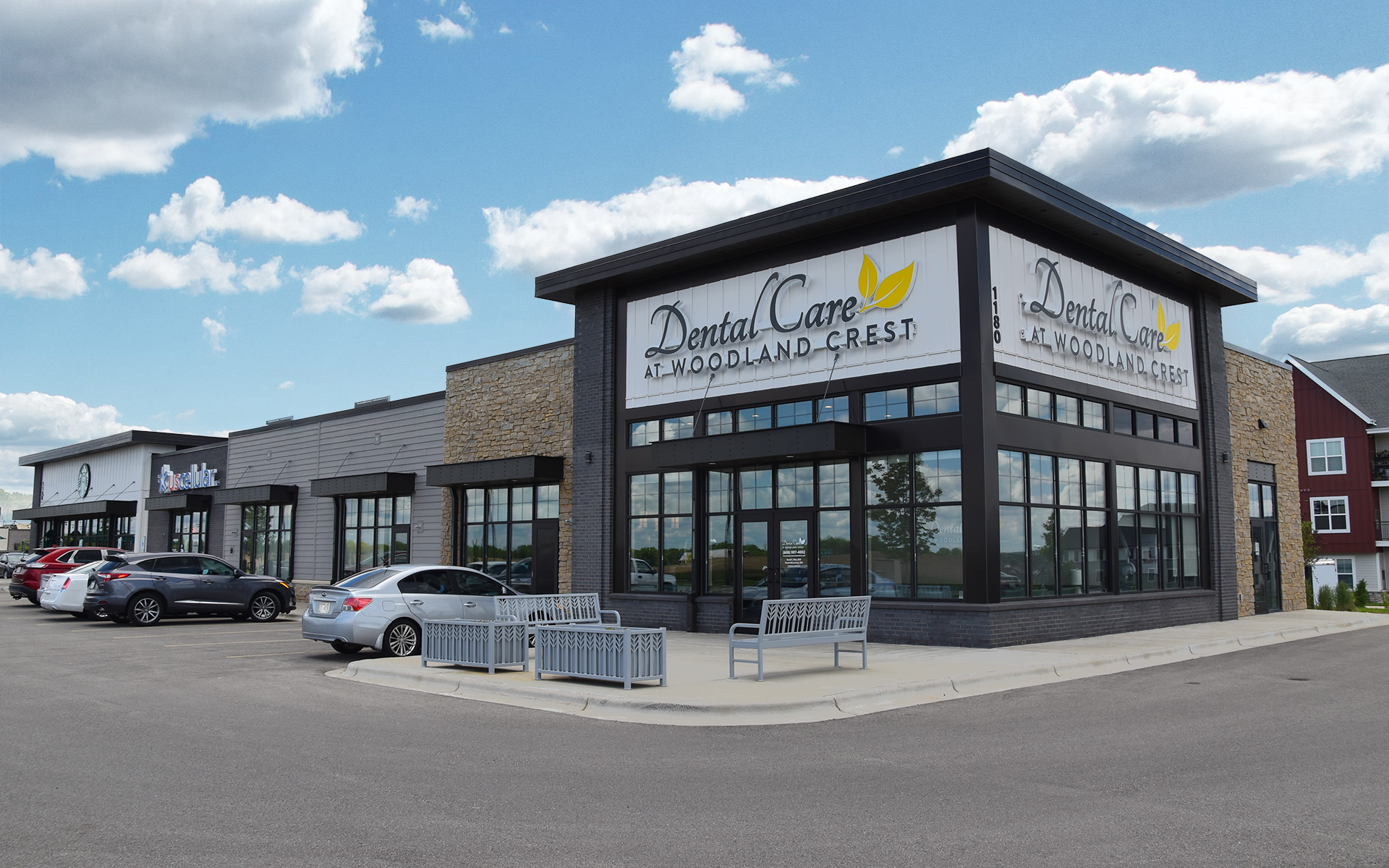
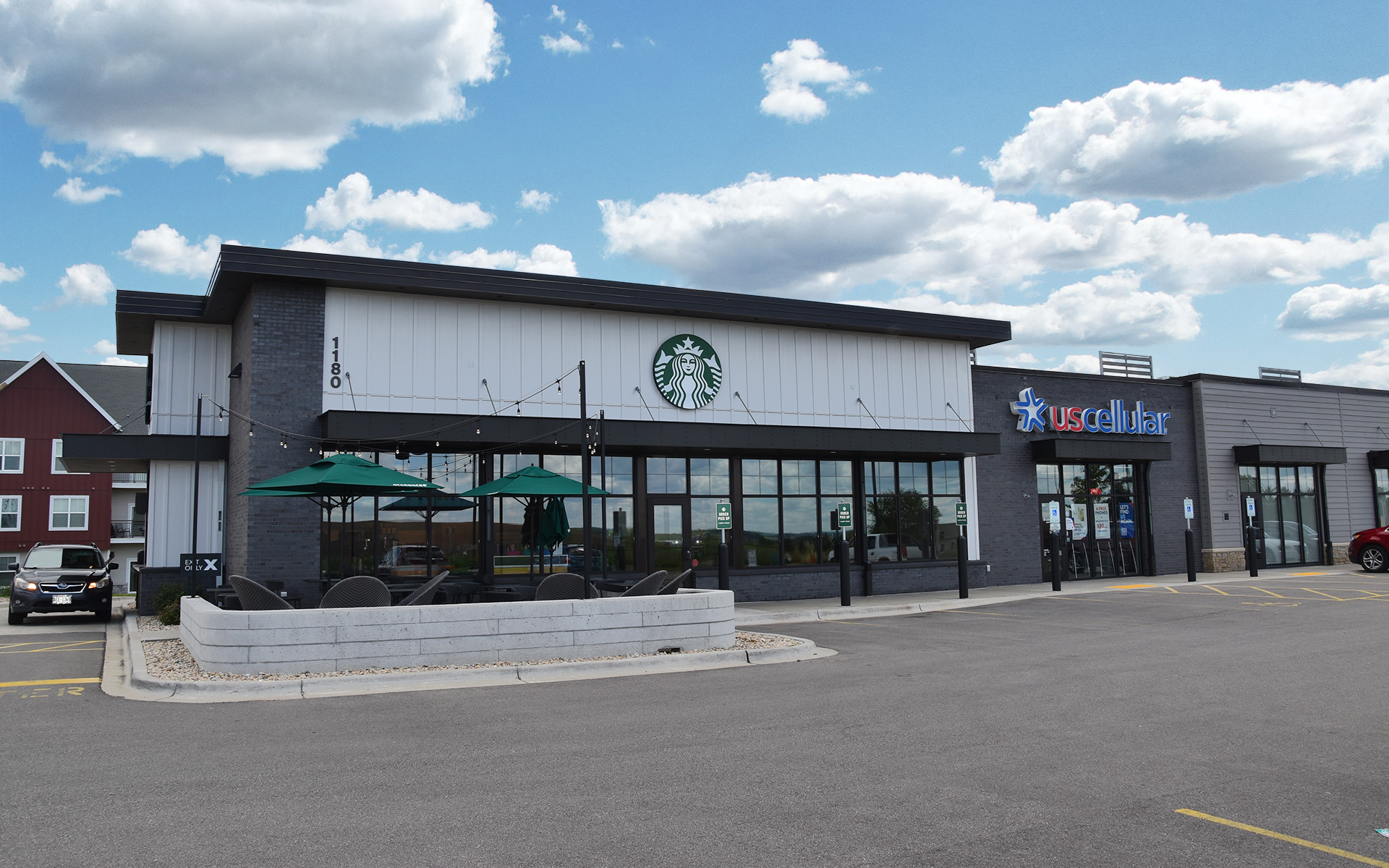
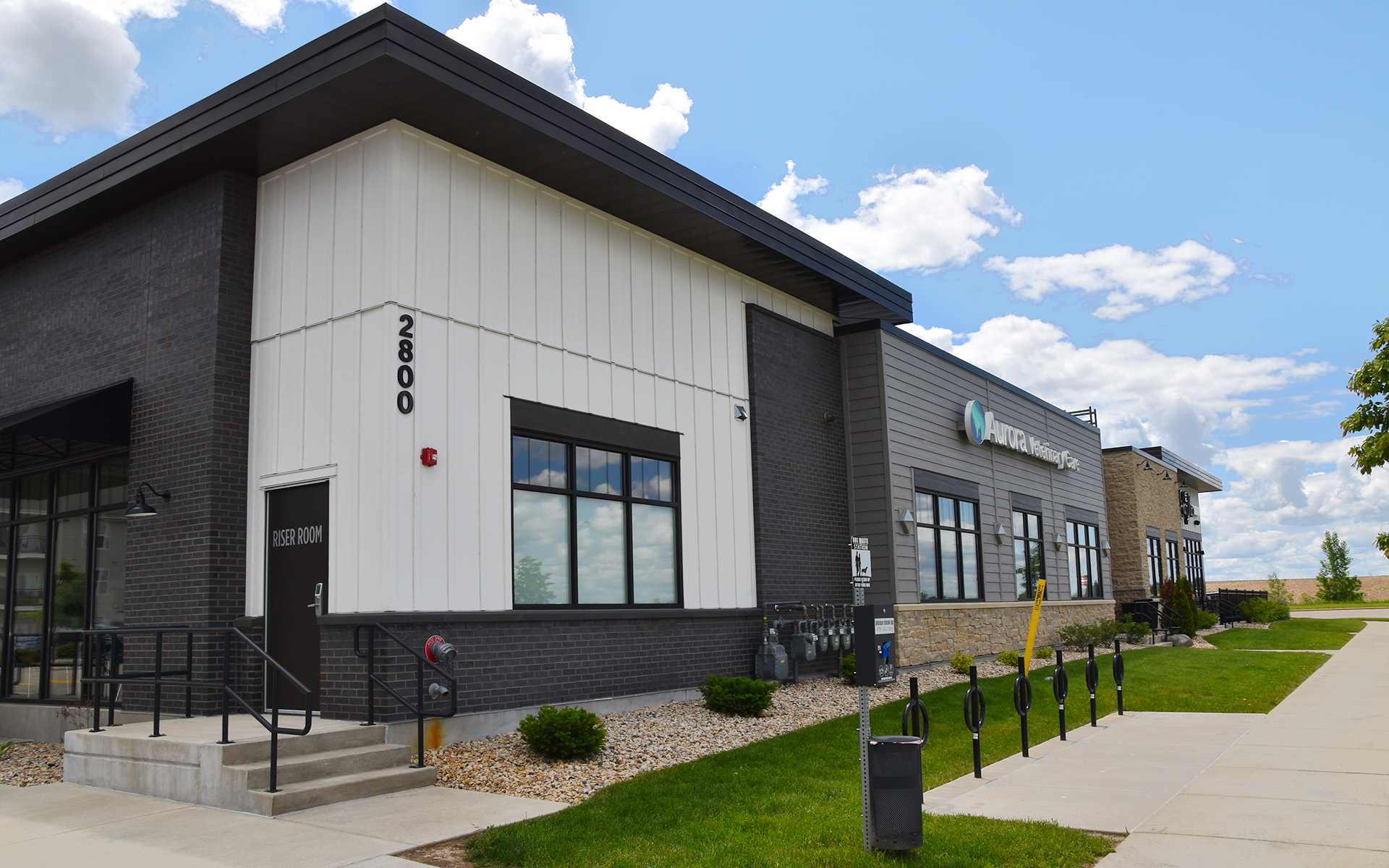
WOODLAND CREST RETAIL DEVELOPMENT
Mixed-Use Development
Phase 1 of Woodland Crest, located in the heart of a rapidly growing area in Waunakee, Wisconsin, consists of 2 mixed-use commercial buildings. Sitting between a future grocery store and multi-family housing, this development hosts multiple restaurants such as Noodles & Company and Eno Vino Wine Bar & Bistro and retail/service tenants including Sherwin Williams, Sport Clips Haircuts, Shopko Optical, and Aurora Veterinary Care. The Noodles & Company restaurant features a drive-through order area while both restaurants have exterior patio seating for customers to use on nice days. With decorative brick and stone exteriors, contrasted by manufactured wood and metal siding, this building presents a bold appearance.
Phase II of Woodland Crest features a Starbucks, US Cellular, and a Dental Office in this highly sought after location. After demolishing the existing buildings on the site, new construction was off to a quick start. To offset lumber shortages for wood framed panels, our Building Information Modeling and Prefabricating Department designed the plans to fabricate these panels in our Equipment & Distribution Center. This single-story building features a brick and stone exterior, accented by white wood-grain siding, black metal fascia, and aluminum storefronts. Accommodating three unique tenants, each store required strict design criteria and standards, resulting in high coordination between the architect, construction team, MEP subcontractors, tenants, and the building’s owner.
RELATED
Mineral Point School District
EDUCATION PORTFOLIO
mineral point SCHOOL DISTRICT
Mineral Point, WI
Overview
ARCHITECT
HSR Associates
Square Footage
52,000 Renovation
21,000 Addition
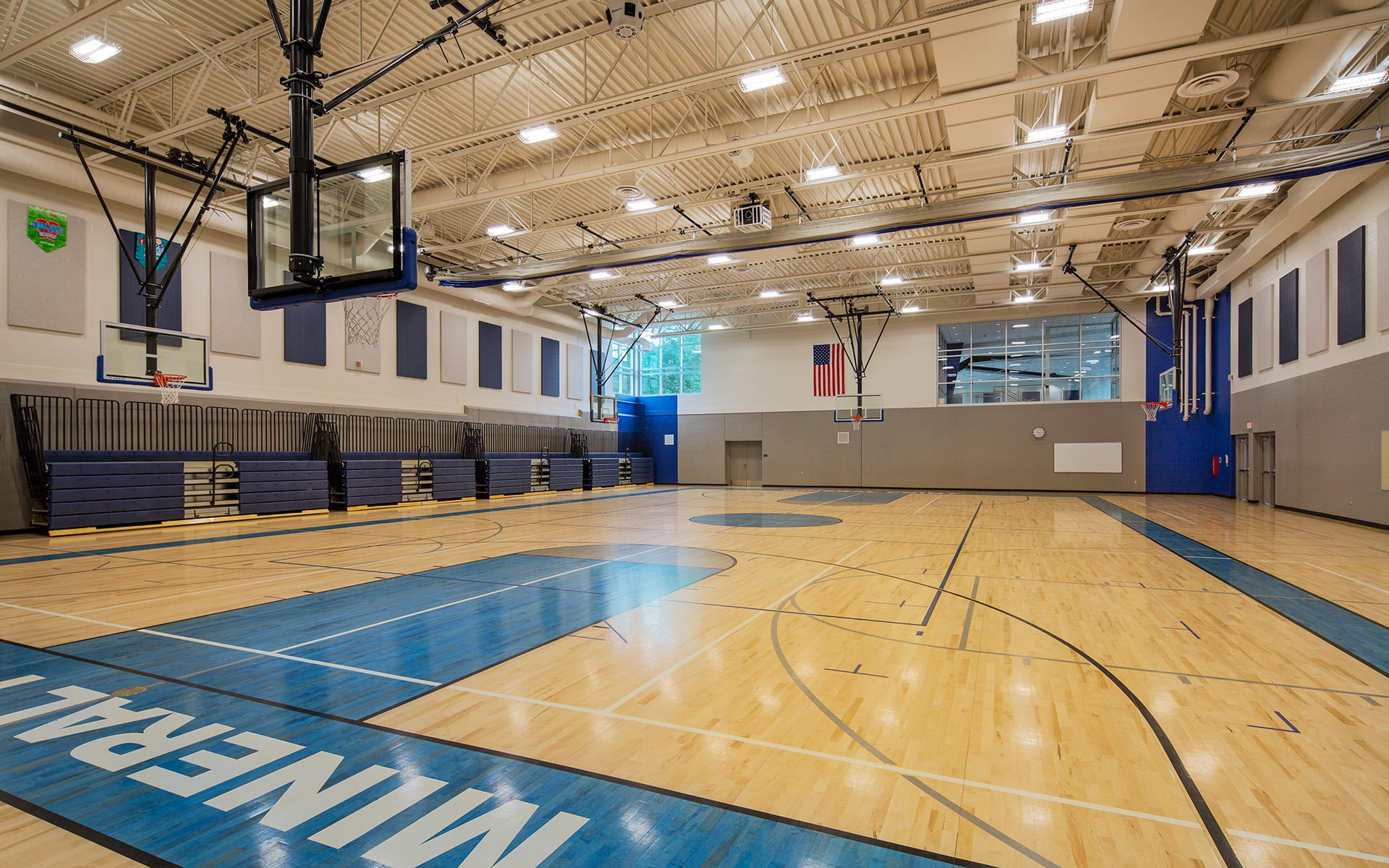
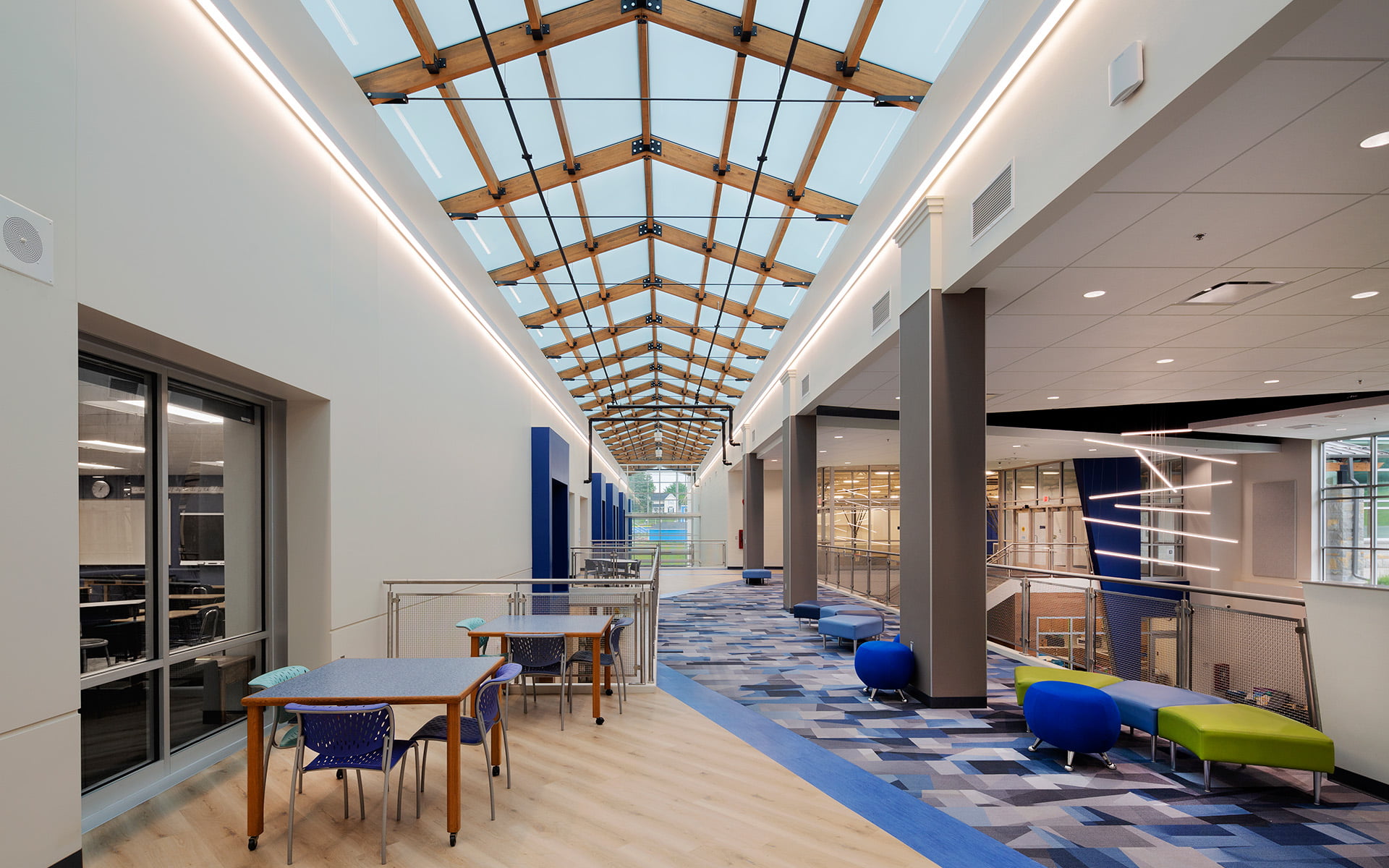
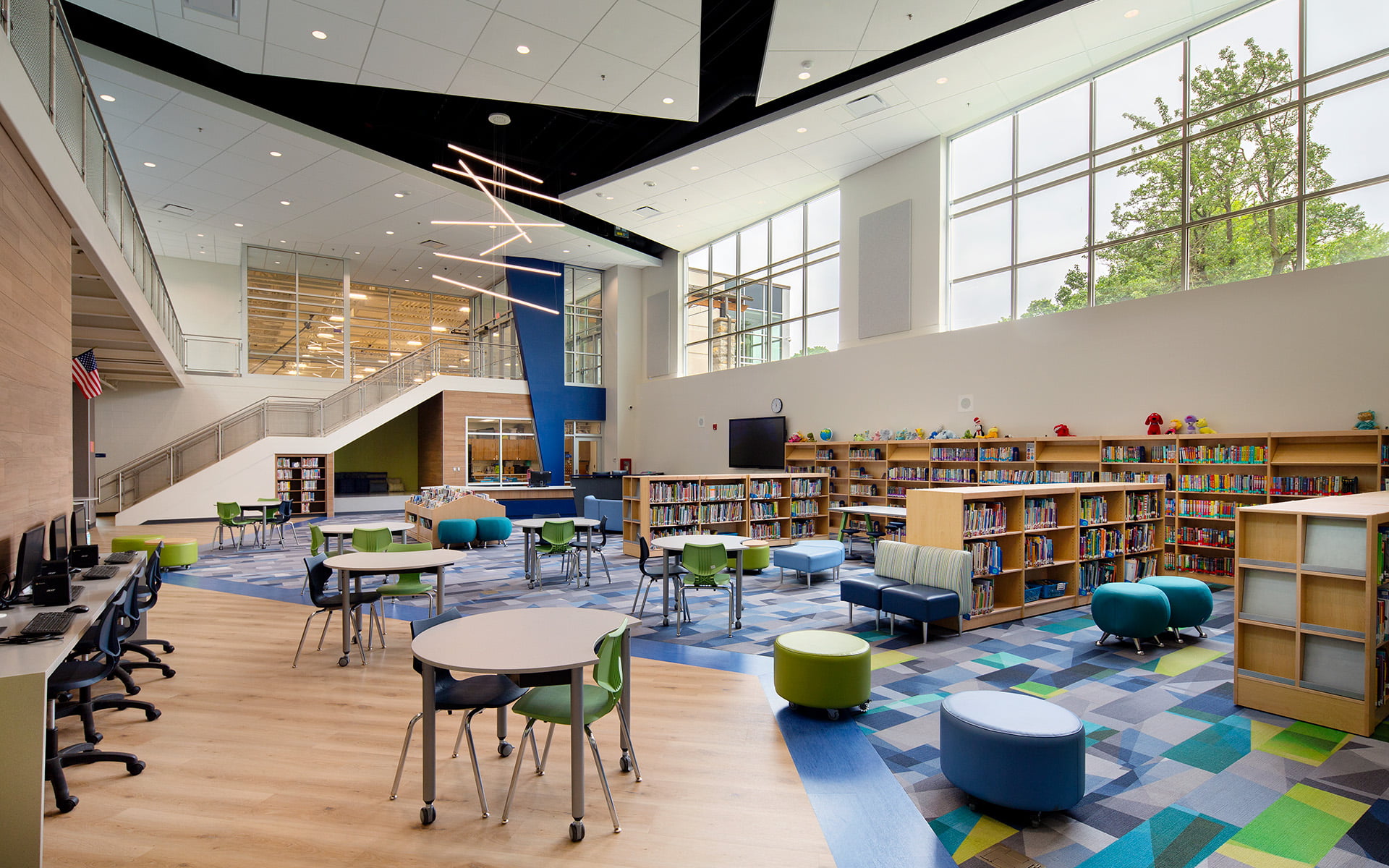

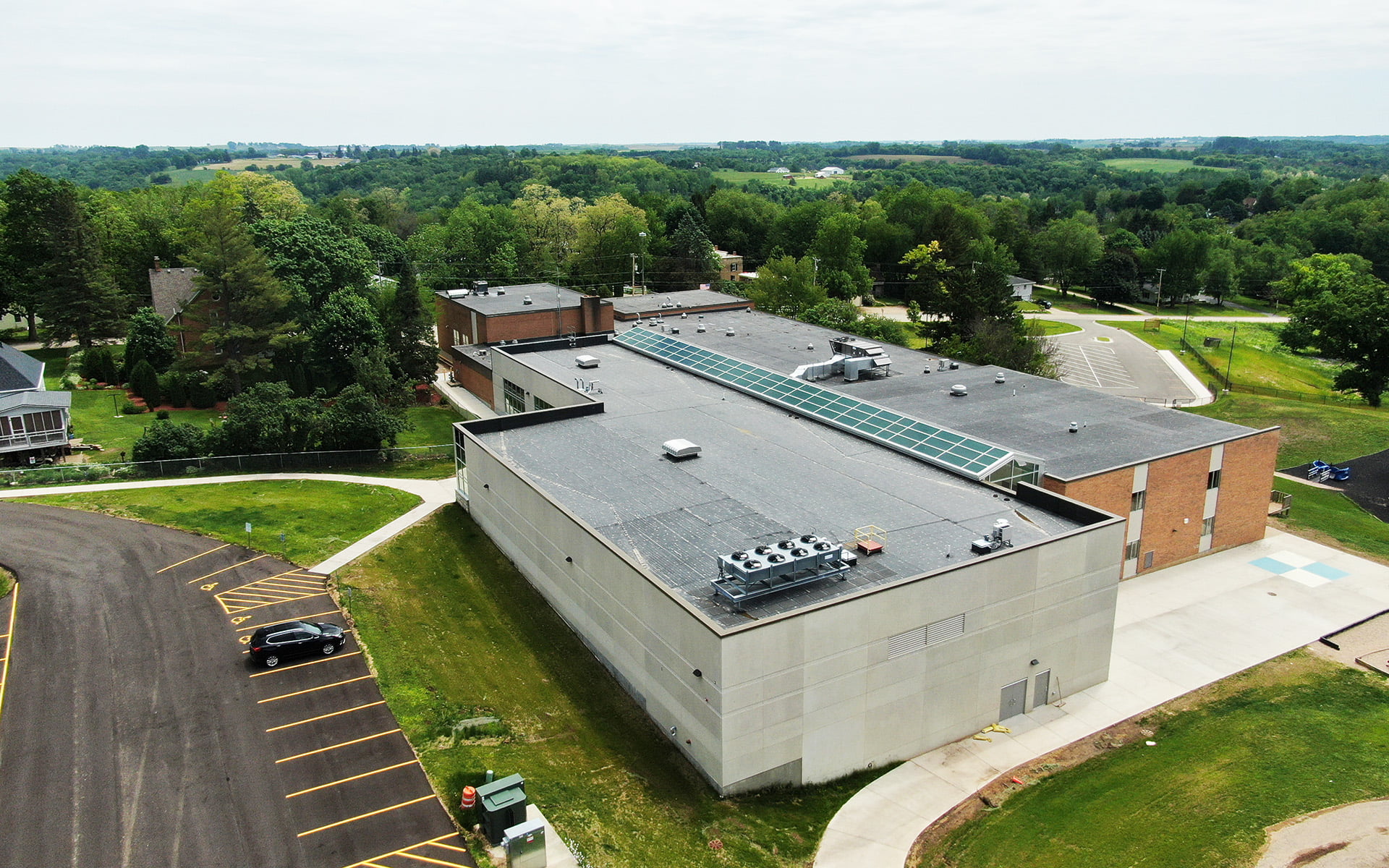
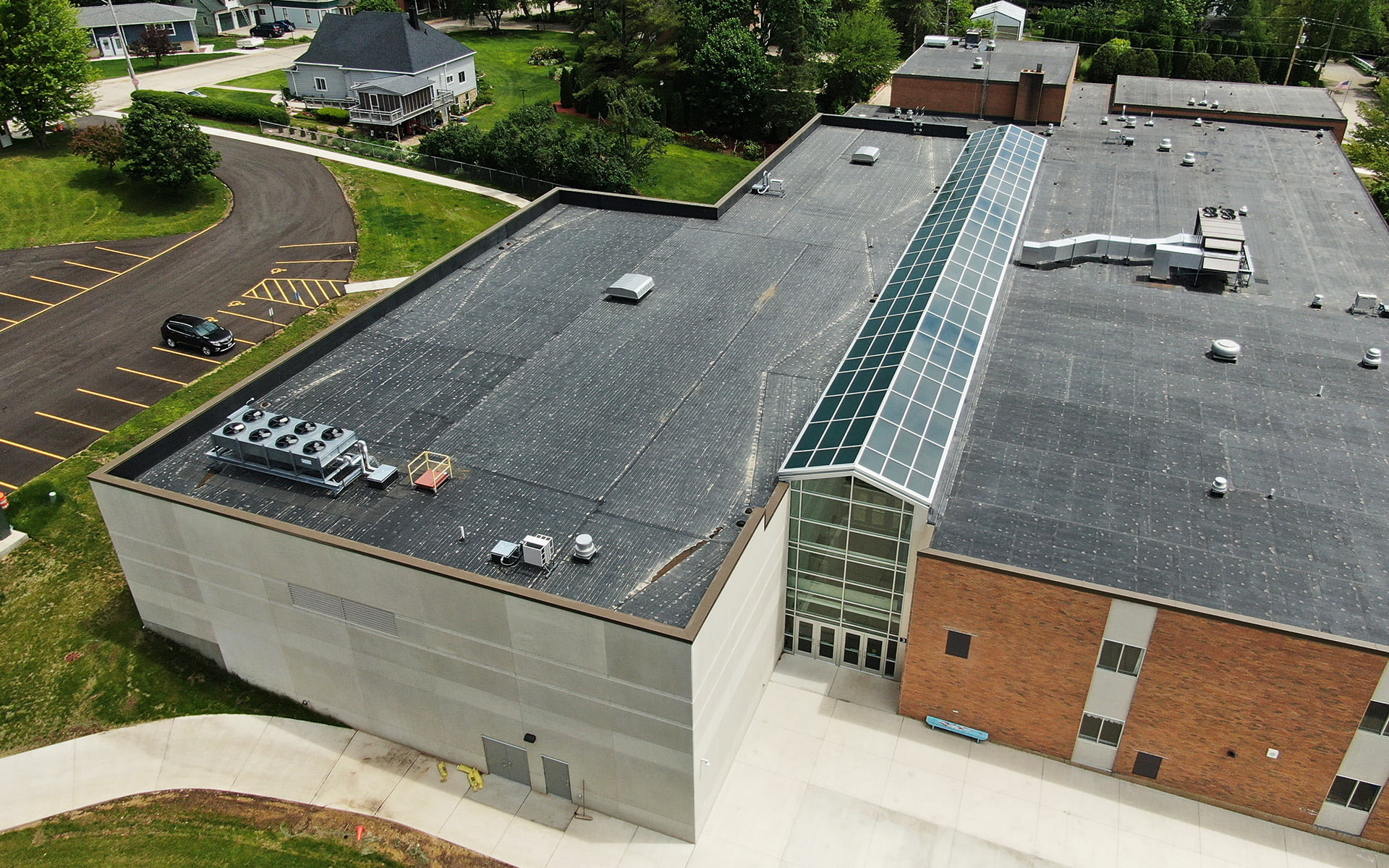
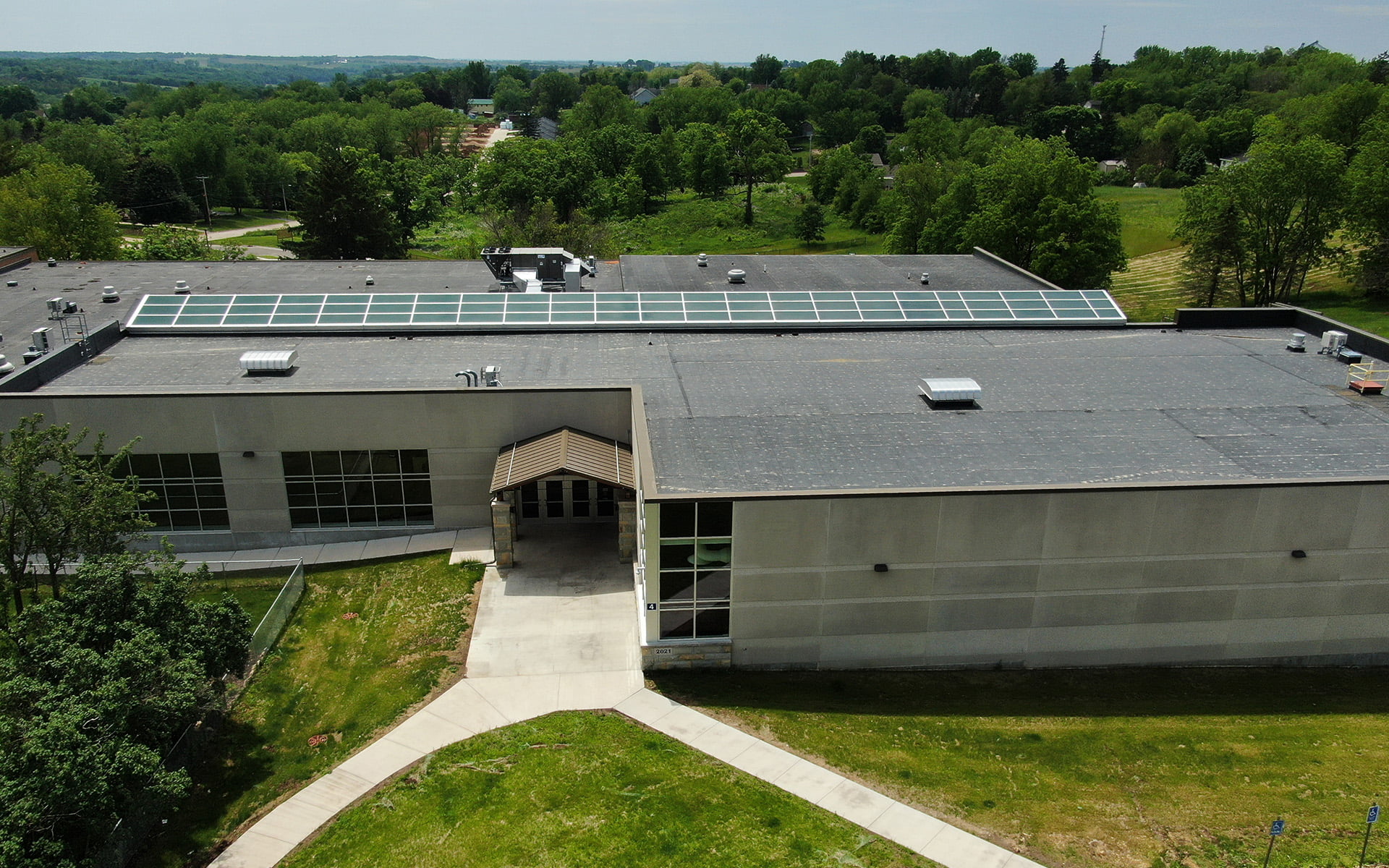
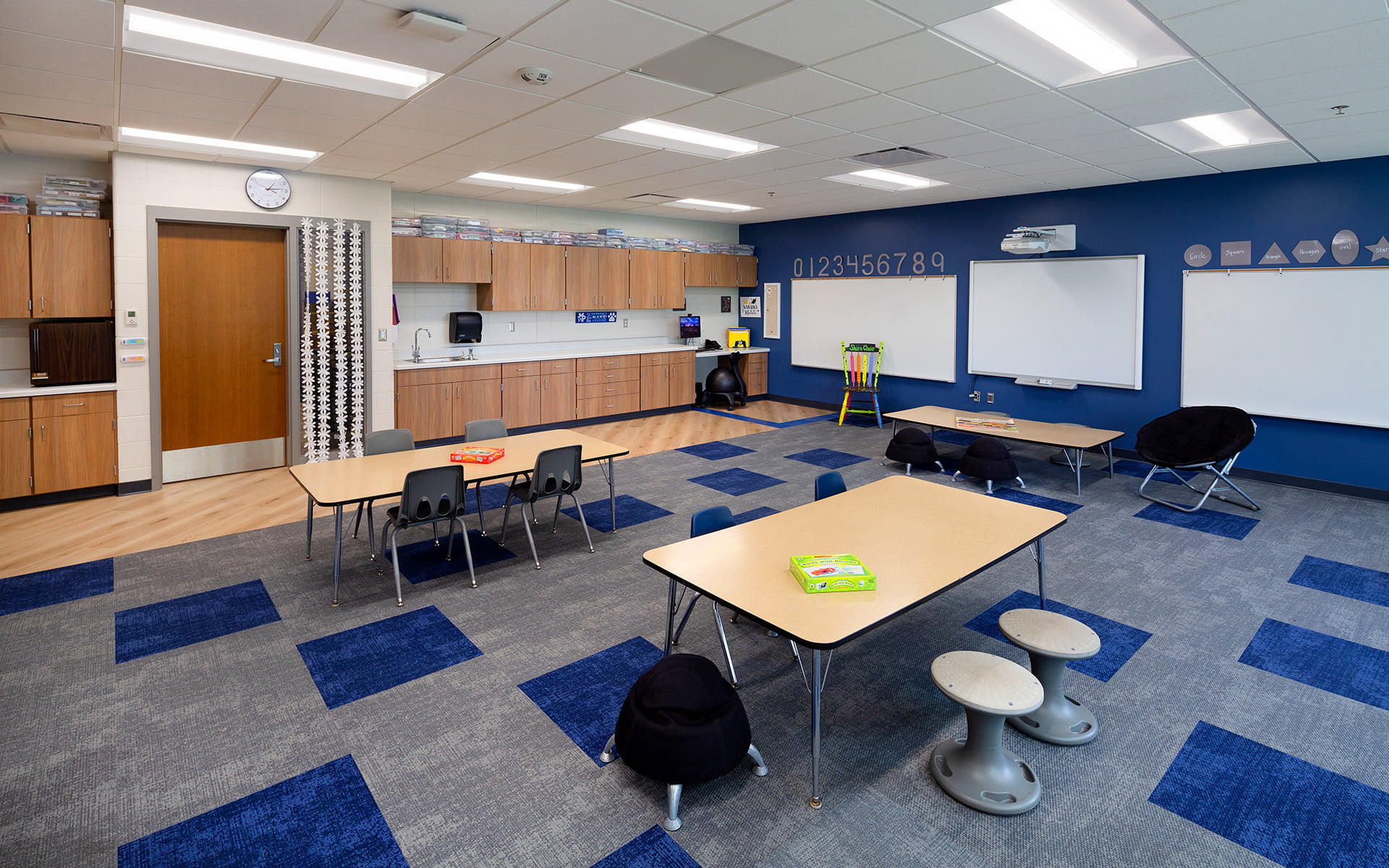
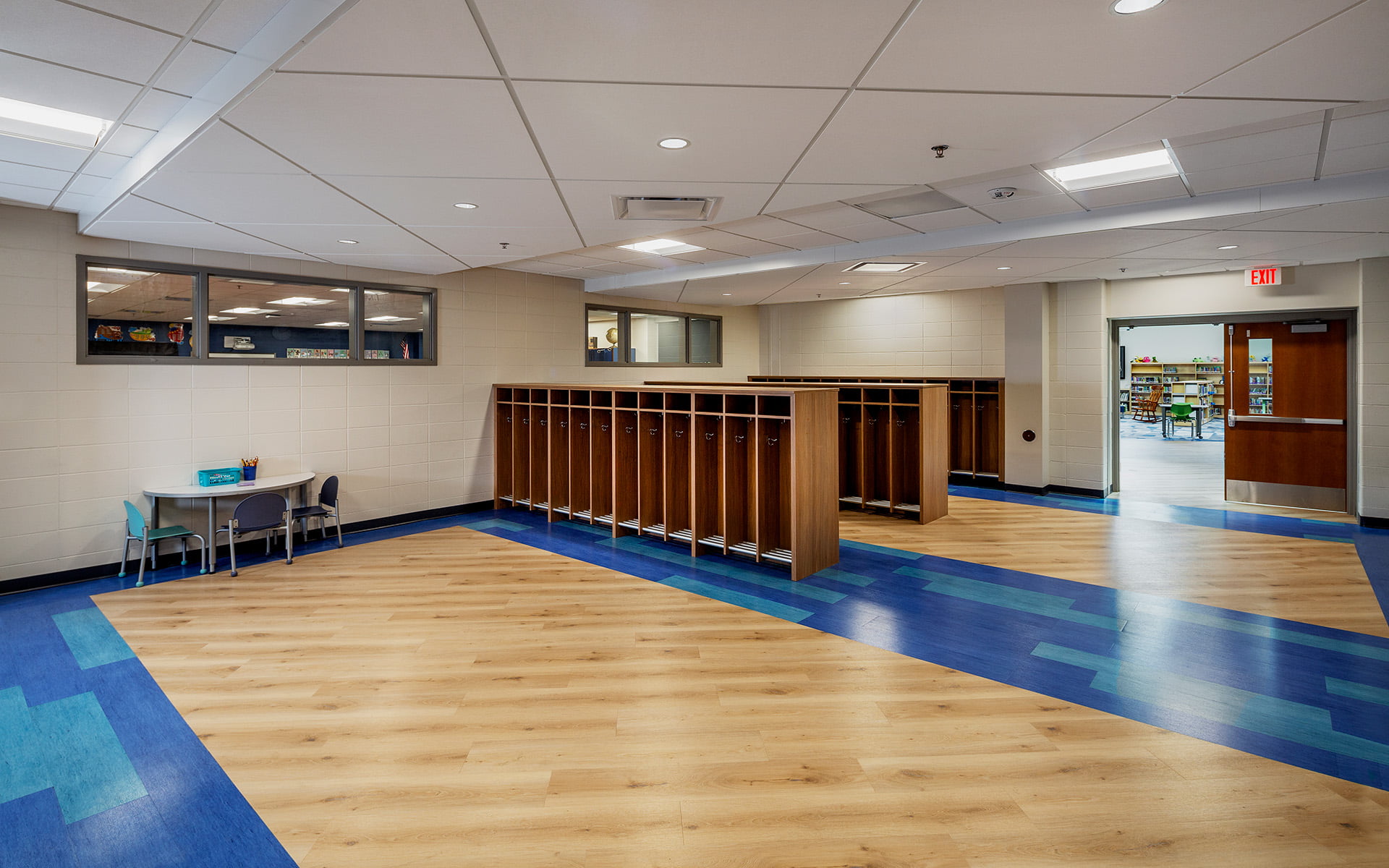
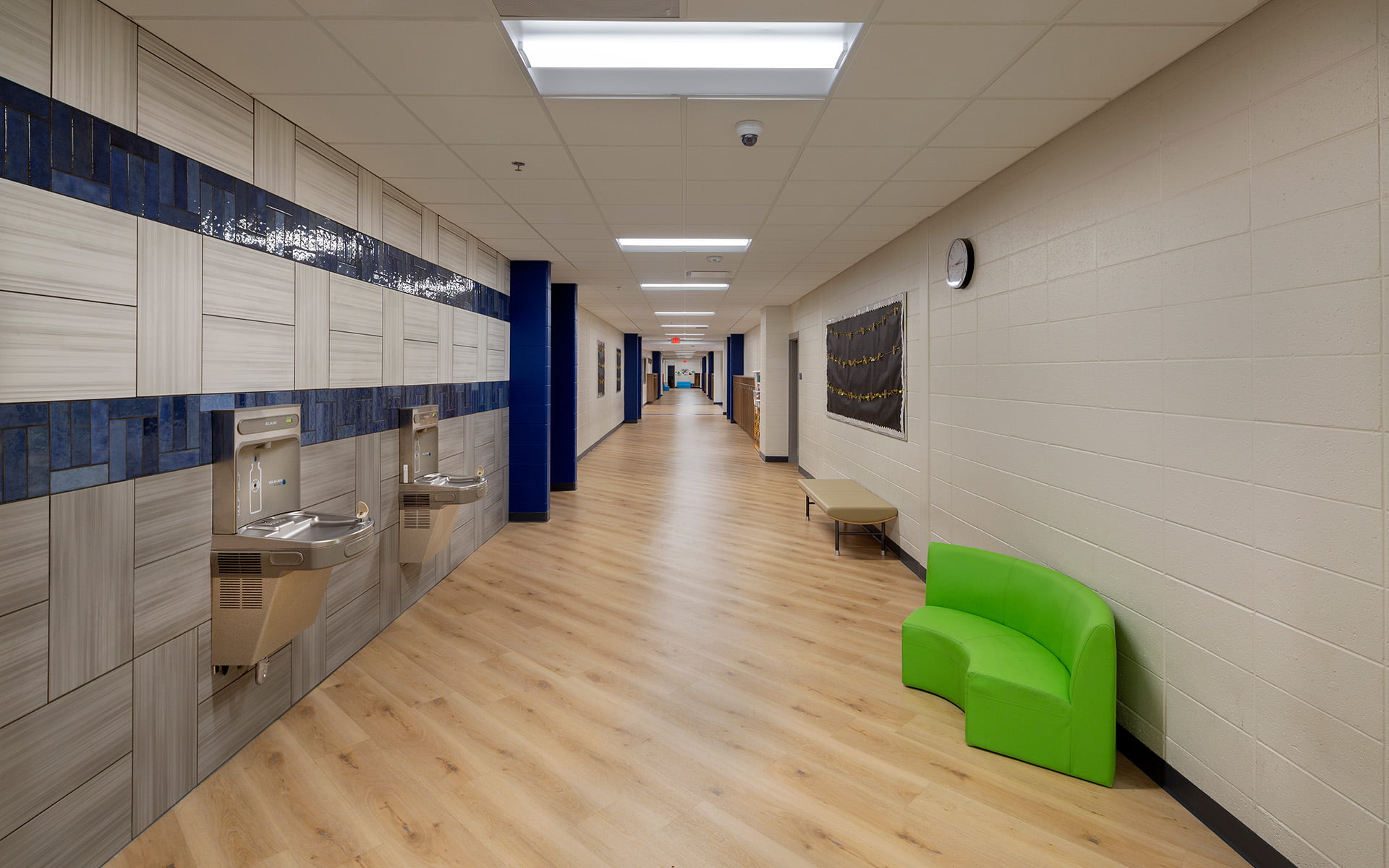
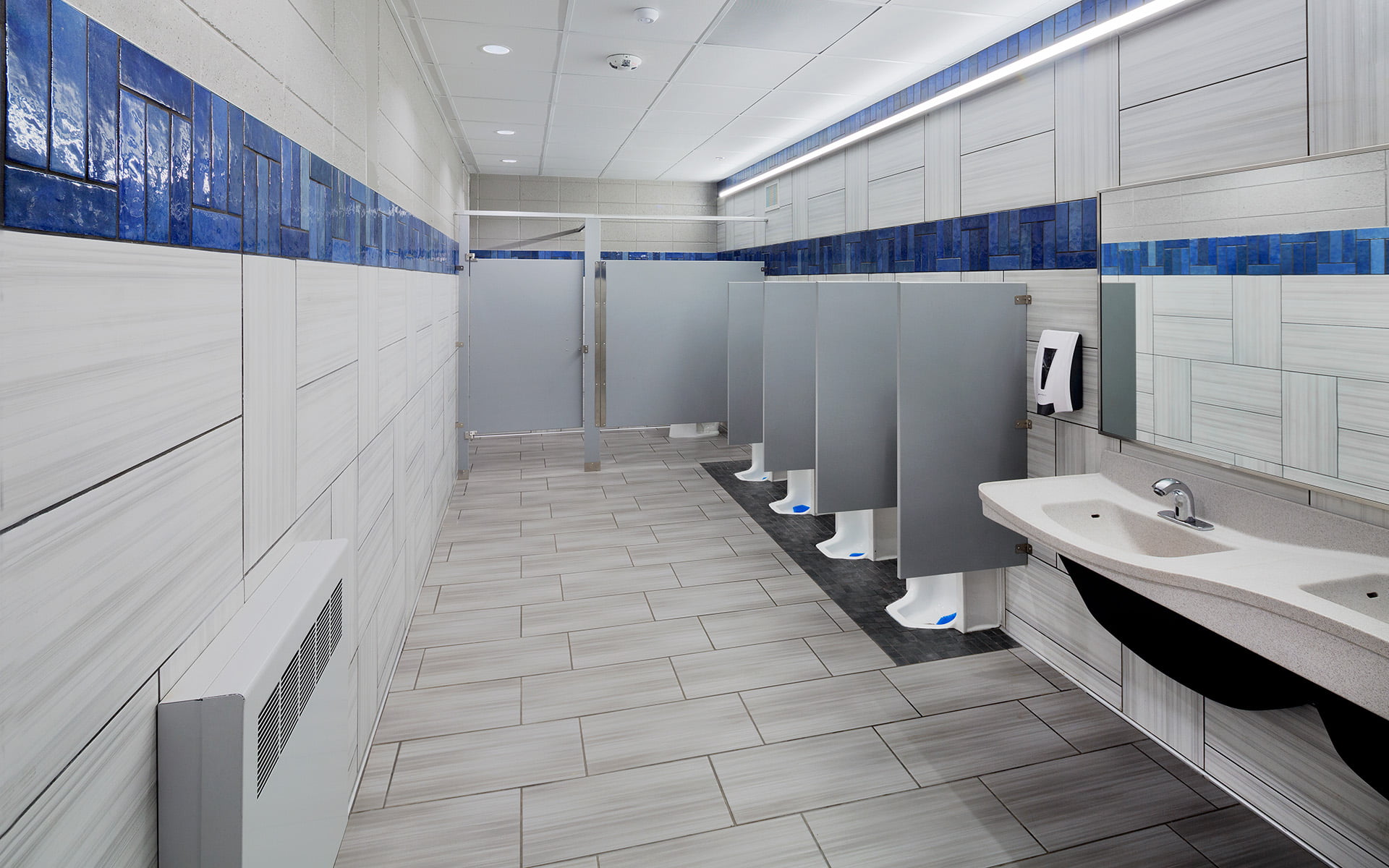
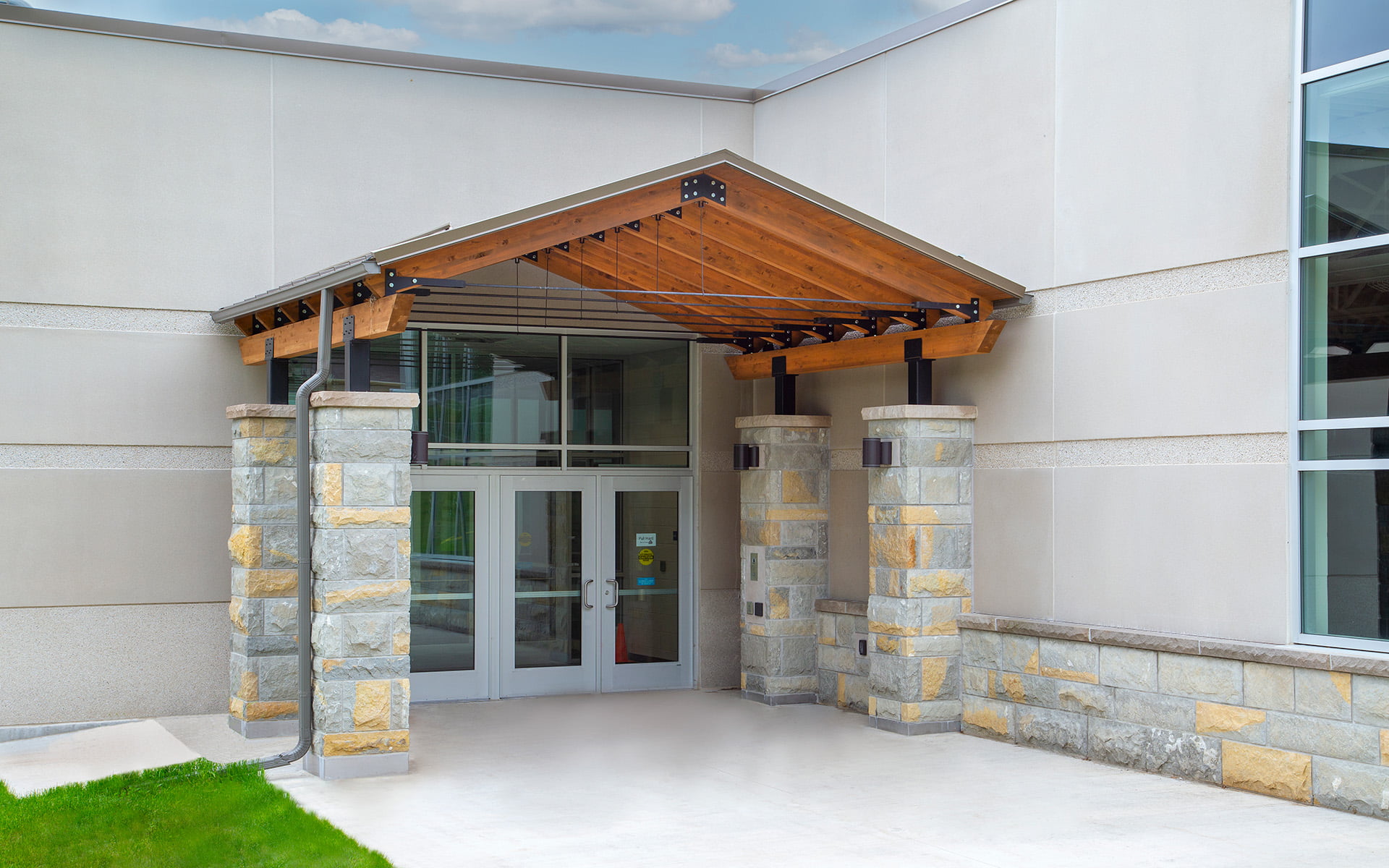
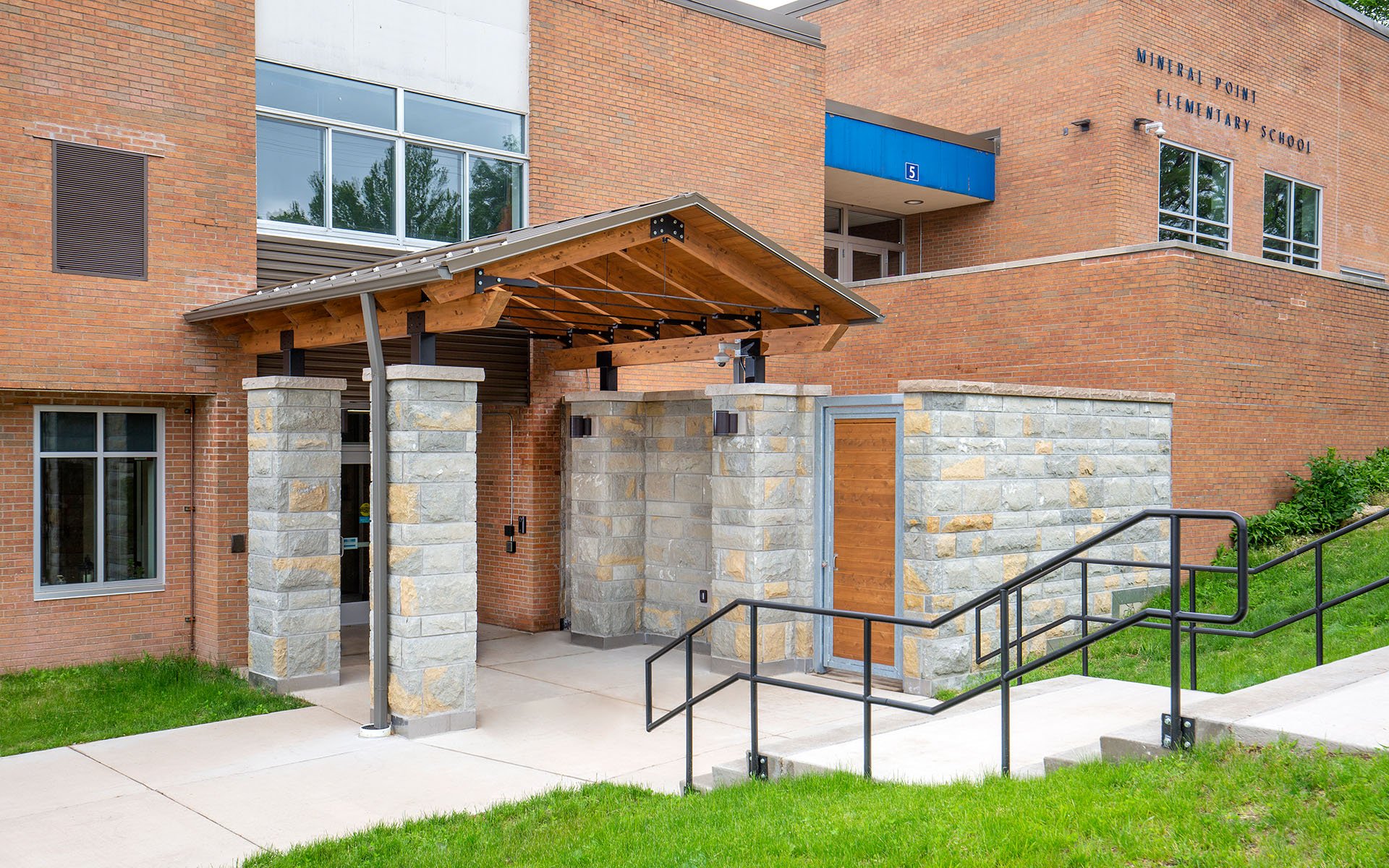
MINERAL POINT ELEMENTARY SCHOOL
Renovation & Addition
With the fall semester of 2021 fast approaching, Kraemer Brothers finished up the multi-year project for the Mineral Point School District on schedule, providing an exciting start to the school year! With the elementary school located on a steep, rocky hill in the middle of a residential neighborhood, careful site planning and extensive structural engineering was required during the construction process. The two-story addition features a new gymnasium and library/media center, while the existing school was remodeled to make way for updated offices, classrooms, and a cafeteria. Creating one cohesive look, Kraemer Brothers removed decades-old floor and wall tile, and replaced it with new tile and wood flooring that matches Mineral Point’s school colors, bringing extra pep to the school. To complete the transition from the existing building to the addition, a connecting bridge-walkway with a large, peaked glass roof was constructed for natural daylighting and an updated modern look. In an effort to make the new building energy efficient, MEP upgrades and automatic light fixtures with zoned lighting were added to freshen up this vintage elementary school, presenting a brand-new school feel.
- 2022 ABC Projects of Distinction
From the Client
Kraemer Brothers is an outstanding company and worked with us in a team approach. We never felt like our ideas were not being heard. As the project progressed, our staff felt like we were part of their company with our inclusion in weekly meetings that kept us informed at every step of the way throughout our building project.
Mitch Wainwright
District Administrator | Mineral Point School District
Promega Corporation – Chappelle Manufacturing Center
SCIENCE & TECHNOLOGY PORTFOLIO
PROMEGA CORPORATION
CHAPPELLE MANUFACTURING CENTER
Madison, WI
Overview
ARCHITECT
Flad Architects
Square Footage
160,000
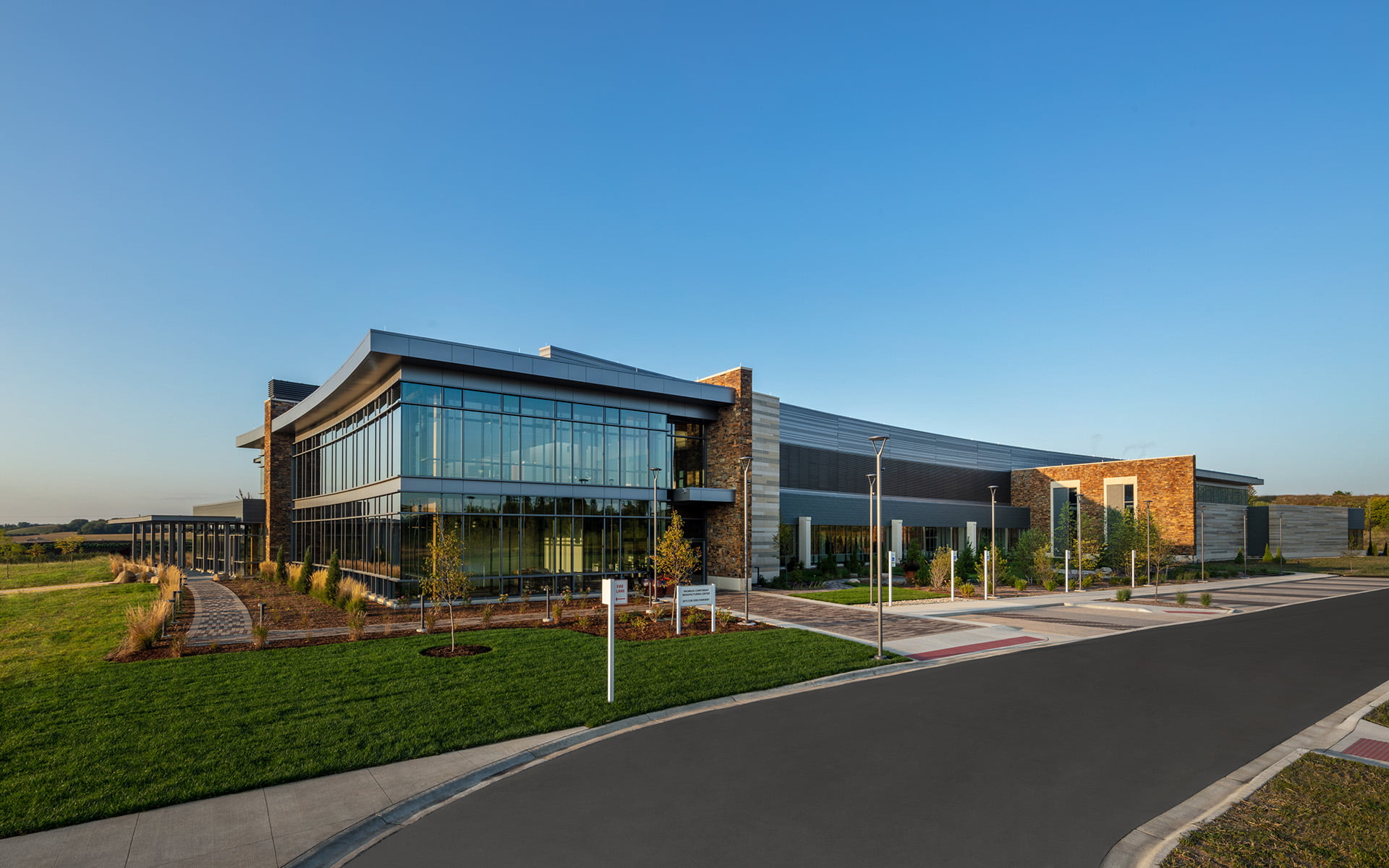
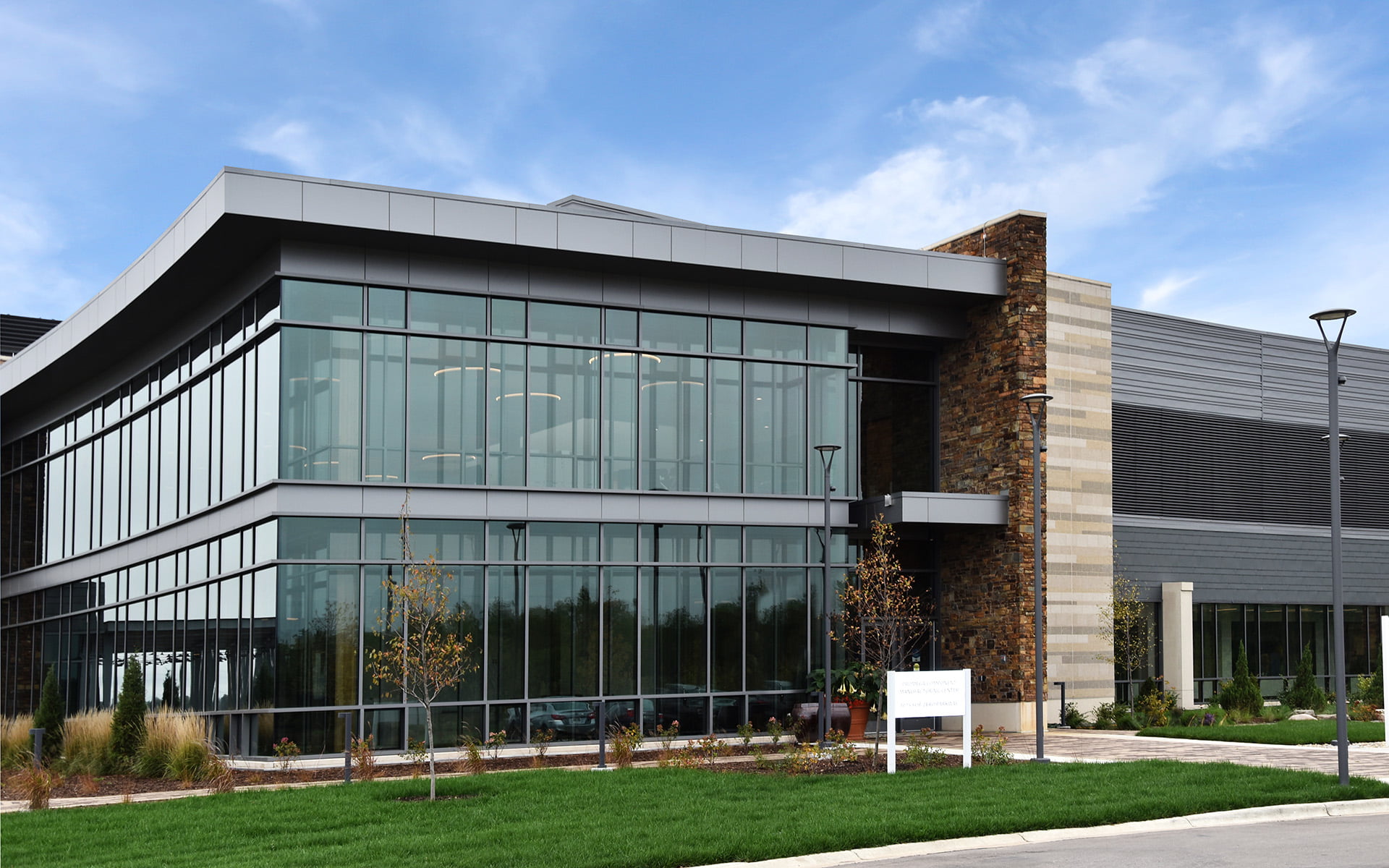

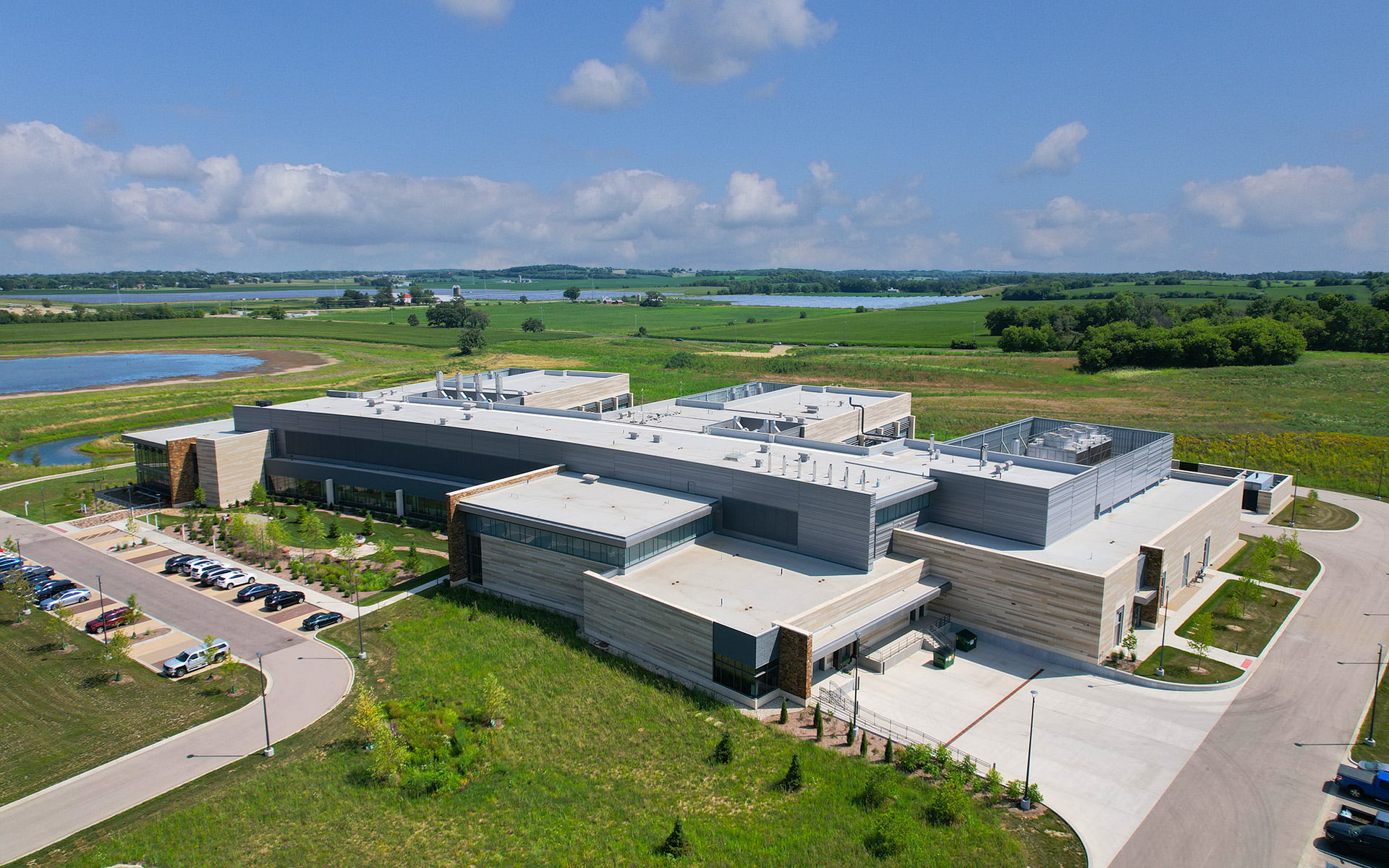
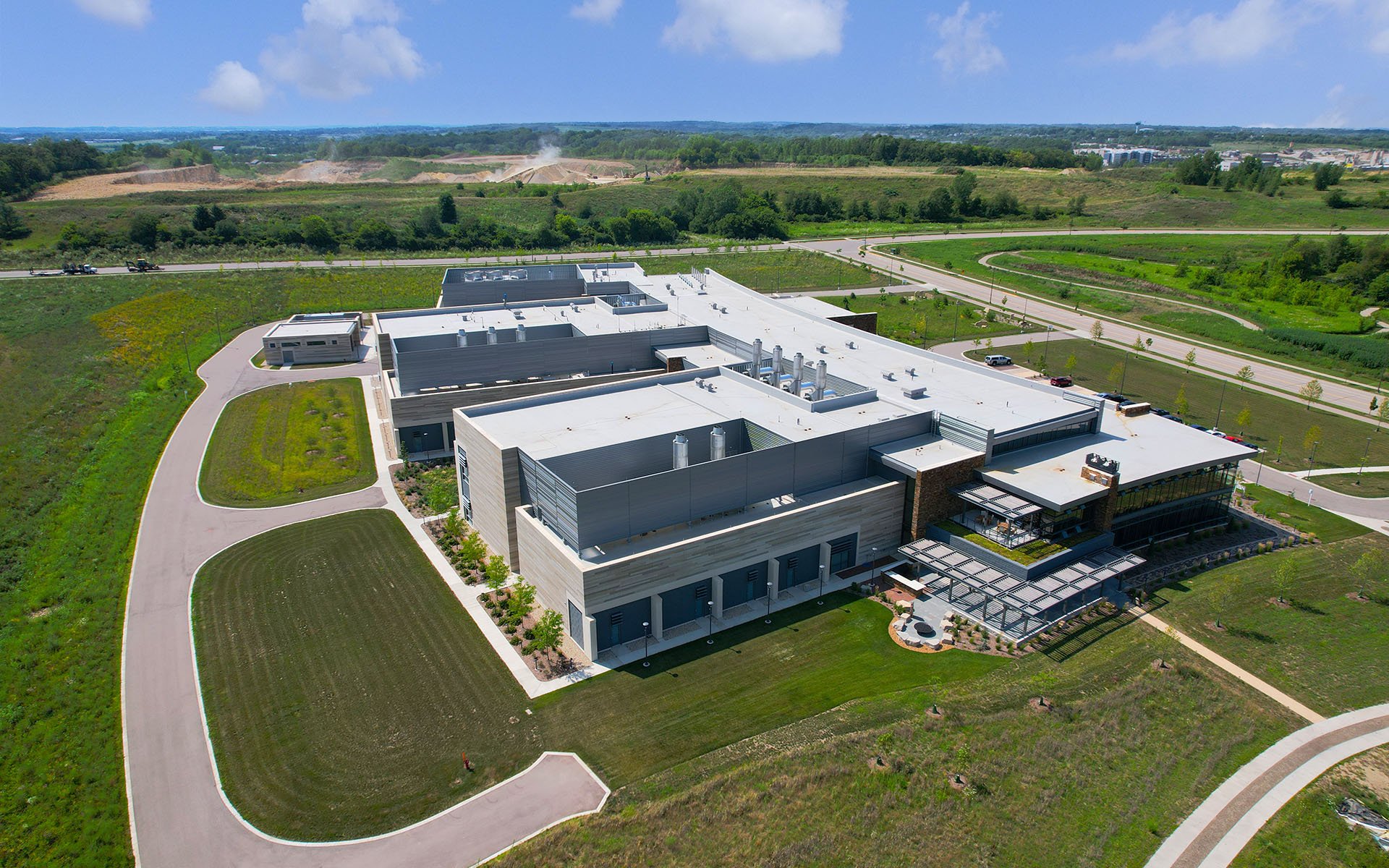
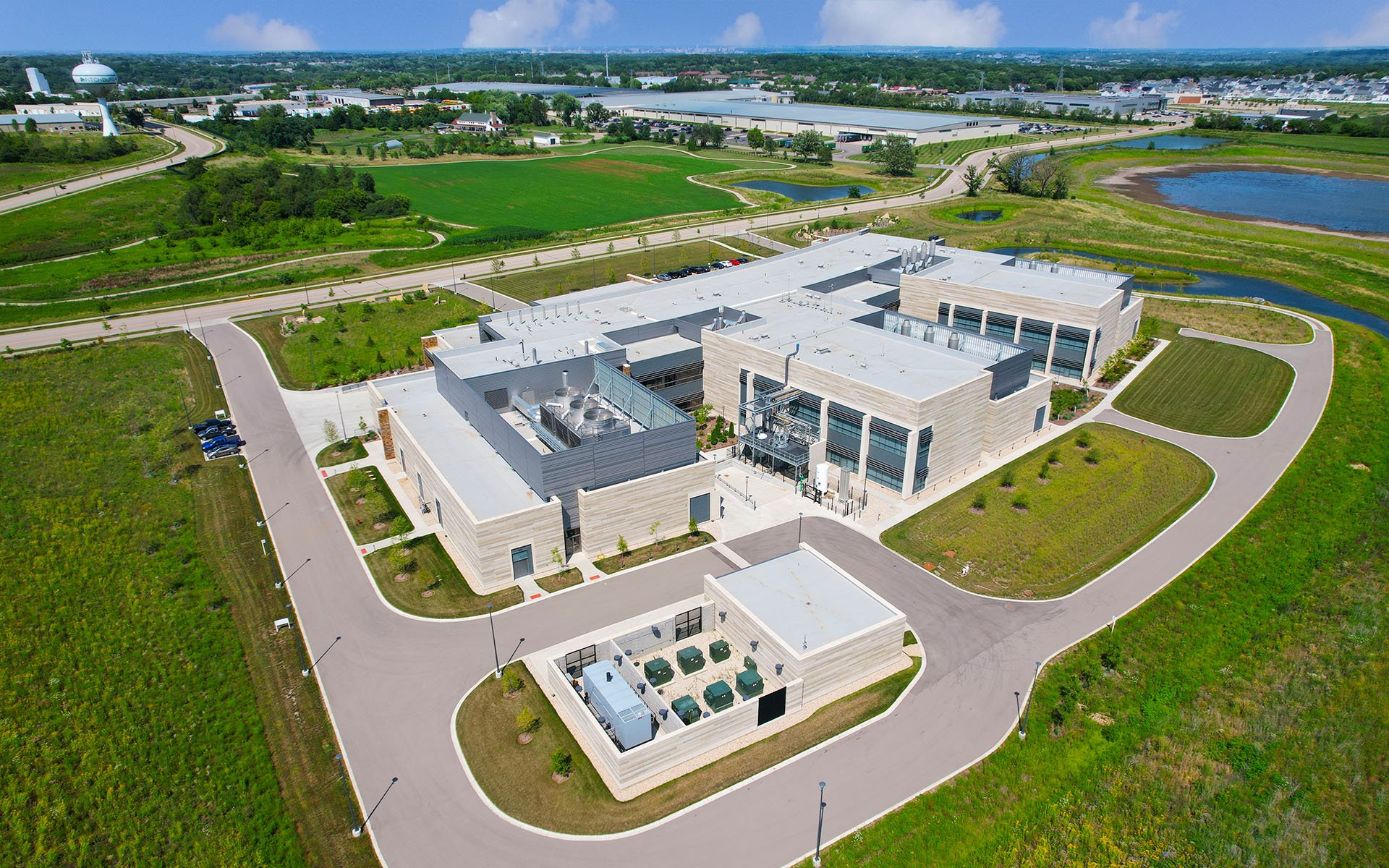
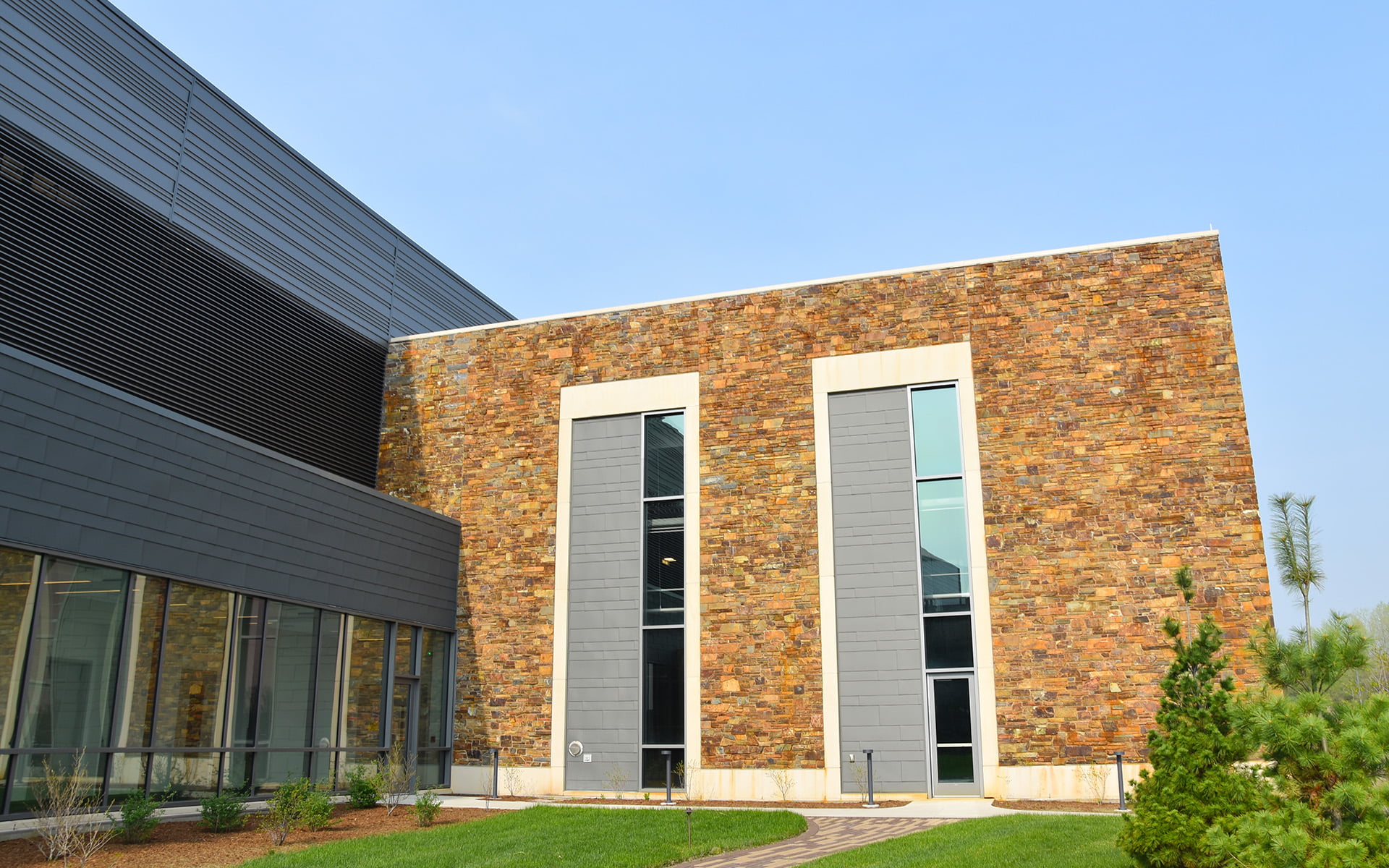
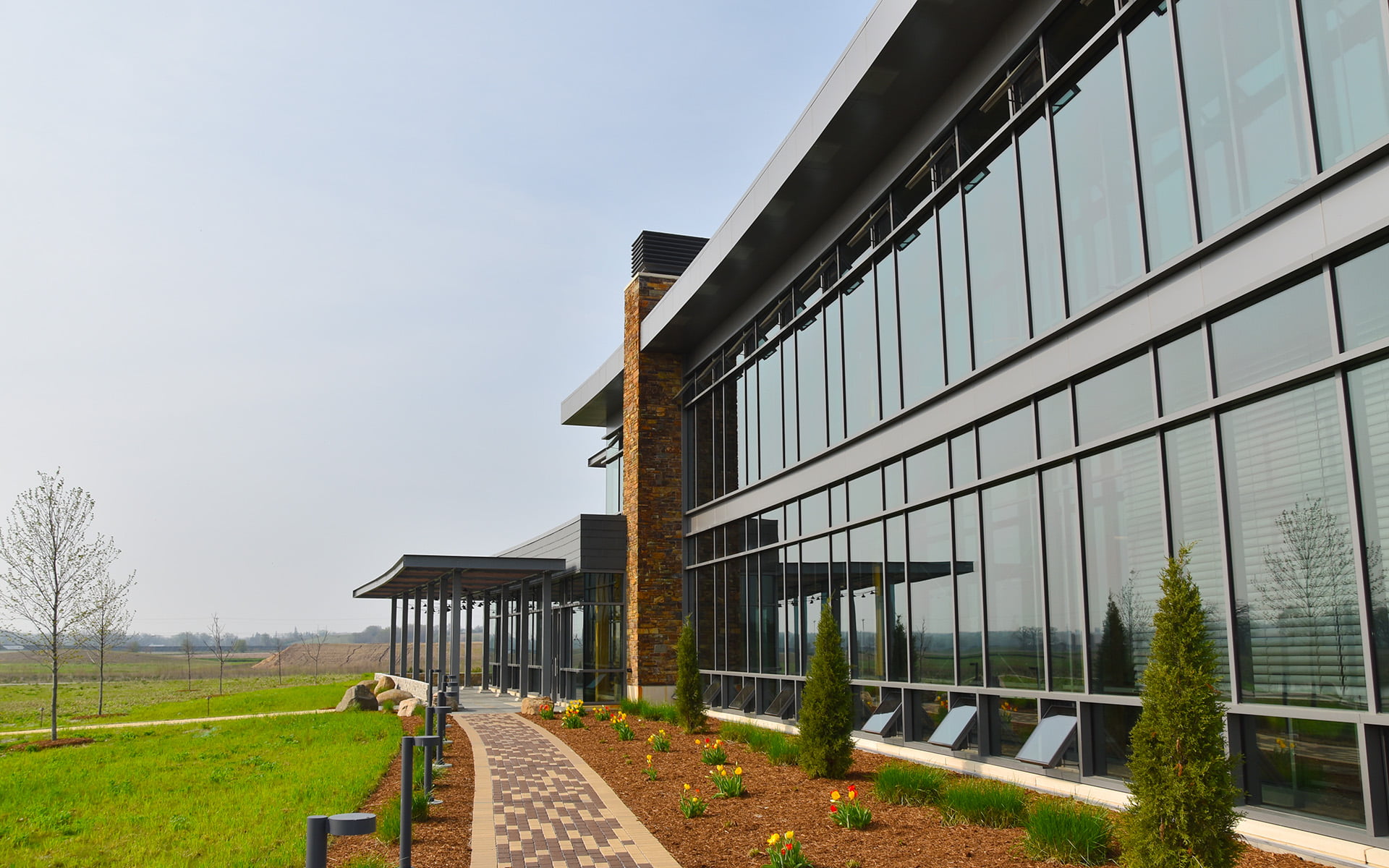
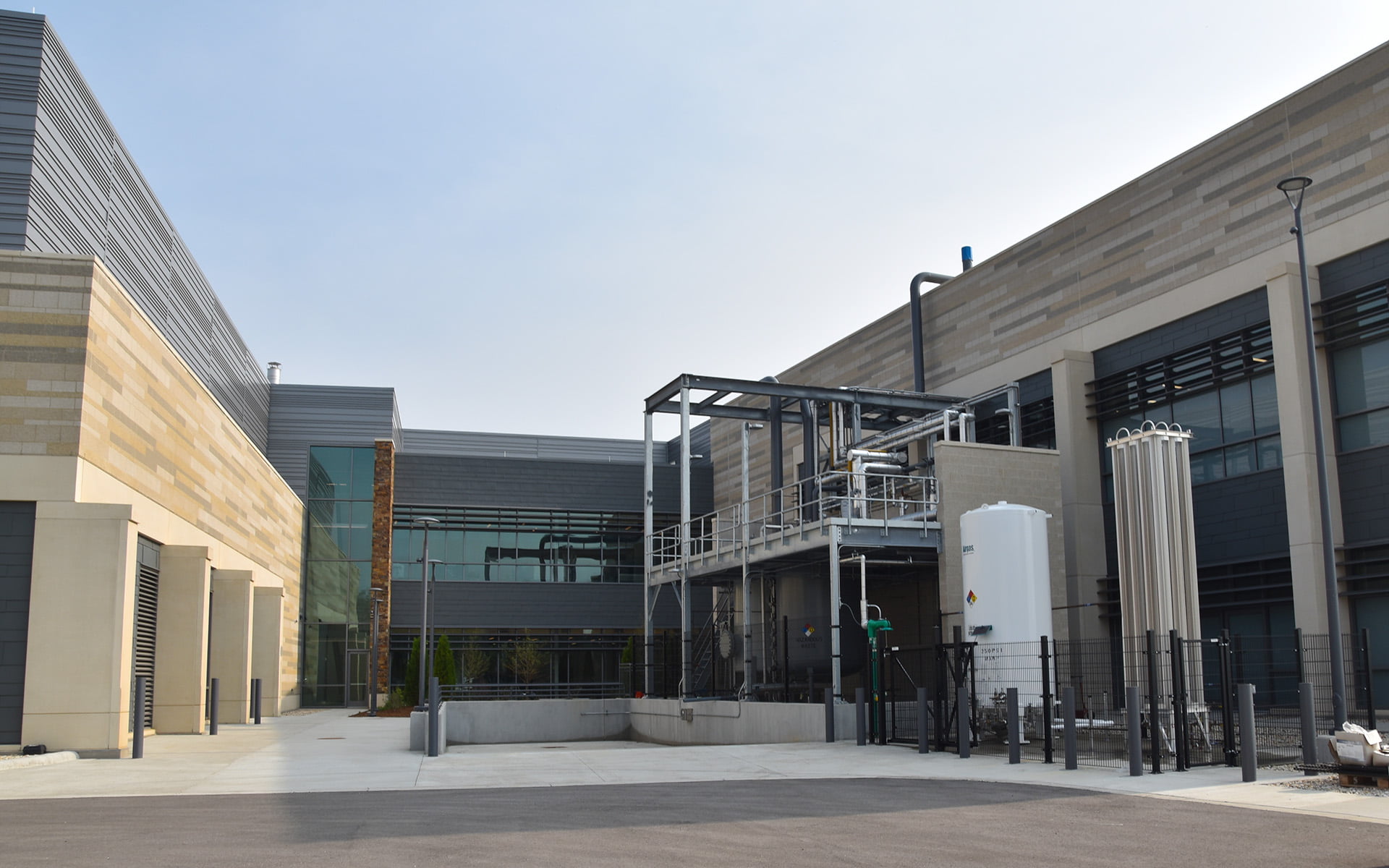
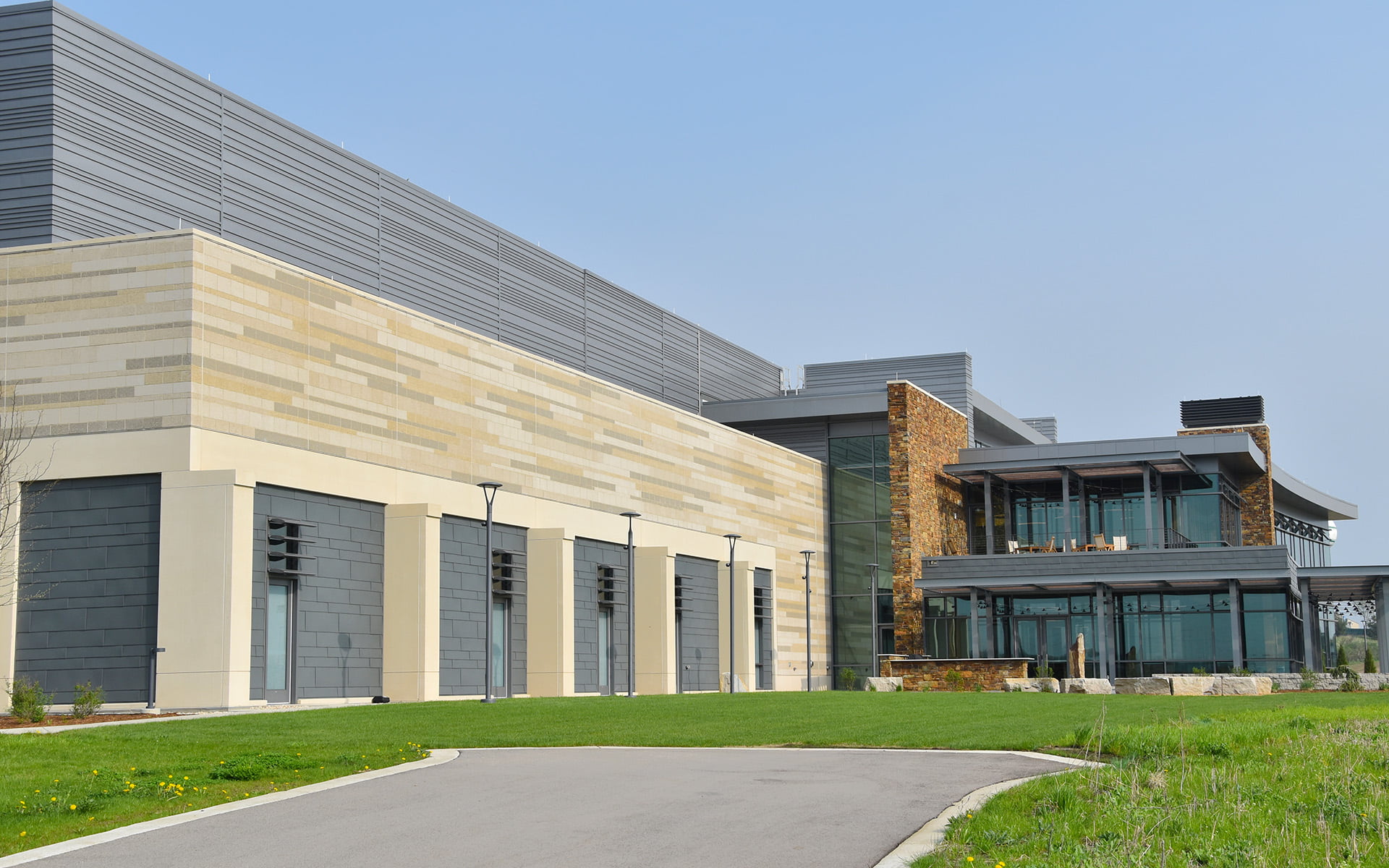
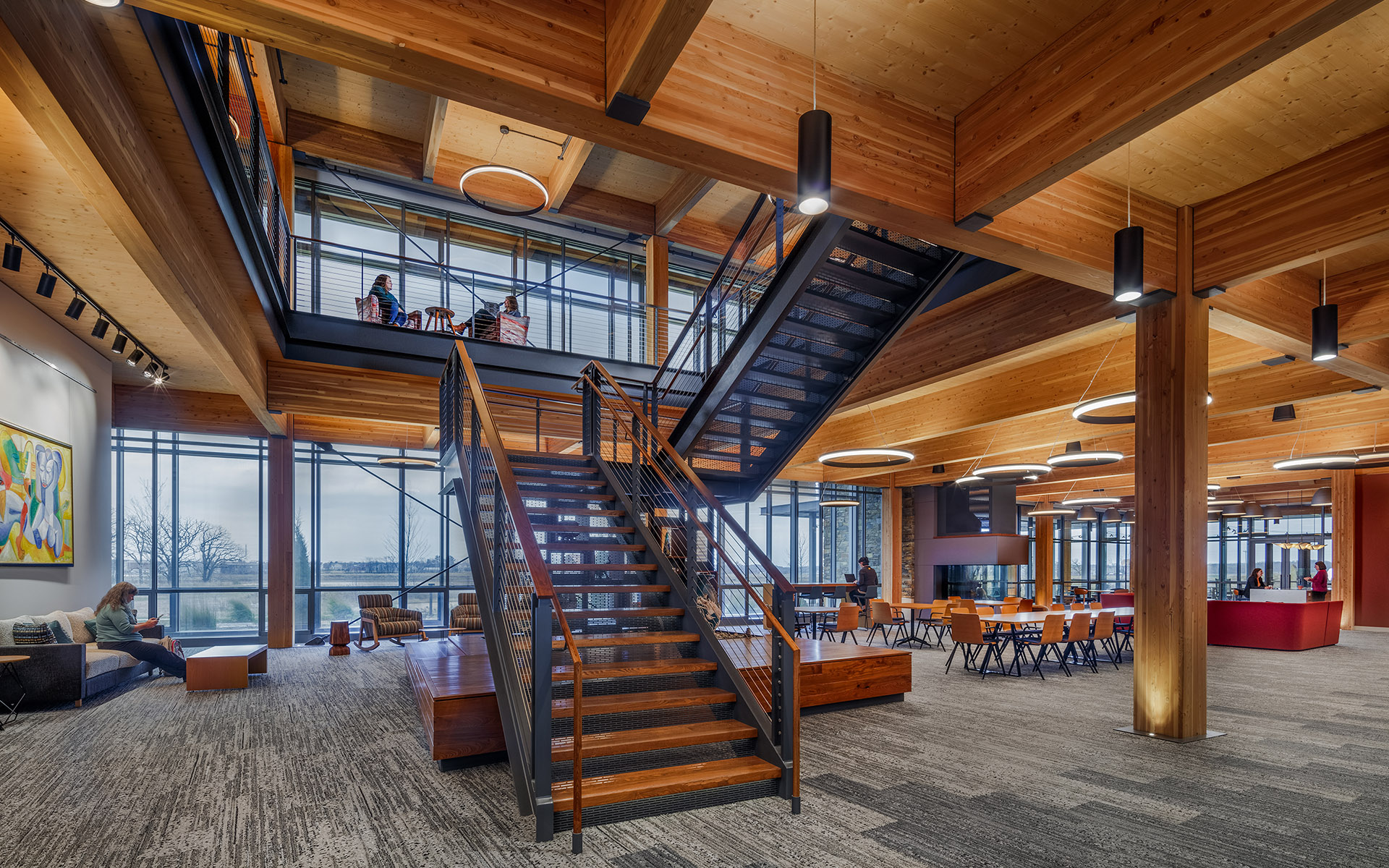
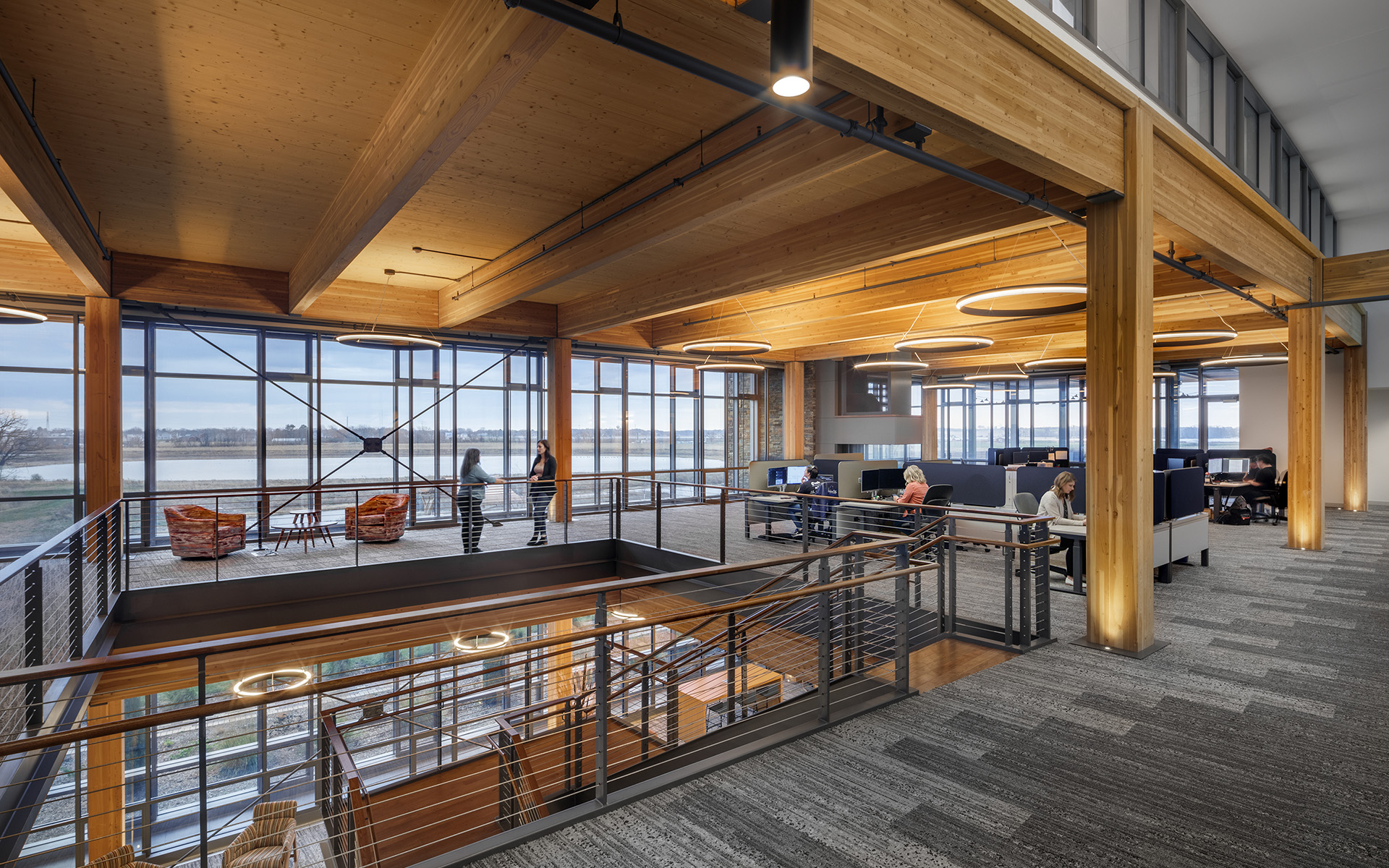
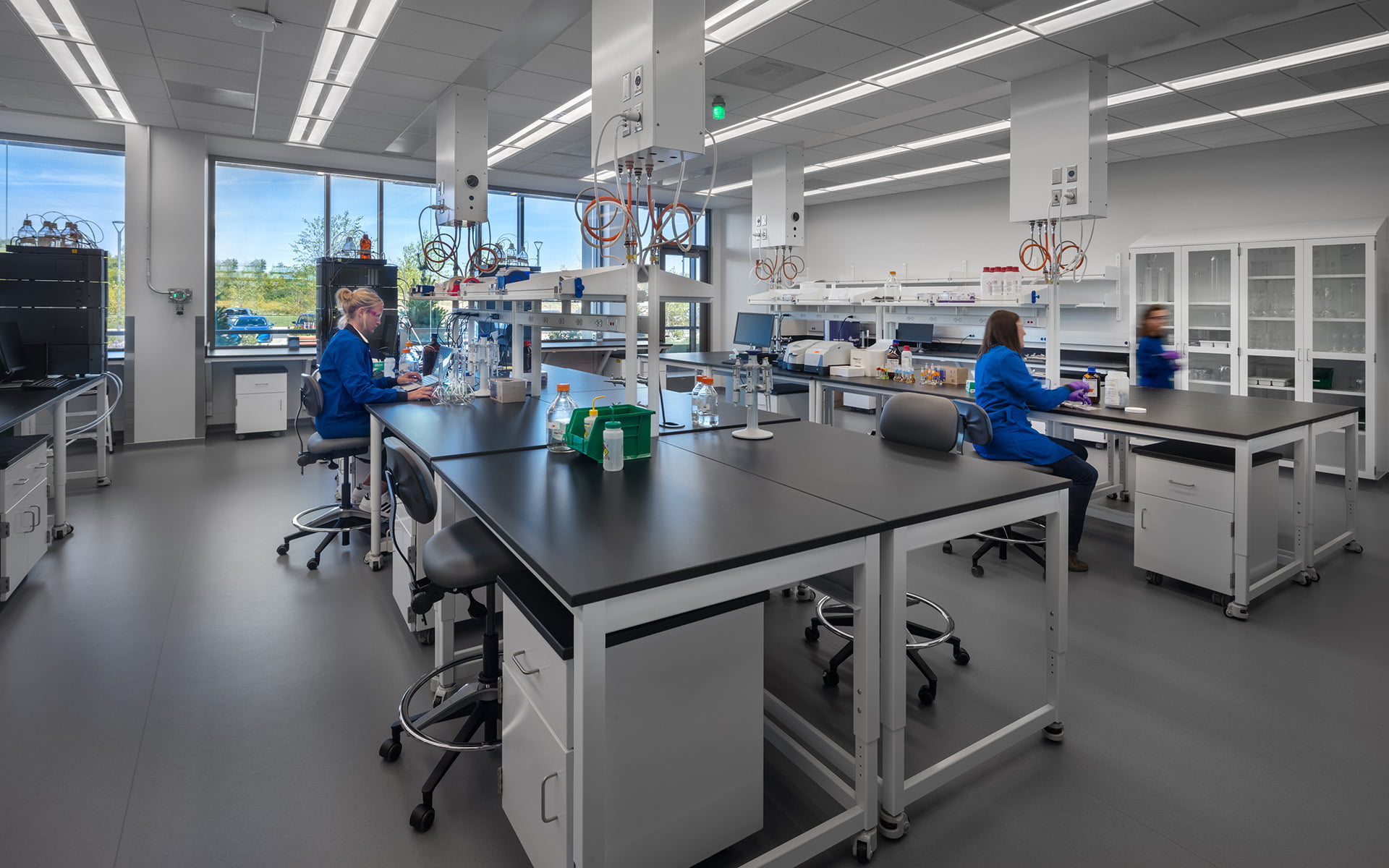
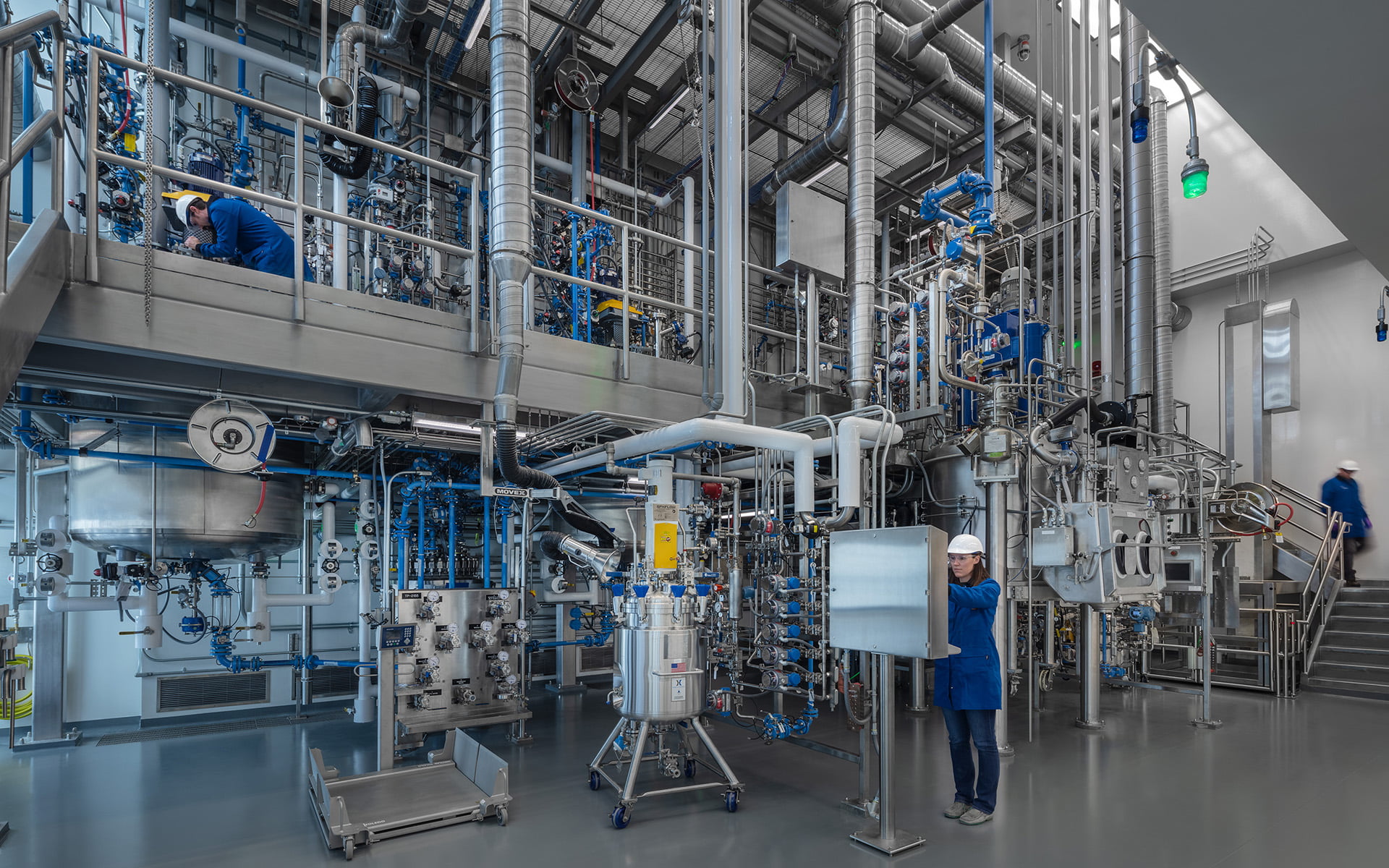
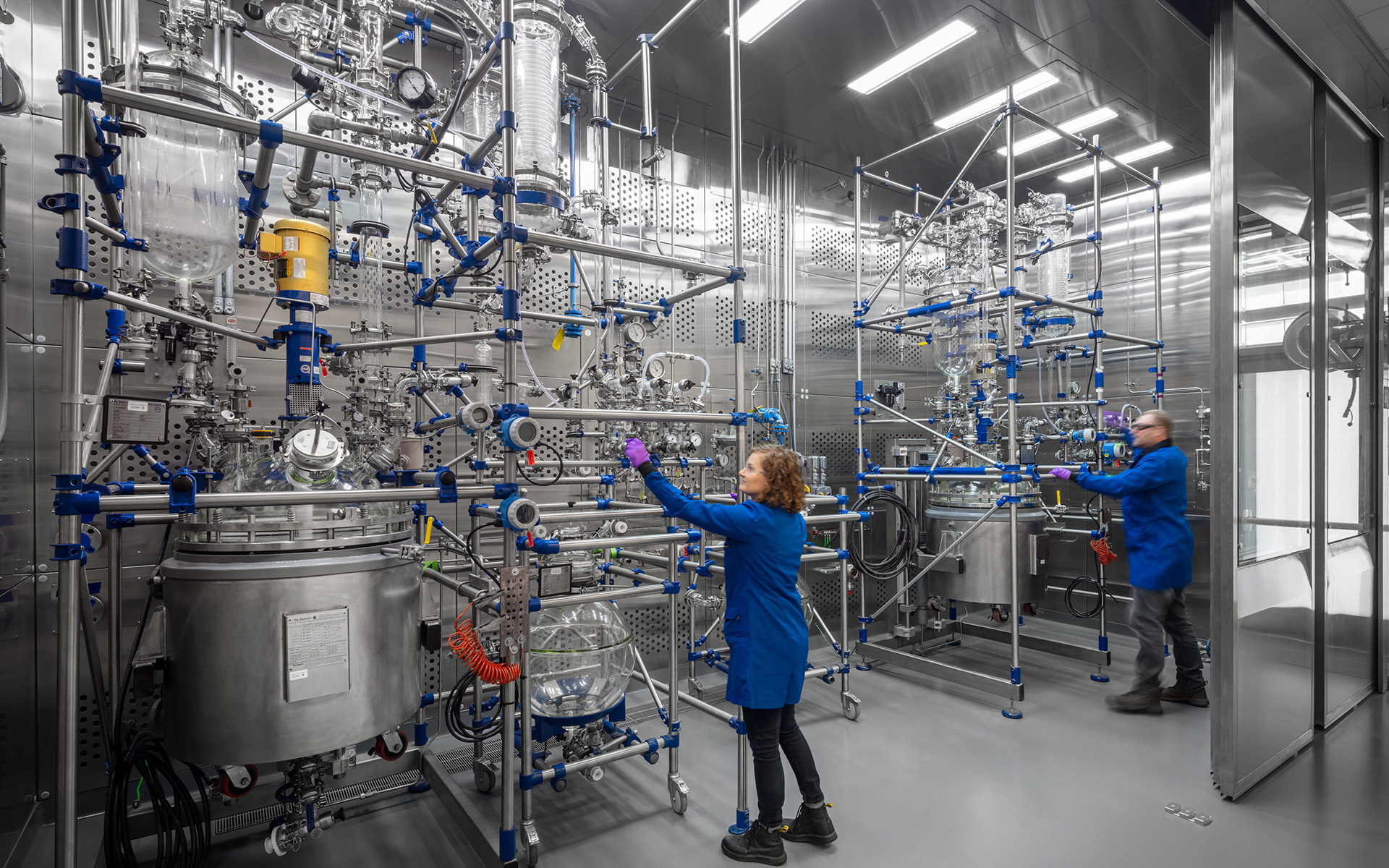
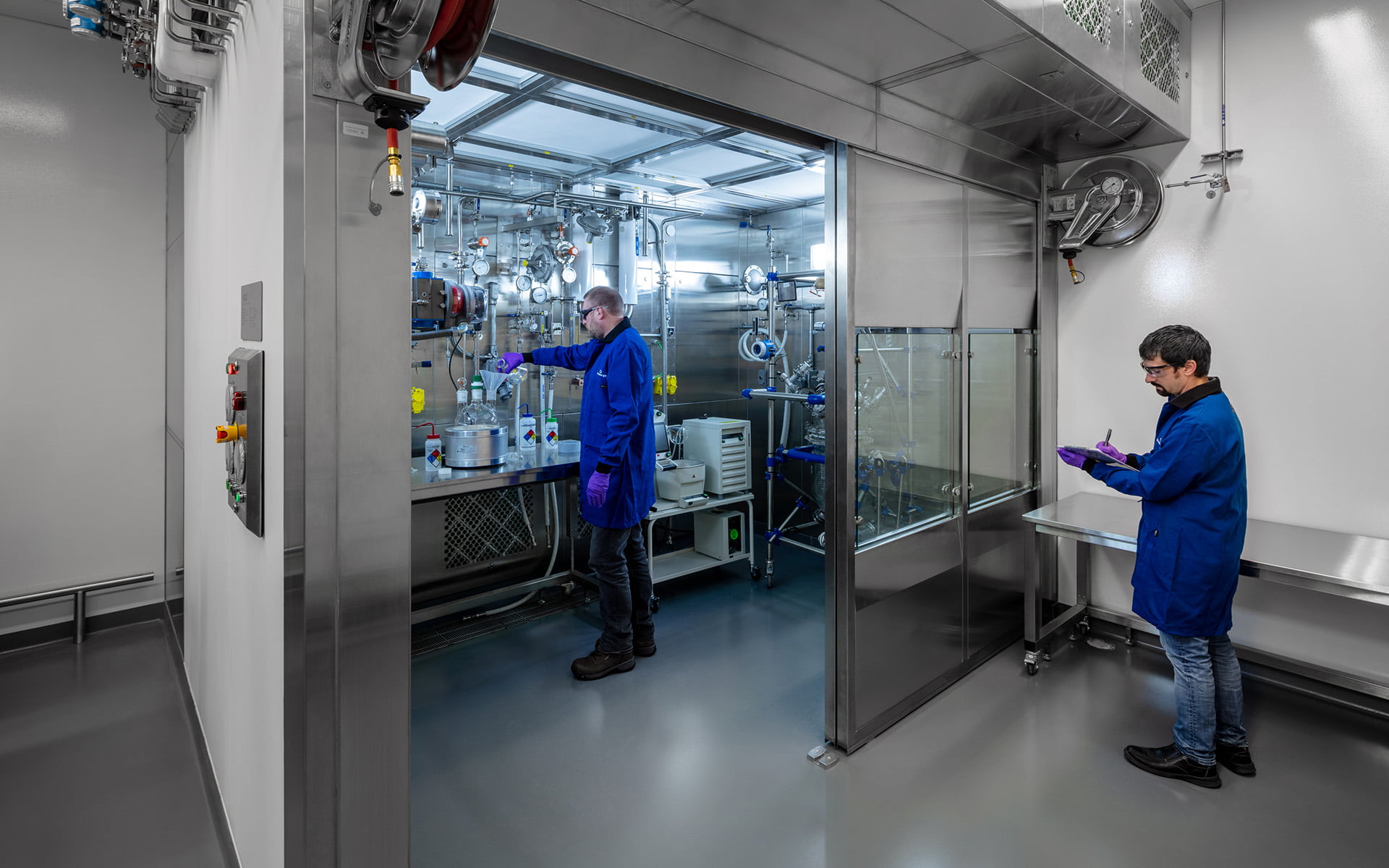
CHAPPELLE MANUFACTURING CENTER
Manufacturing Facility
Located three miles from Promega’s main campus, Chappelle Manufacturing Center (CMC) provides connection to the outdoors in the design elements. This manufacturing facility produces small molecule components used in many of Promega’s products. Using nearly half of the building to support the mechanical process systems, this advanced facility design is focused on safety in its manufacturing capabilities of large, small, and kilo scale synthetic organic chemistry. With room for future expansion, this building has many sustainable features such as a double-glass wall system around the office portion of the building which is used to maximize the temperature of the interior of the building, and a rainwater reuse system for the building’s mechanical cooling and heating of water. Walking trails surround the facility leading to a bridge over a pond with an island full of native grasses and flowers. Large limestone rock slabs located near the entrance to the facility provide a remembrance of the surrounding landscape. Using a combination of real stone exterior walls, contrasting brick colors, glass windows and metal accents, this building symbolizes the modern and futuristic capabilities of molecular manufacturing.
- 2021 Daily Reporter Top Projects
- 2022 Wisconsin Masonry Alliance Excellence in Masonry
- 2022 ABC Projects of Distinction
- 2022 InBusiness Commercial Design Award
- 2023 Dane County Climate Champion
RELATED
From the Client
The Promega Chappelle Manufacturing Center is a highly complex facility using nearly half of the building to support the mechanical process systems. This advanced facility design is focused on safety in its manufacturing process. With room for future expansion, the building has many sustainable features such as a double-glass wall system around the office portion of the building which is used to maximize the temperature efficiency of the interior of the building. Onsite Kraemer Brothers management was able to keep up with the fast pace and aggressive project schedule of this project. They area a huge reason for the success of this project.
Eric Loucks
Director of Facilities | Promega Corporation
St. Andrew Lutheran Church Westside Christian School
RELIGIOUS PORTFOLIO
St. andrew lutheran church - WESTSIDE CHRISTIAN SCHOOL
Middleton, WI
Overview
ARCHITECT
Zimmerman Architectural Studios
Square Footage
8,500
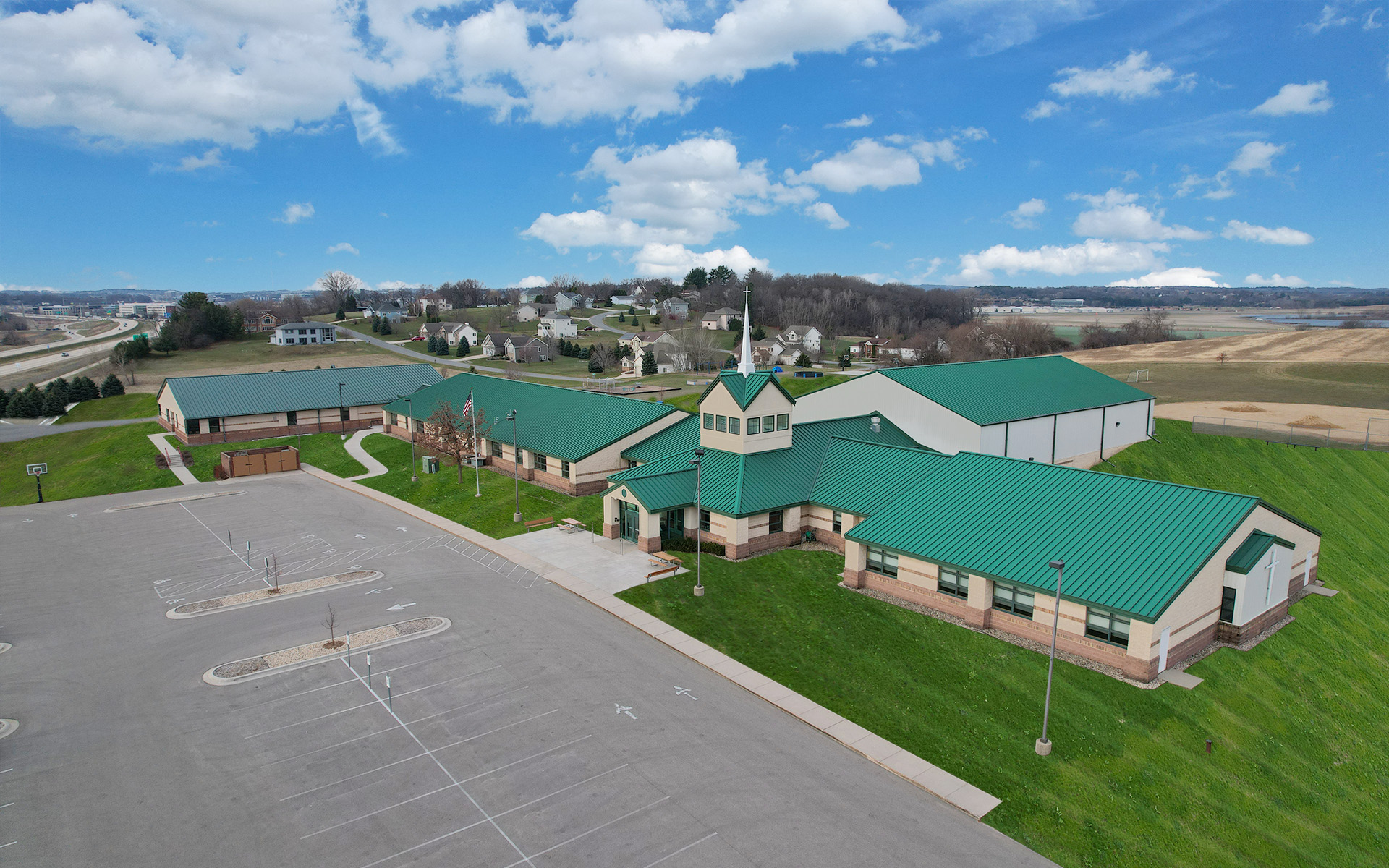
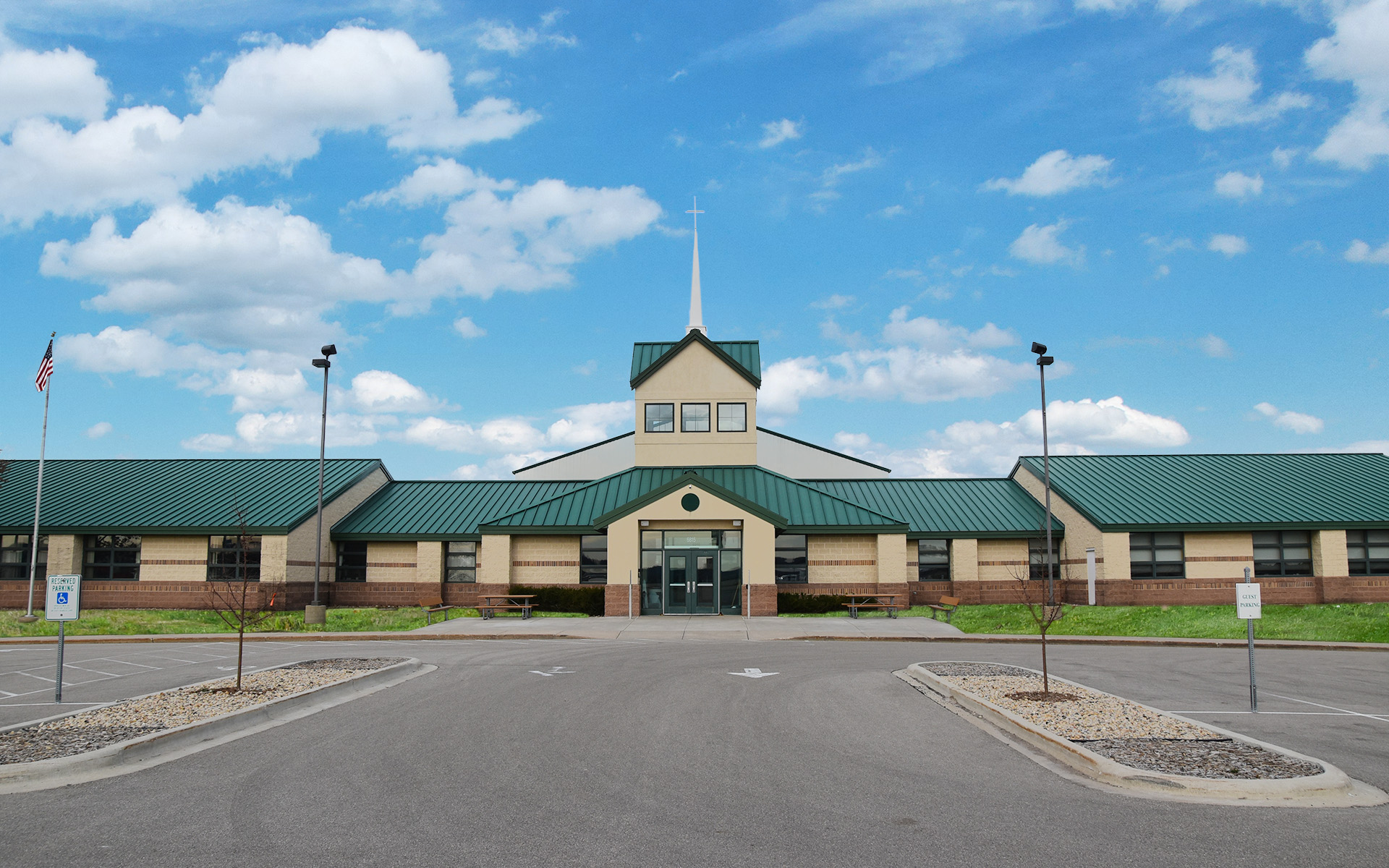
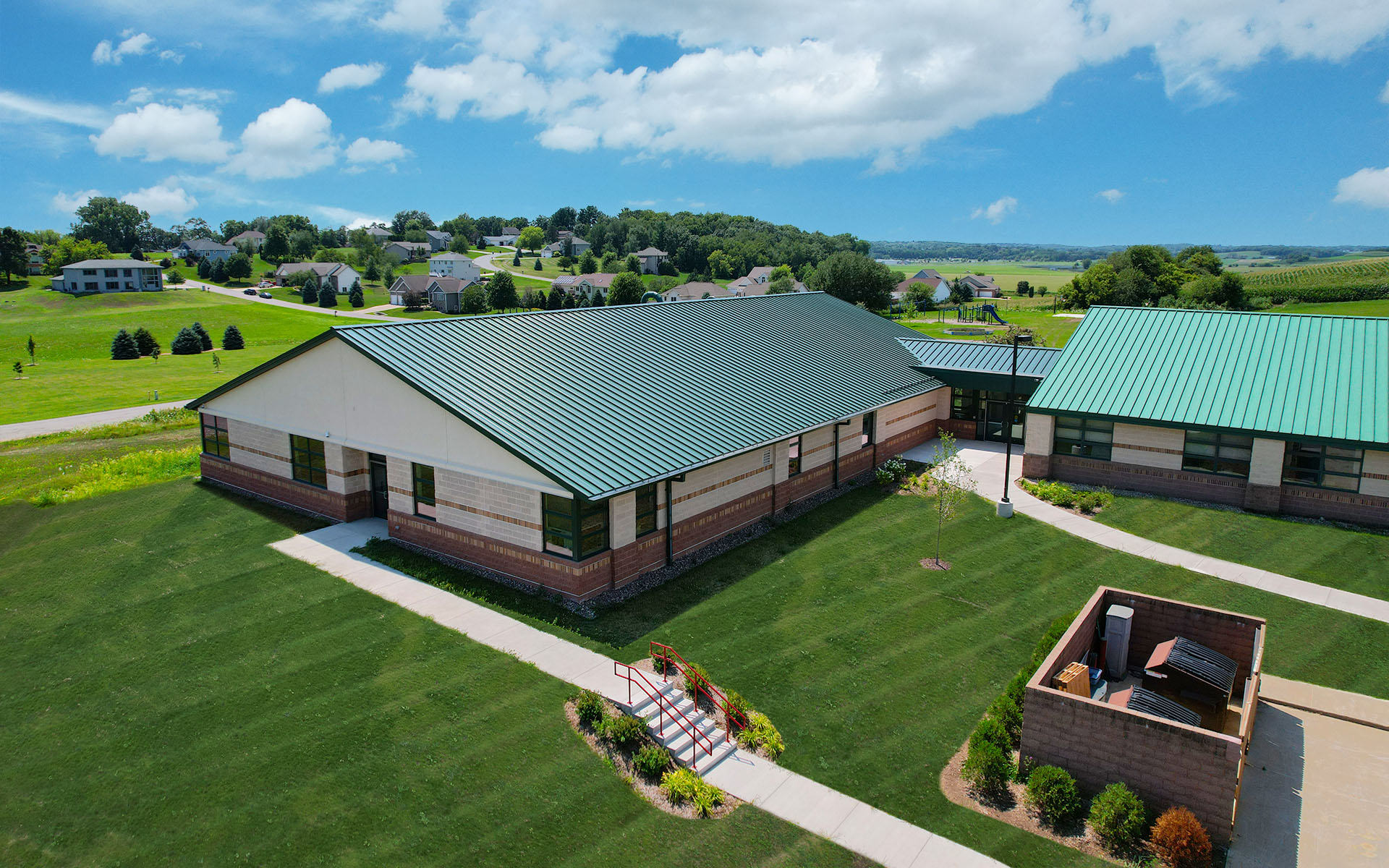
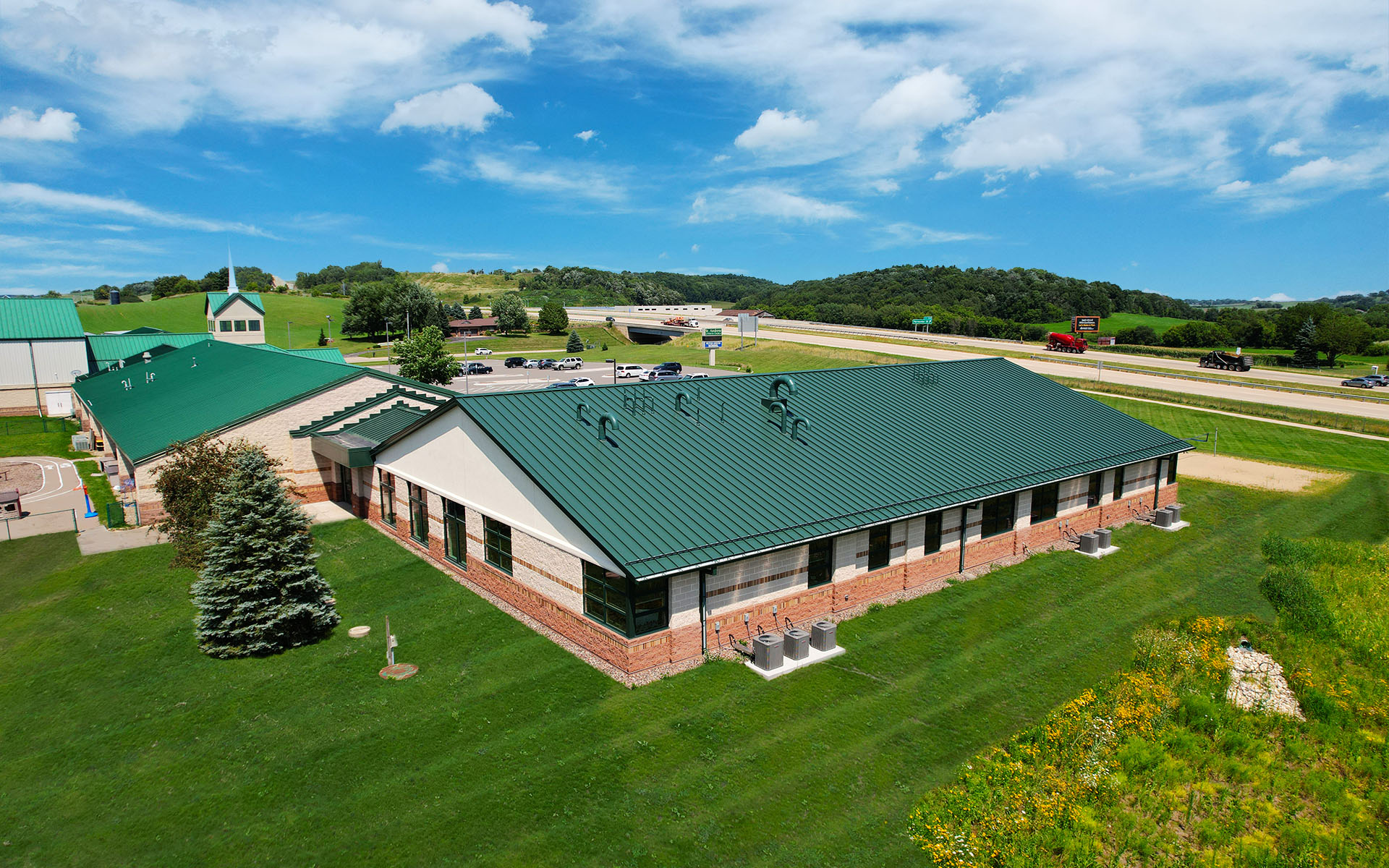
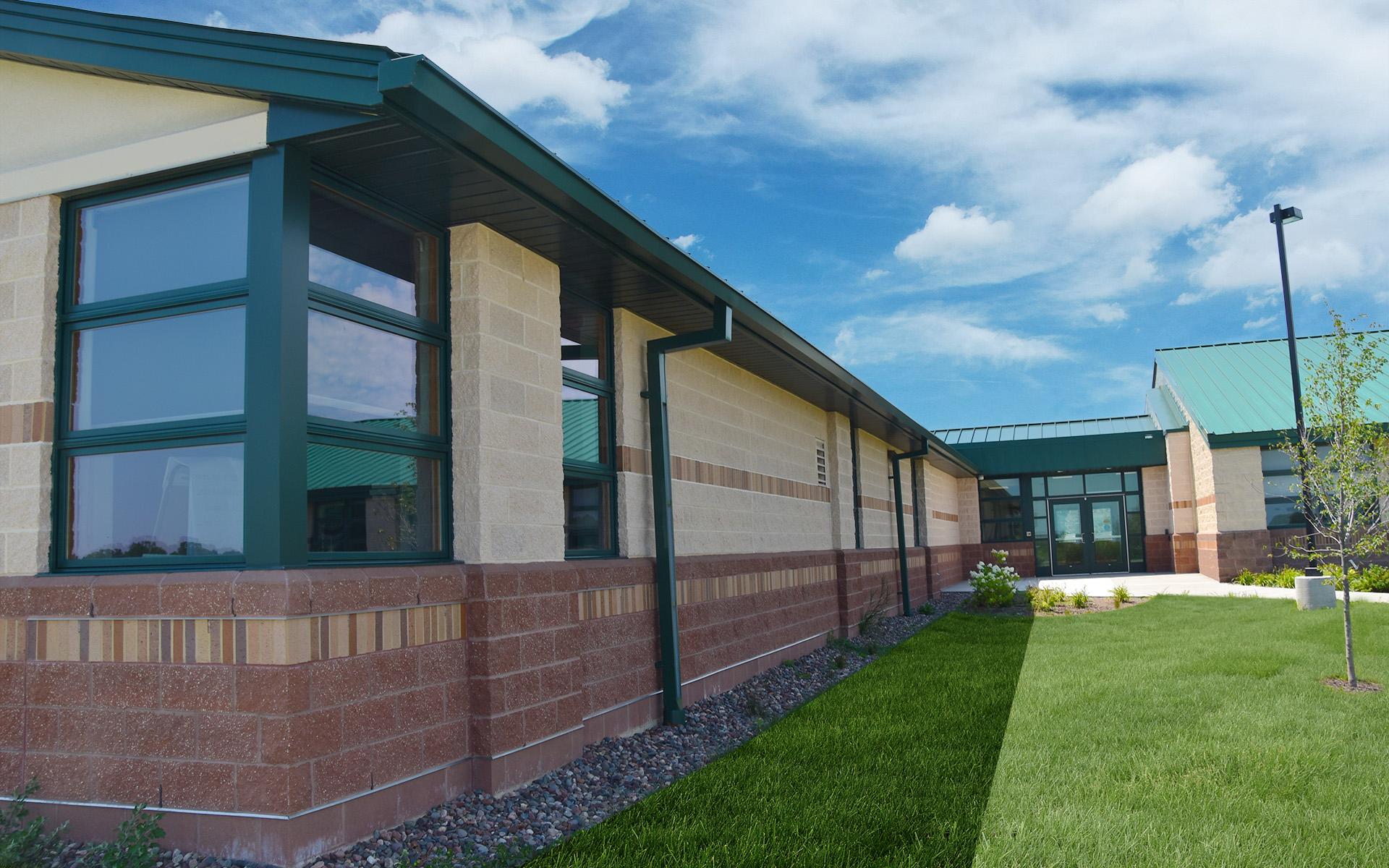
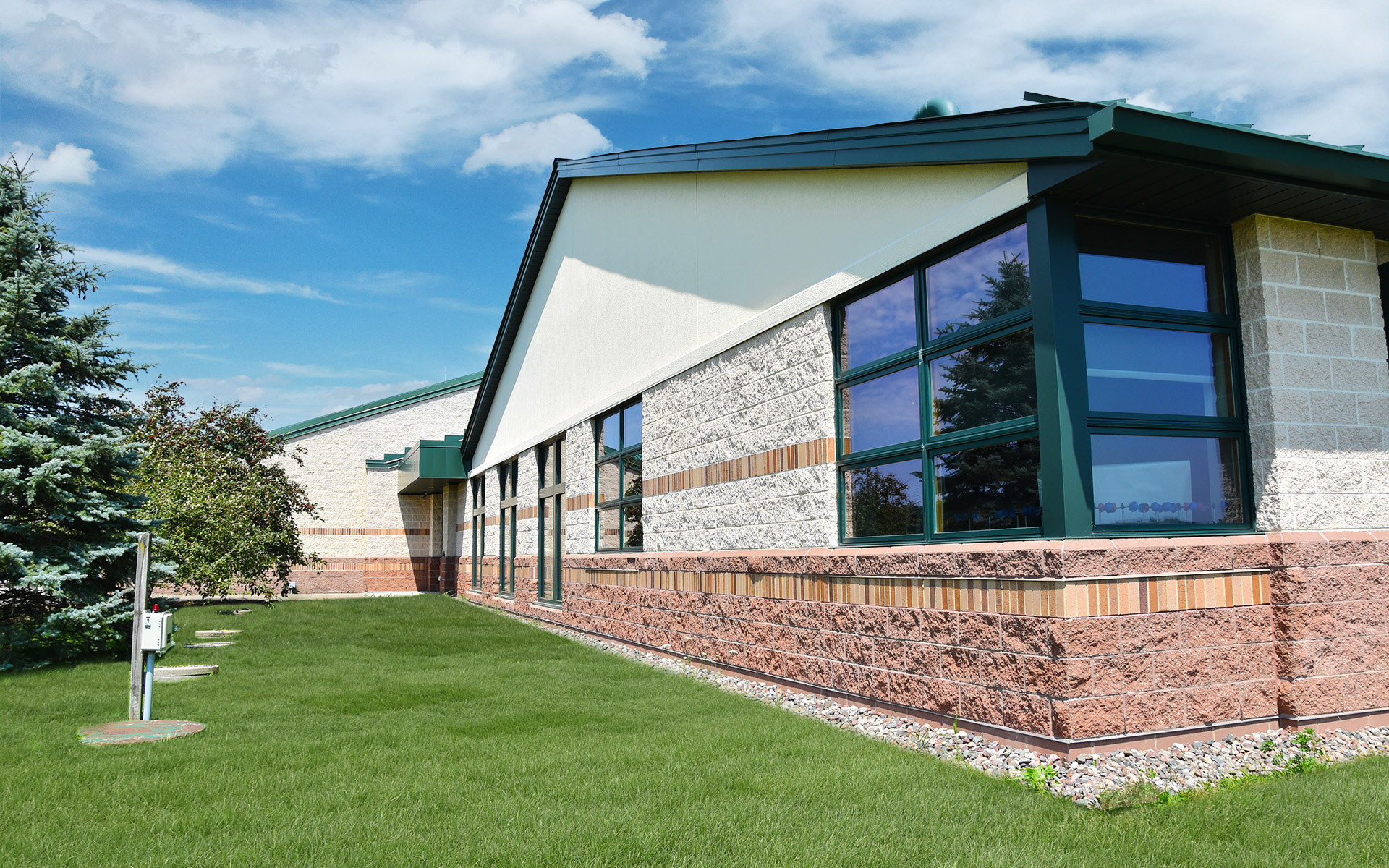
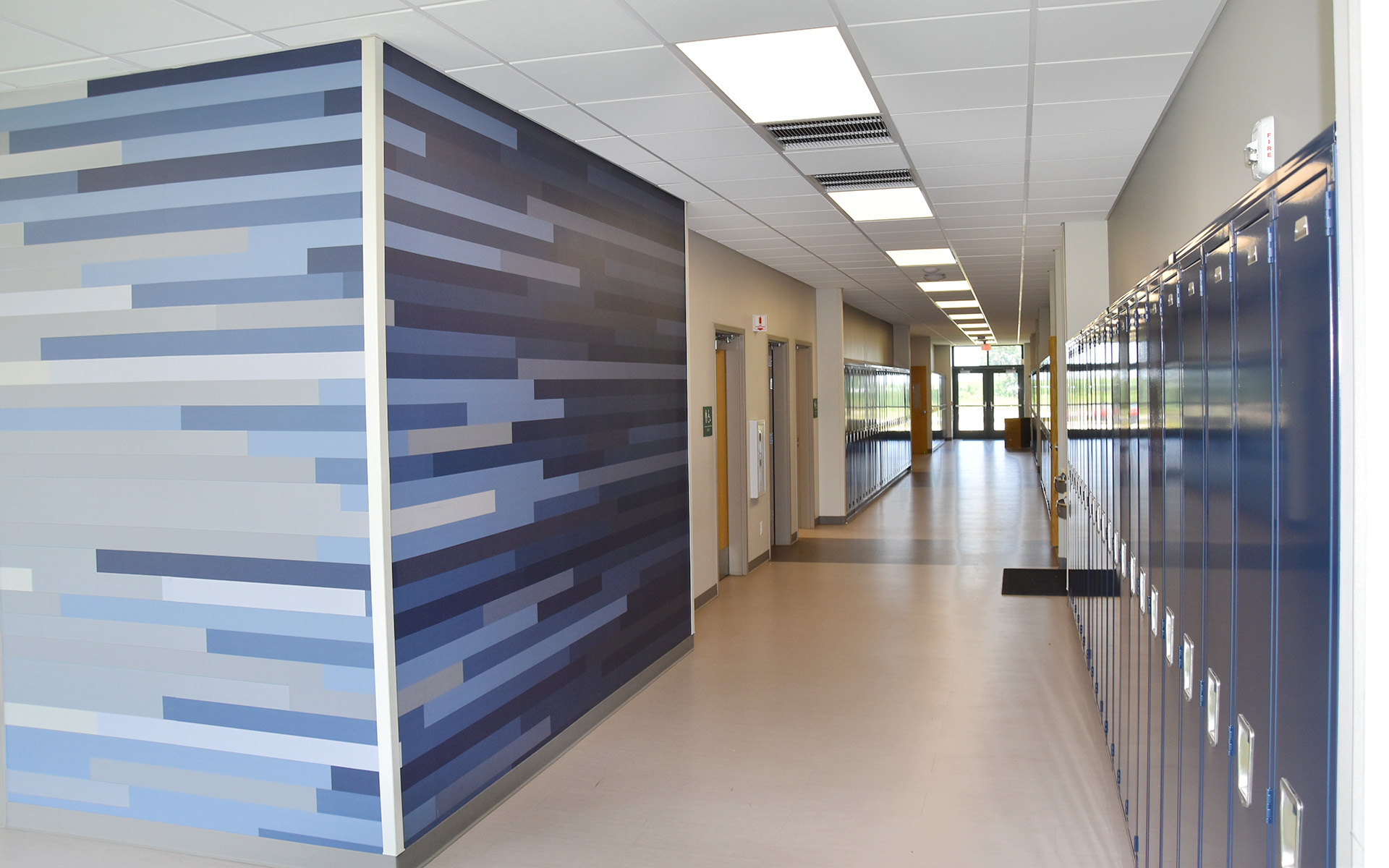
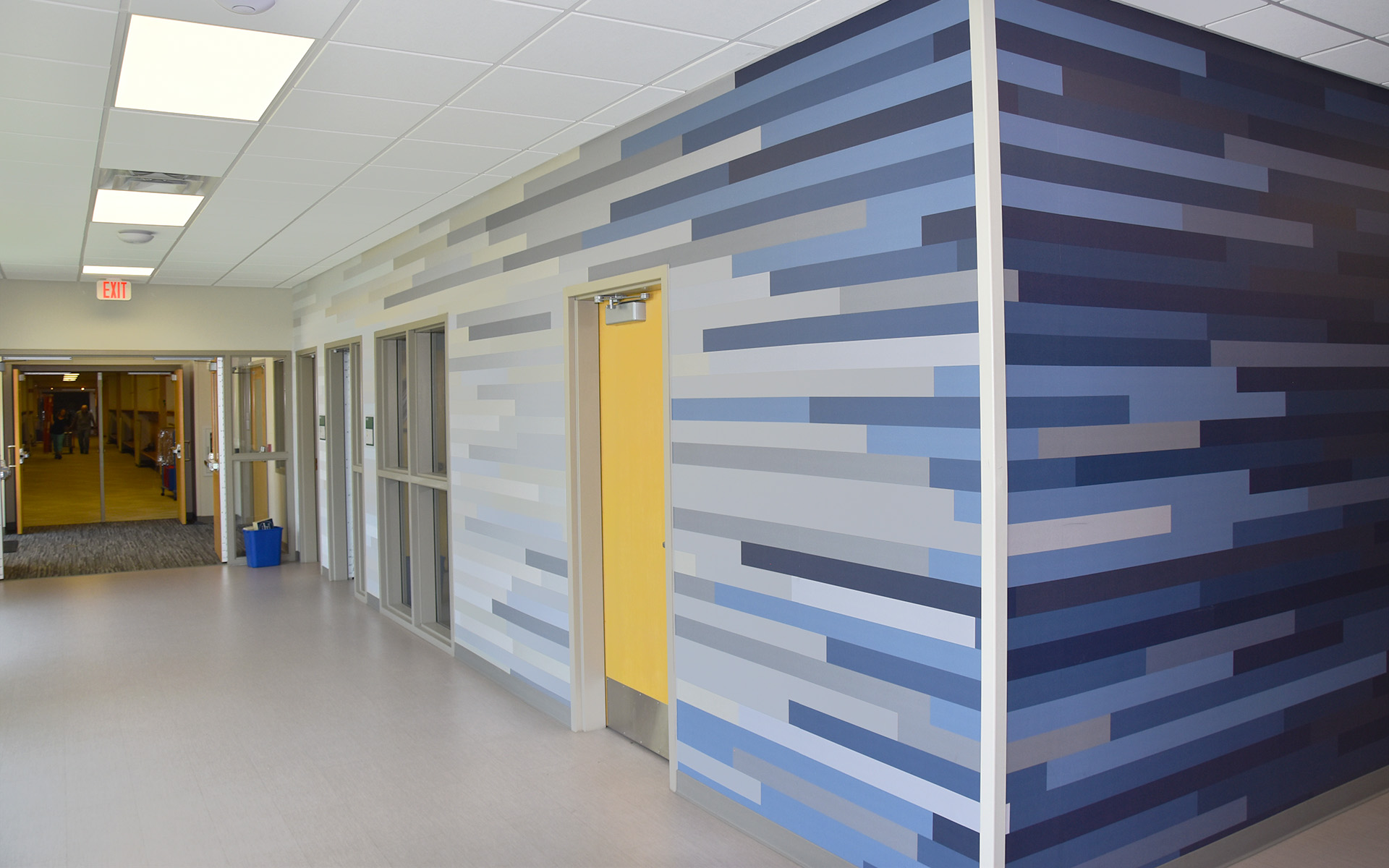
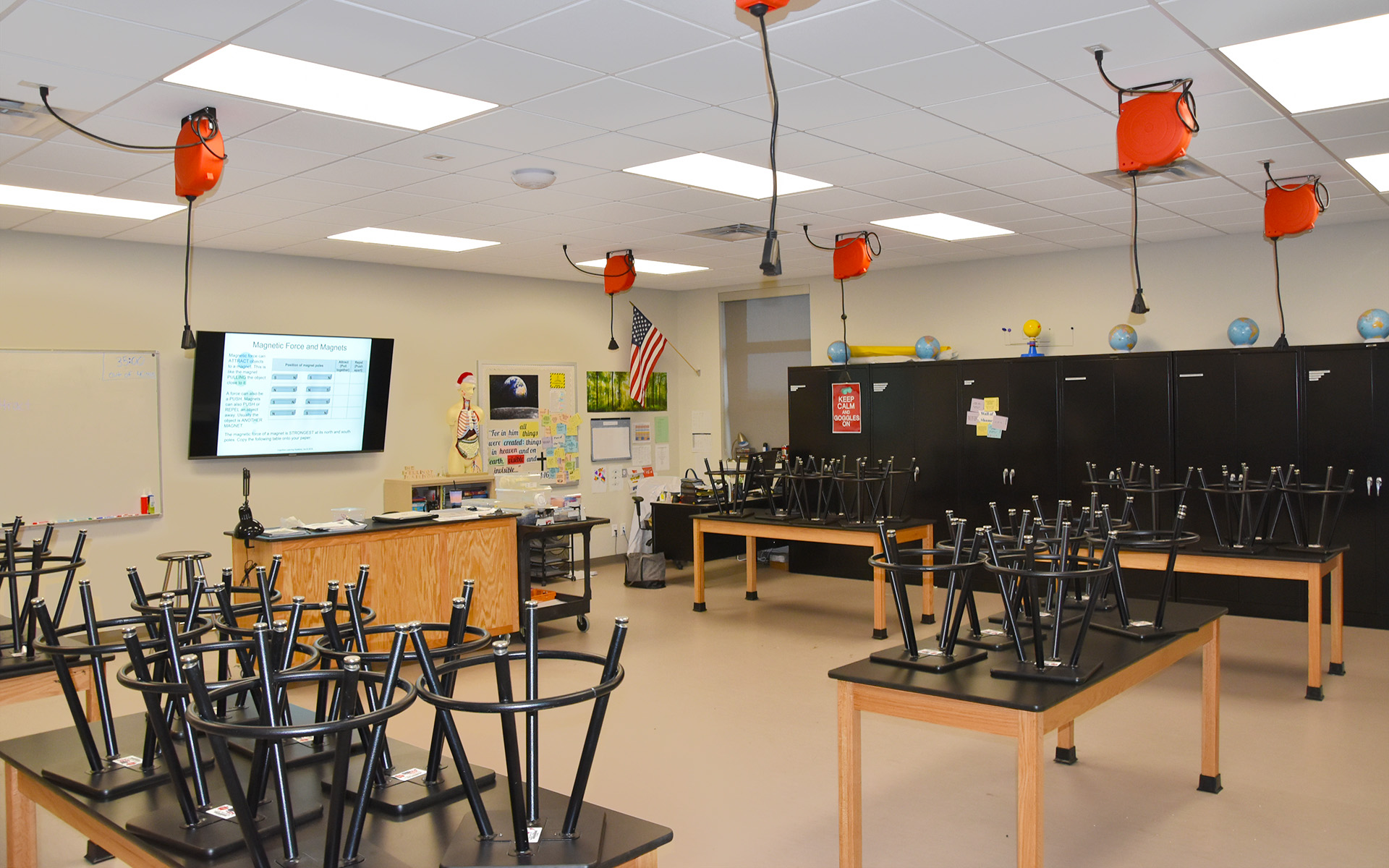
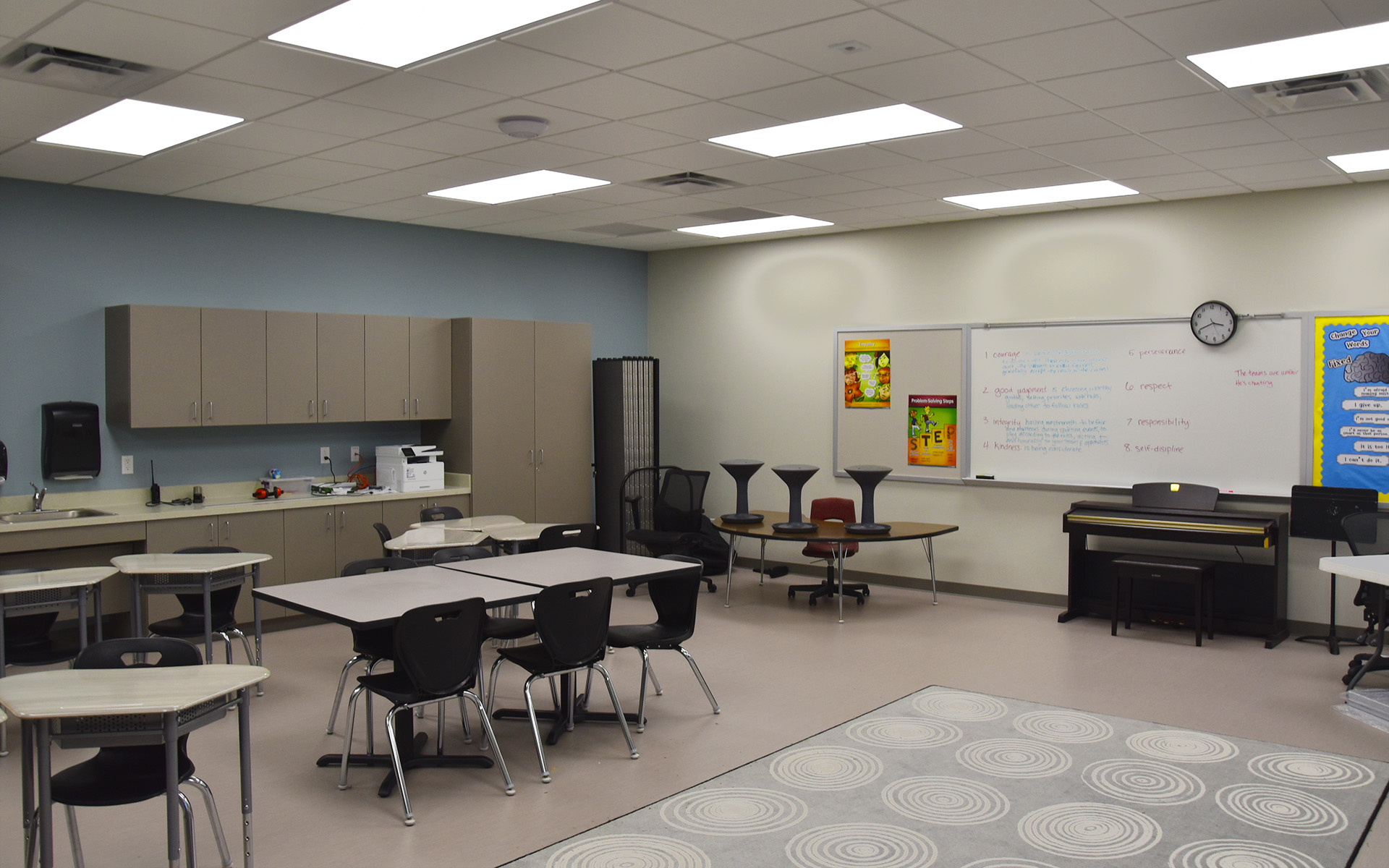
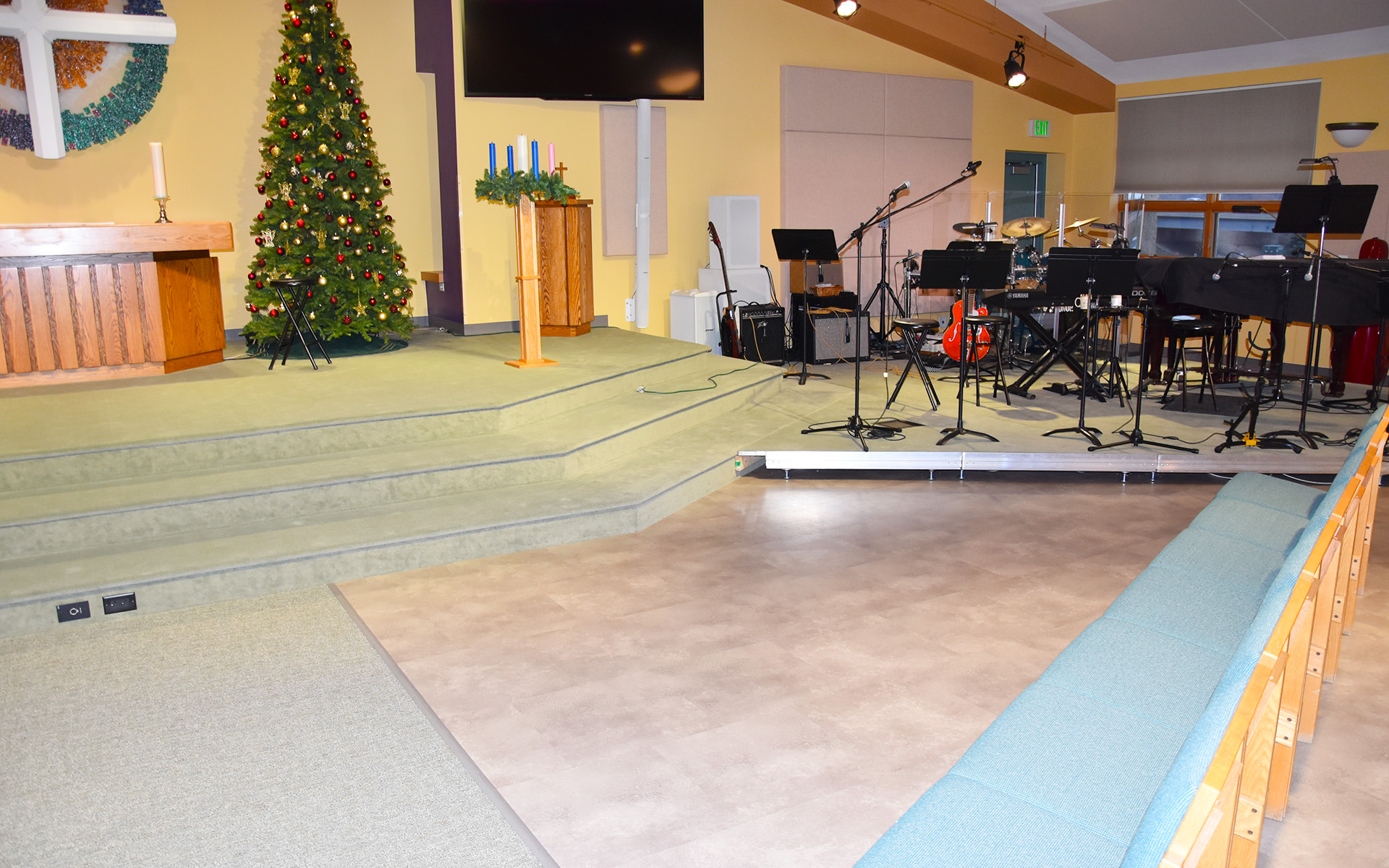
ST. ANDREW LUTHERAN CHURCH - WESTSIDE CHRISTIAN SCHOOL
Addition & Renovation
With recent growth and a strong waiting list, Westside Christian School needed to expand and add onto their existing church and school. Located on the northwest side of Middleton, this single-story addition consists of 6 modernized classrooms, office spaces, restrooms, and utility rooms. With construction starting in March, we were able to fast-track this building to finish up in August, right before the new school year started. With the septic tanks very close to the entrance of the addition, Kraemer Brothers executed the project with precise excavation and careful concrete pours. Matching the exterior and interior color and materials of the previous building, we were able to seamlessly connect the addition to the existing building. Also included in this project were upgrades in the sanctuary in St. Andrew Lutheran Church. These upgrades include new lighting controls and flooring, renovations to the sound system at the AV desk, as well as acoustical sound panels and a raised platform for musical instruments.
RELATED
DoubleTree by Hilton
HOSPITALITY PORTFOLIO
DOUBLETREE BY HILTON
Madison, WI
Overview
ARCHITECT
Gary Brink & Associates, Inc.
Square Footage
152,000
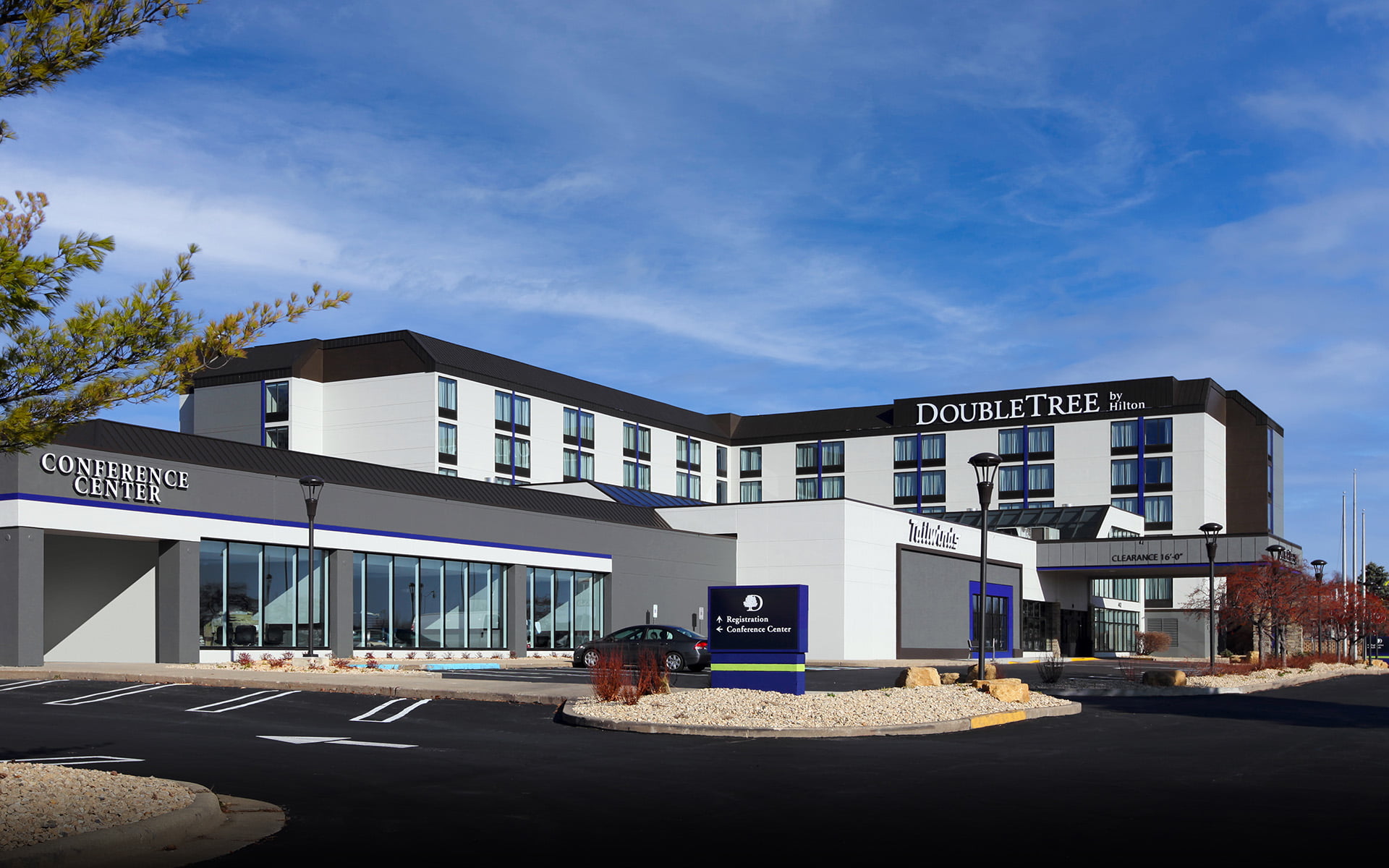
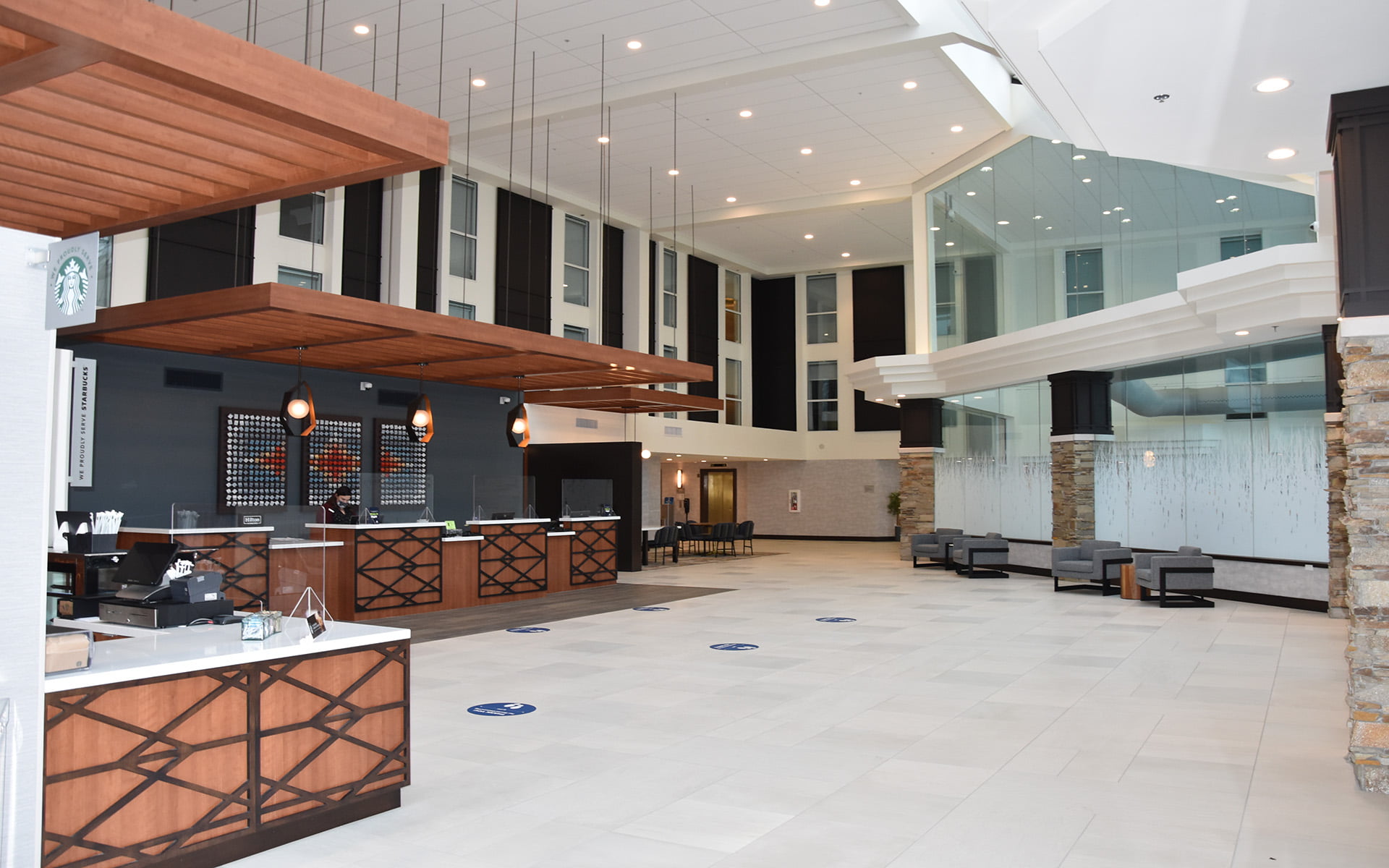
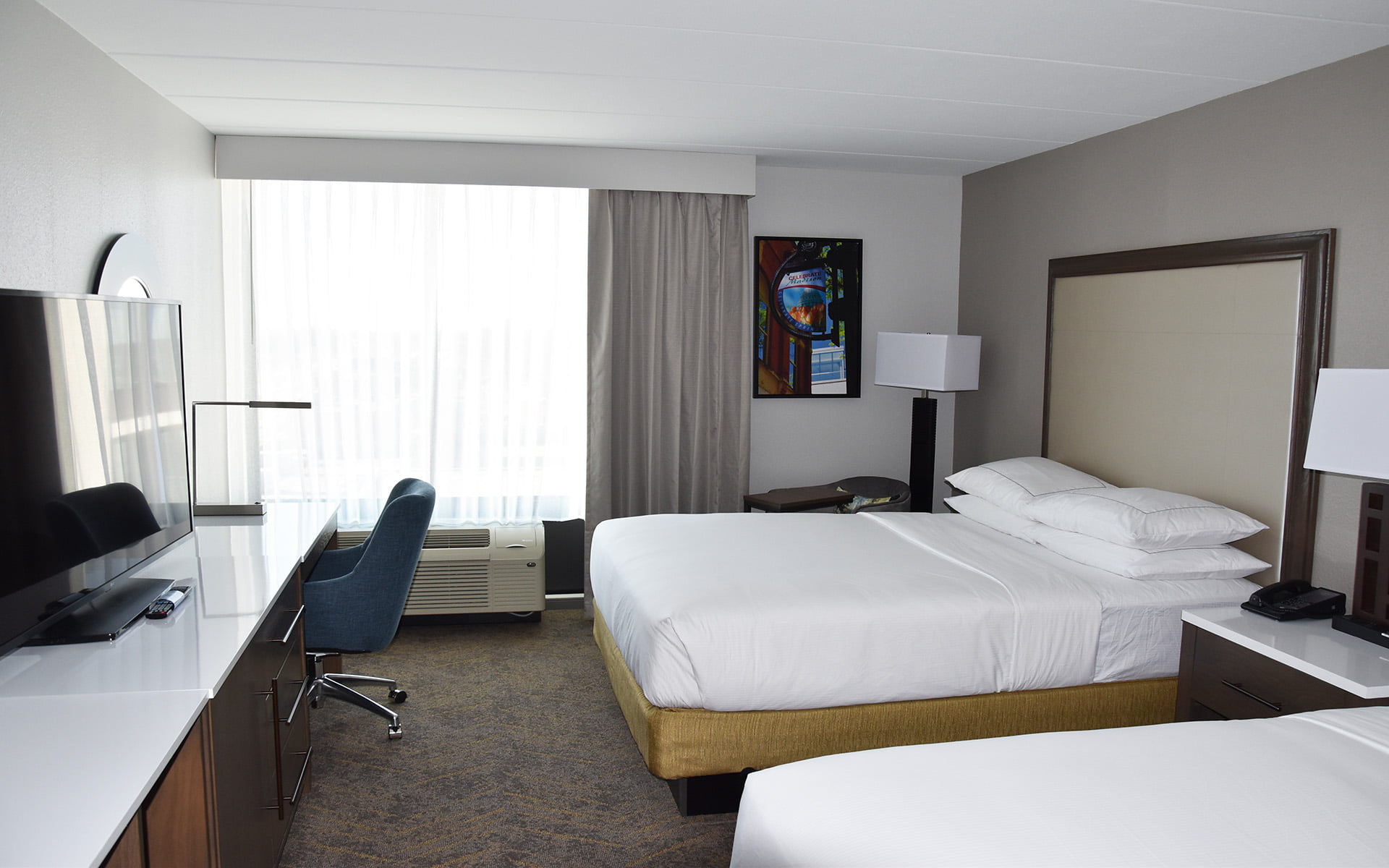
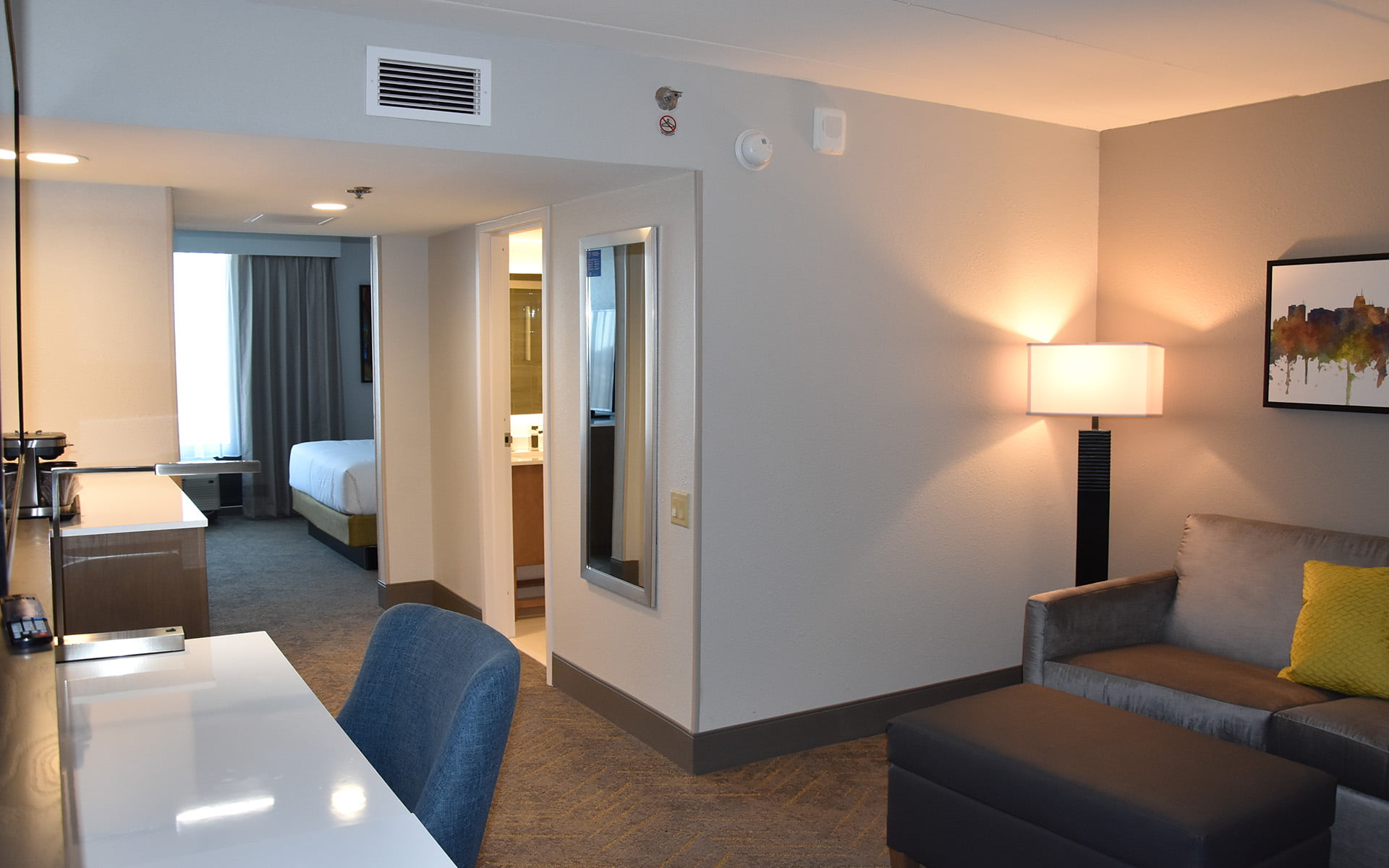
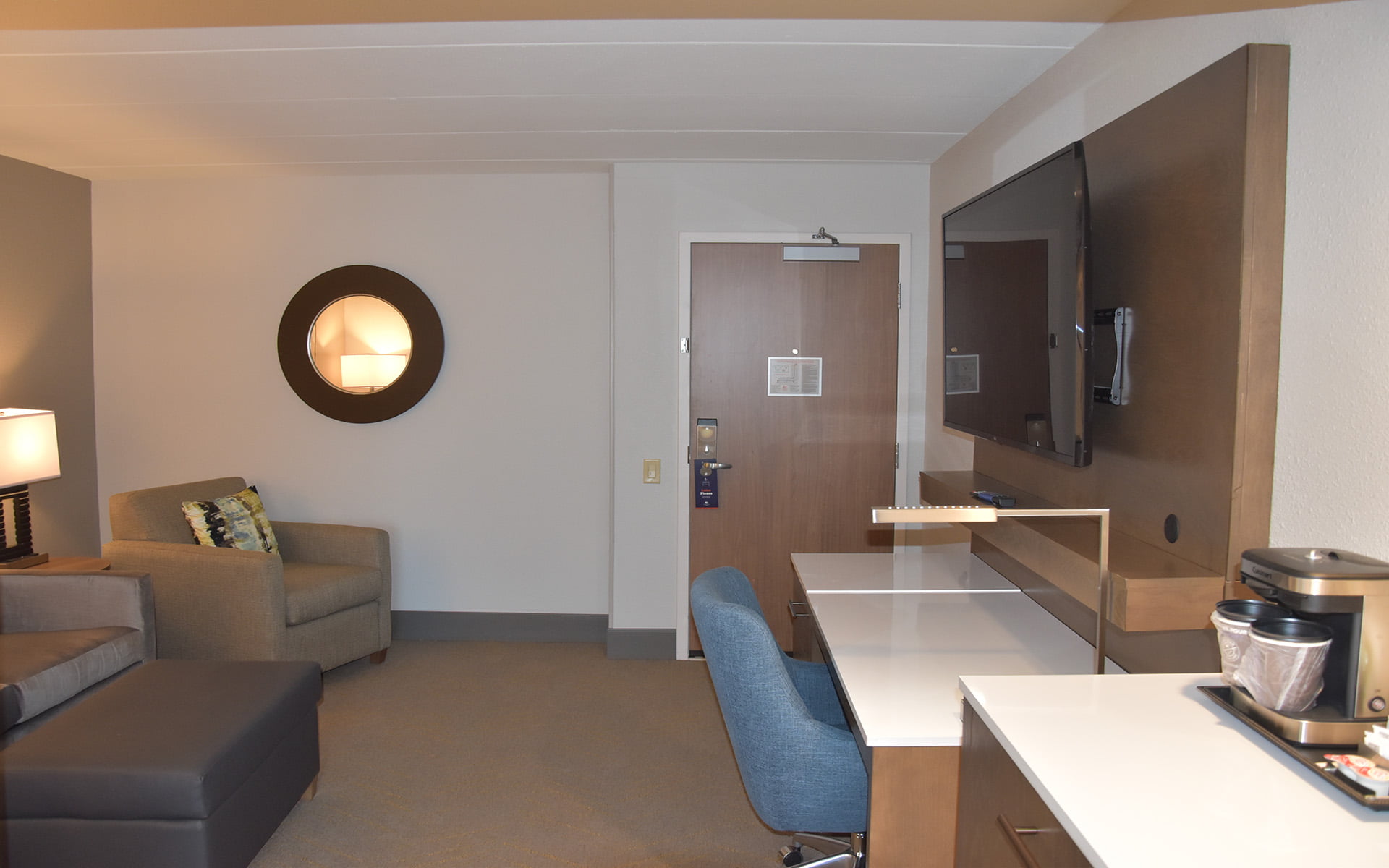
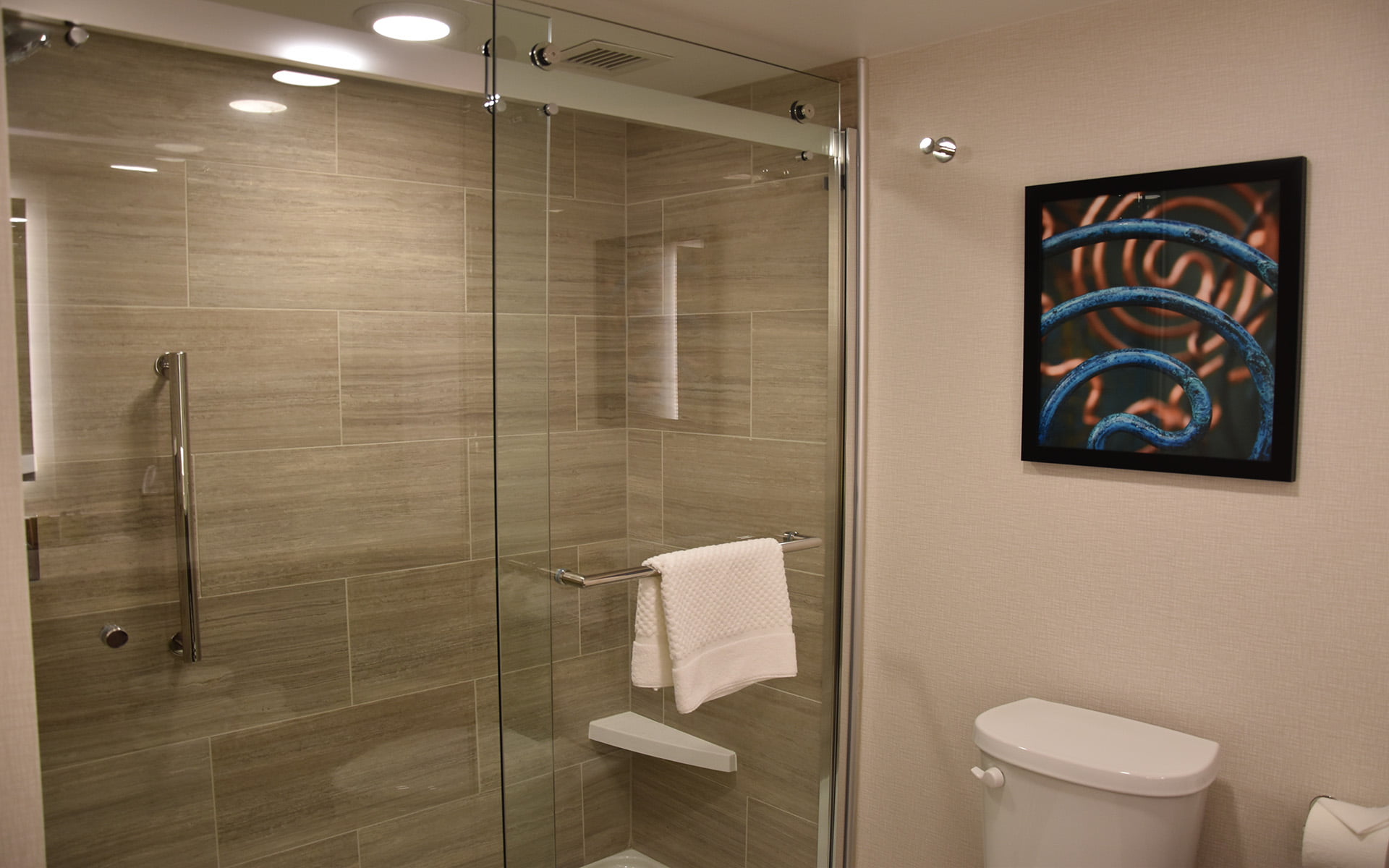
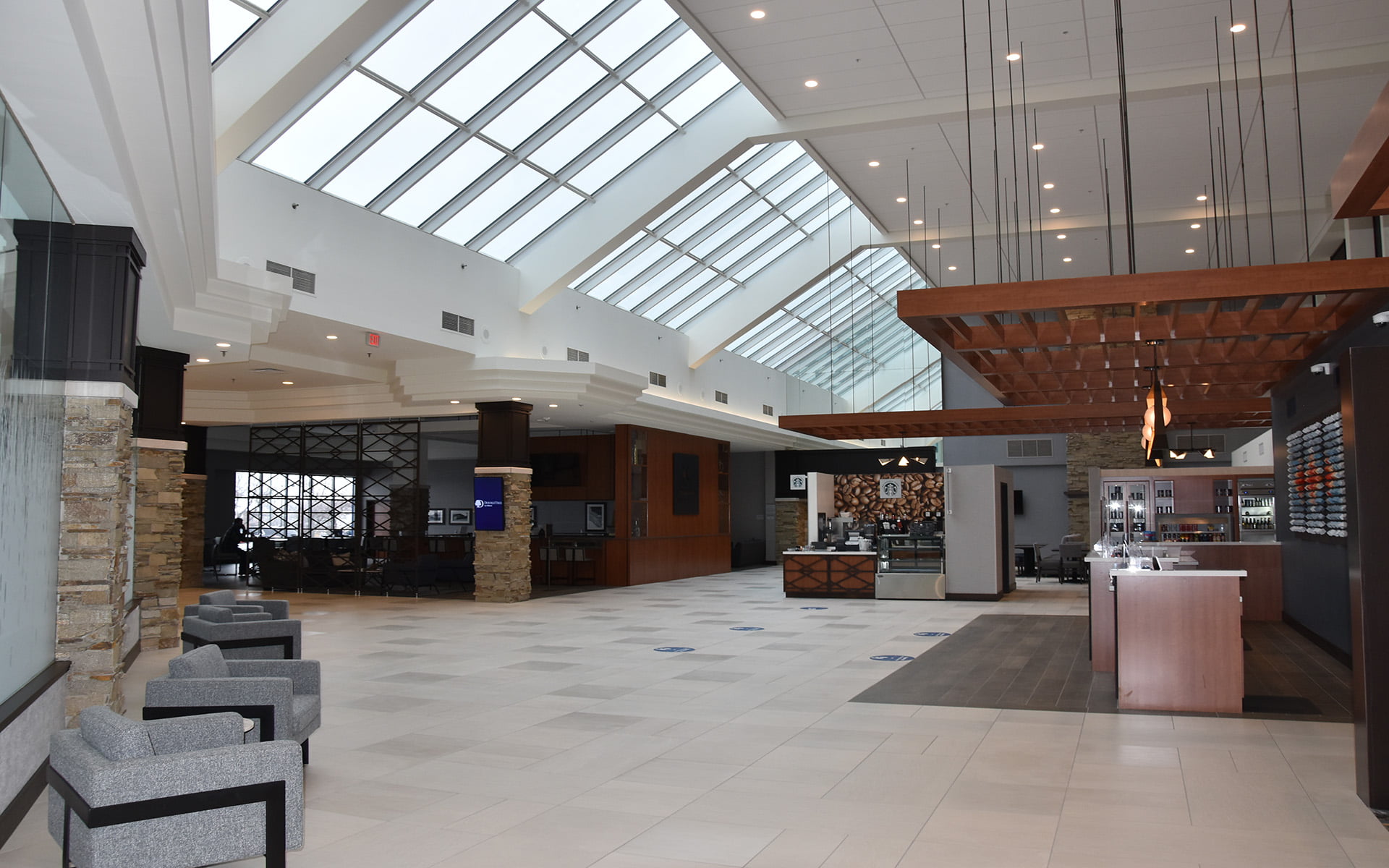
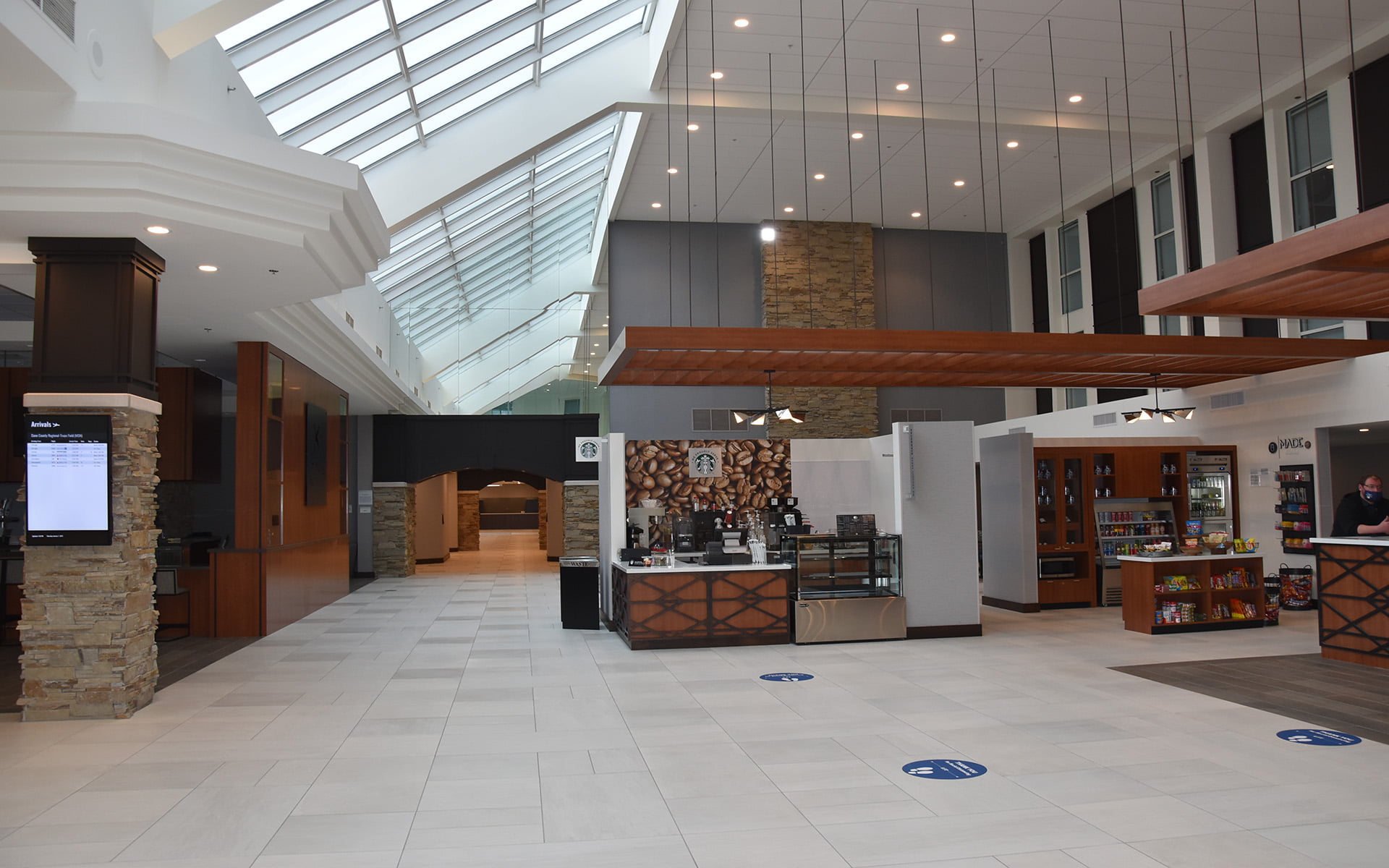
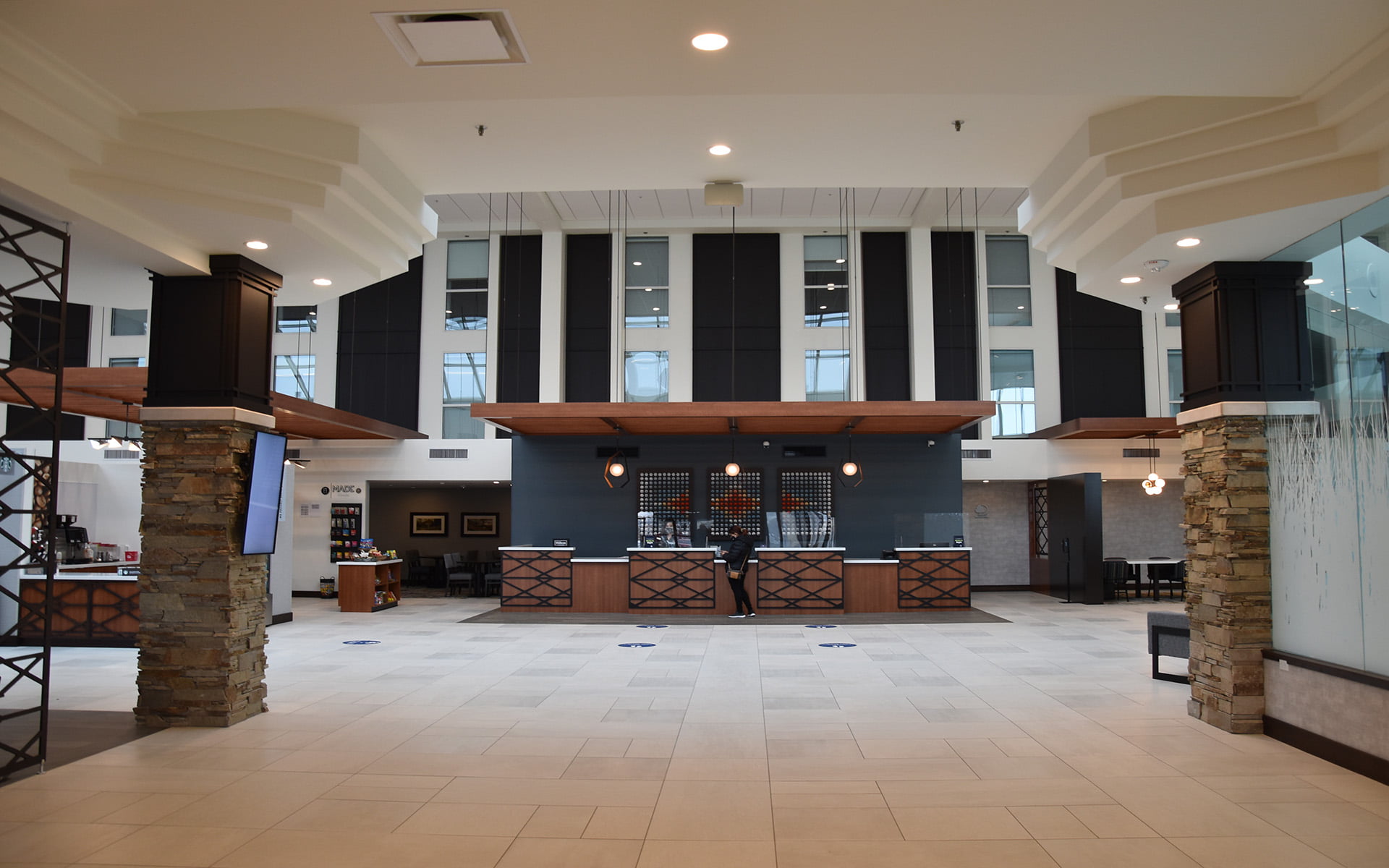
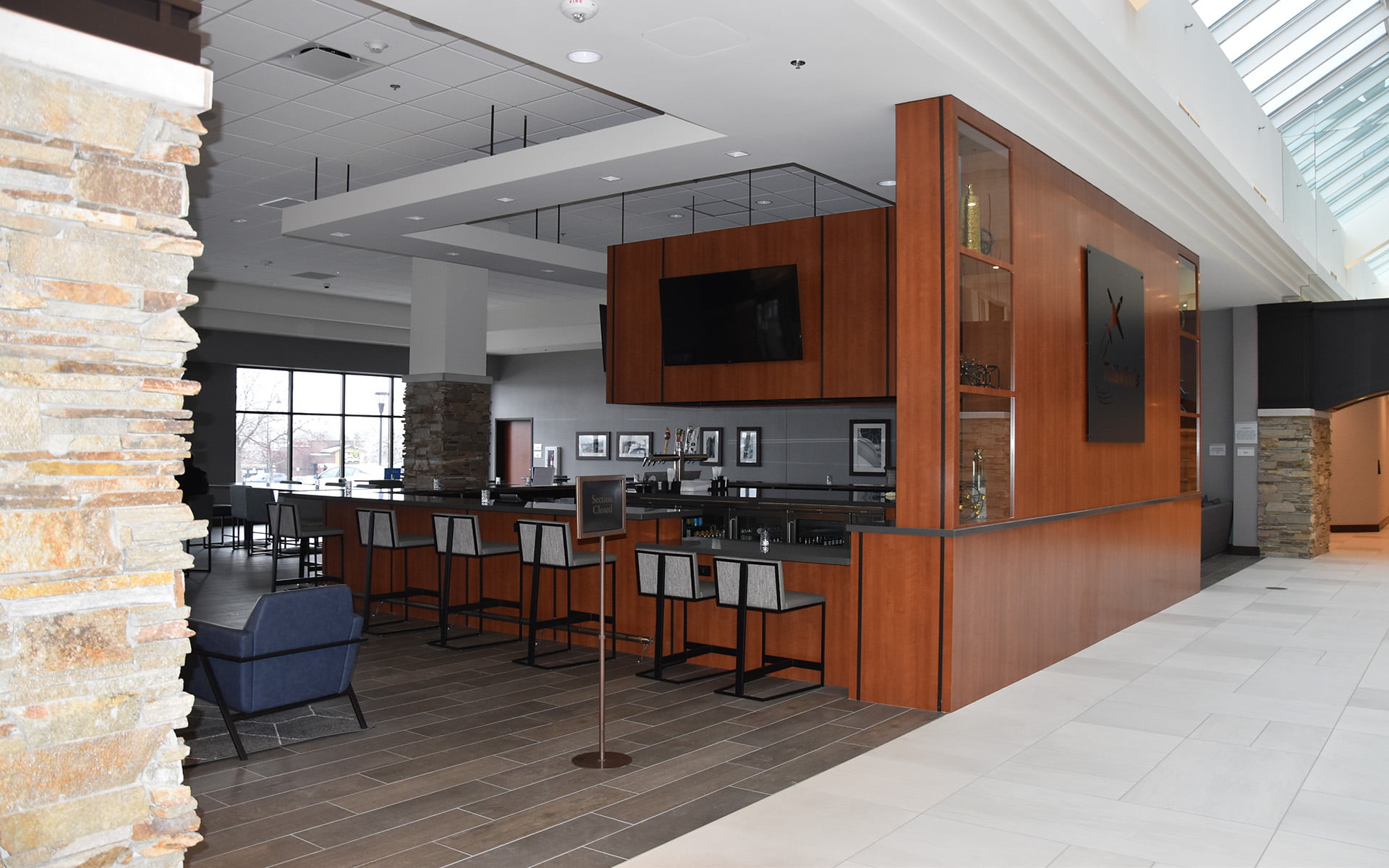
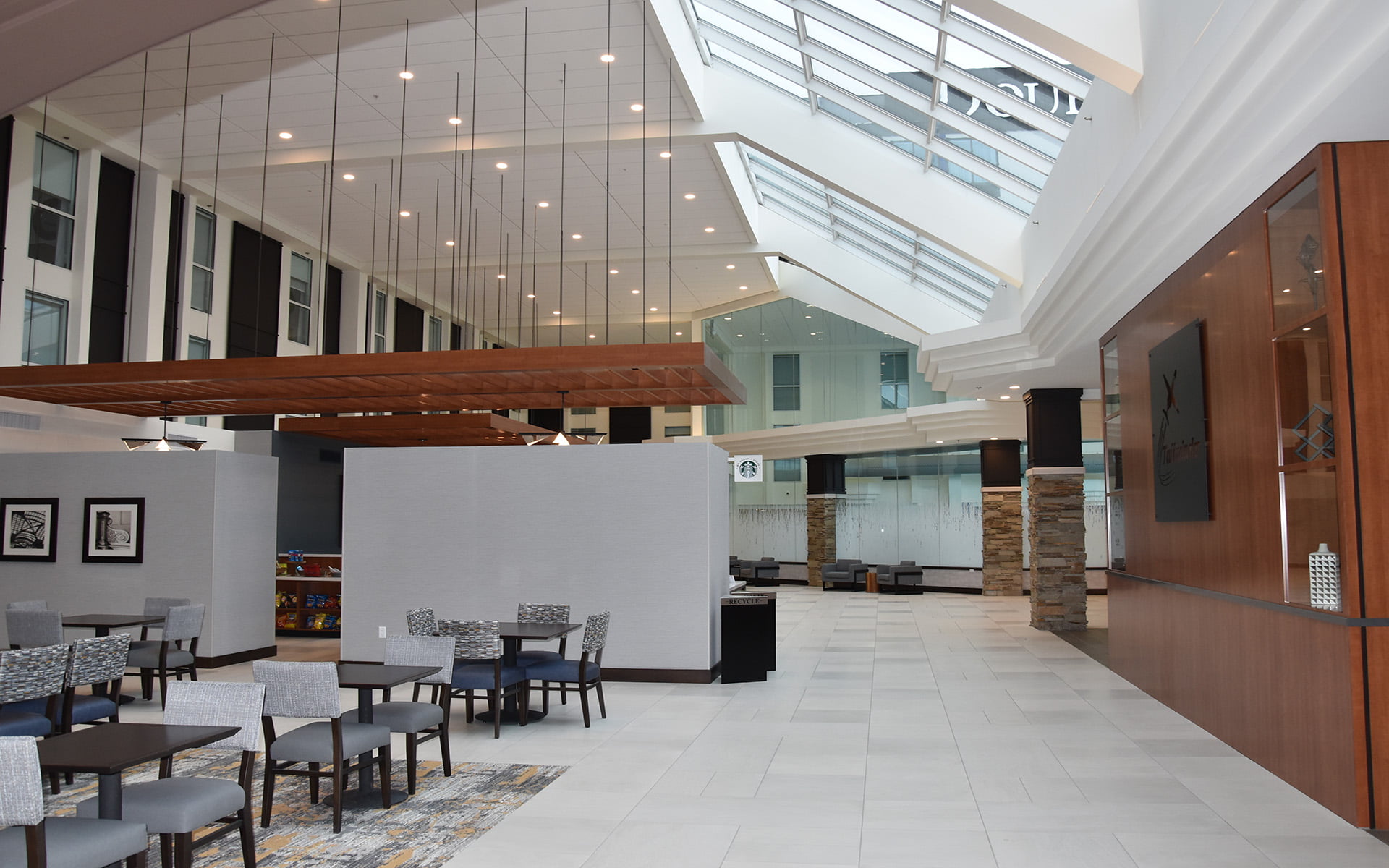
DOUBLETREE BY HILTON
Renovation
After our client acquired this Madison, WI property, which was originally built by Kraemer Brothers, we were asked to provide extensive preconstructive services to balance a much needed renovation within their desired budget. Construction started with an ambitious nine-month schedule in February 2020 and was completed on time. The project, which met both our client’s and Hilton’s standards, involved the redesign and renovation of over 200 guest rooms, the lobby and common area, conference center and a new architectural design for the building’s exterior. With an eye toward performance, several sustainable features were incorporated including new energy efficient windows, upgraded mechanical systems, low-flush toilets and LED lights throughout the interior and exterior of the building. With demolition starting at the same time as the concept drawings, this fast track project was very fluid from start to finish and required a fully integrated project approach to the design and construction activities.
Gundersen Boscobel Area Hospital and Clinics
HEALTHCARE PORTFOLIO
GUNDERSEN BOSCOBEL AREA HOSPITAL AND CLINICS
Boscobel, WI
Overview
ARCHITECT
Kahler Slater; HSR Associates
Square Footage
6,300 Renovation; 11,700 Addition
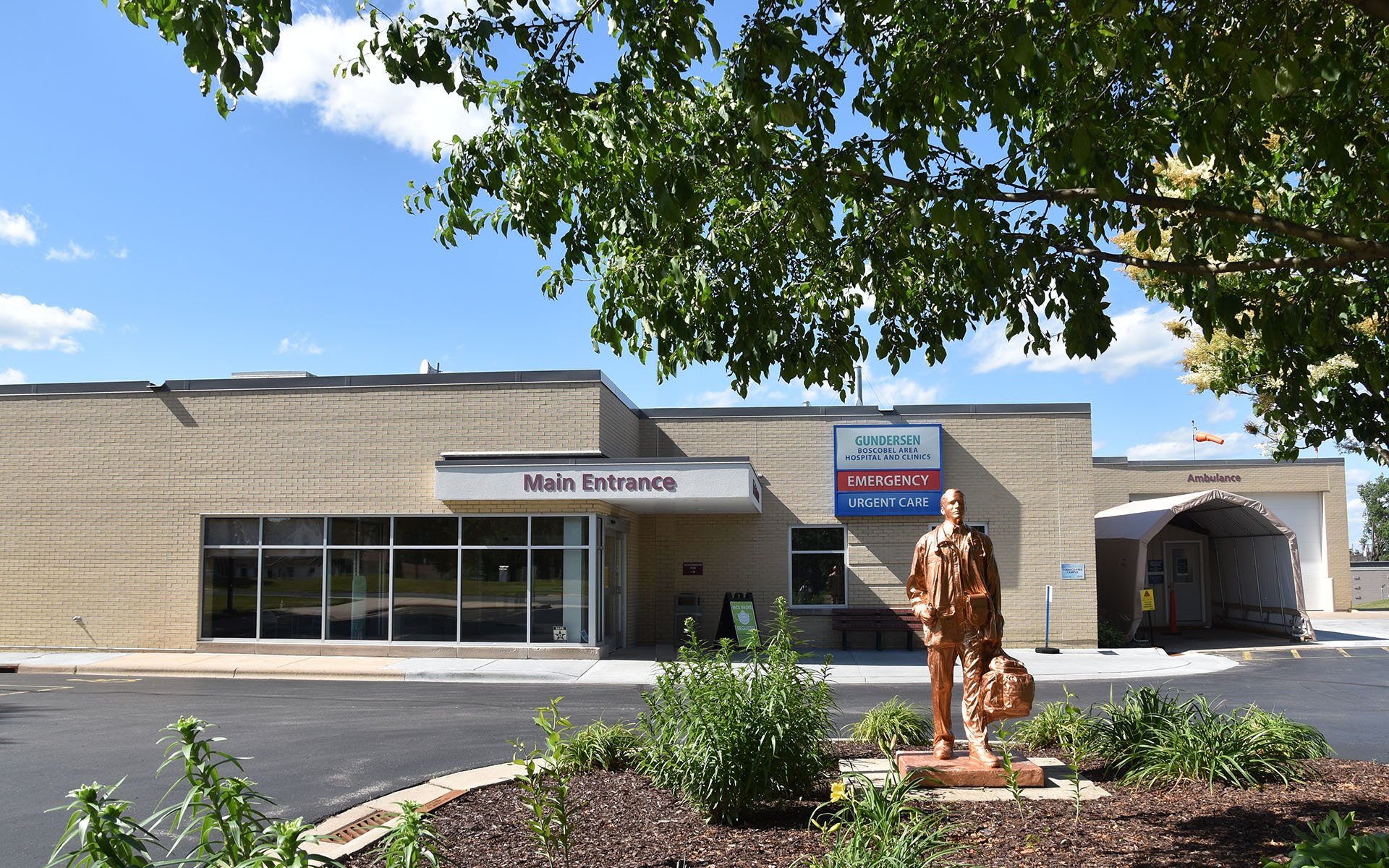
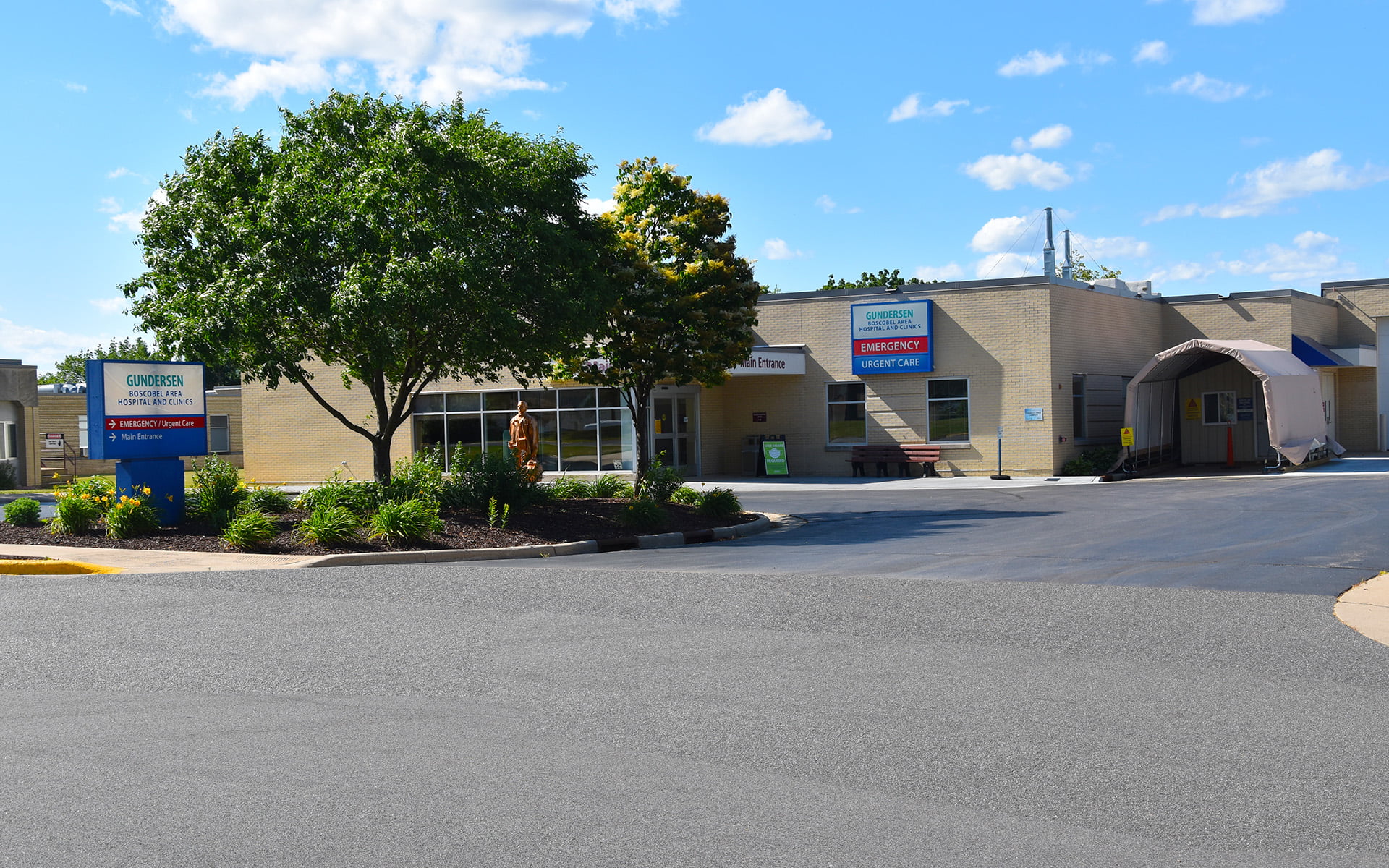
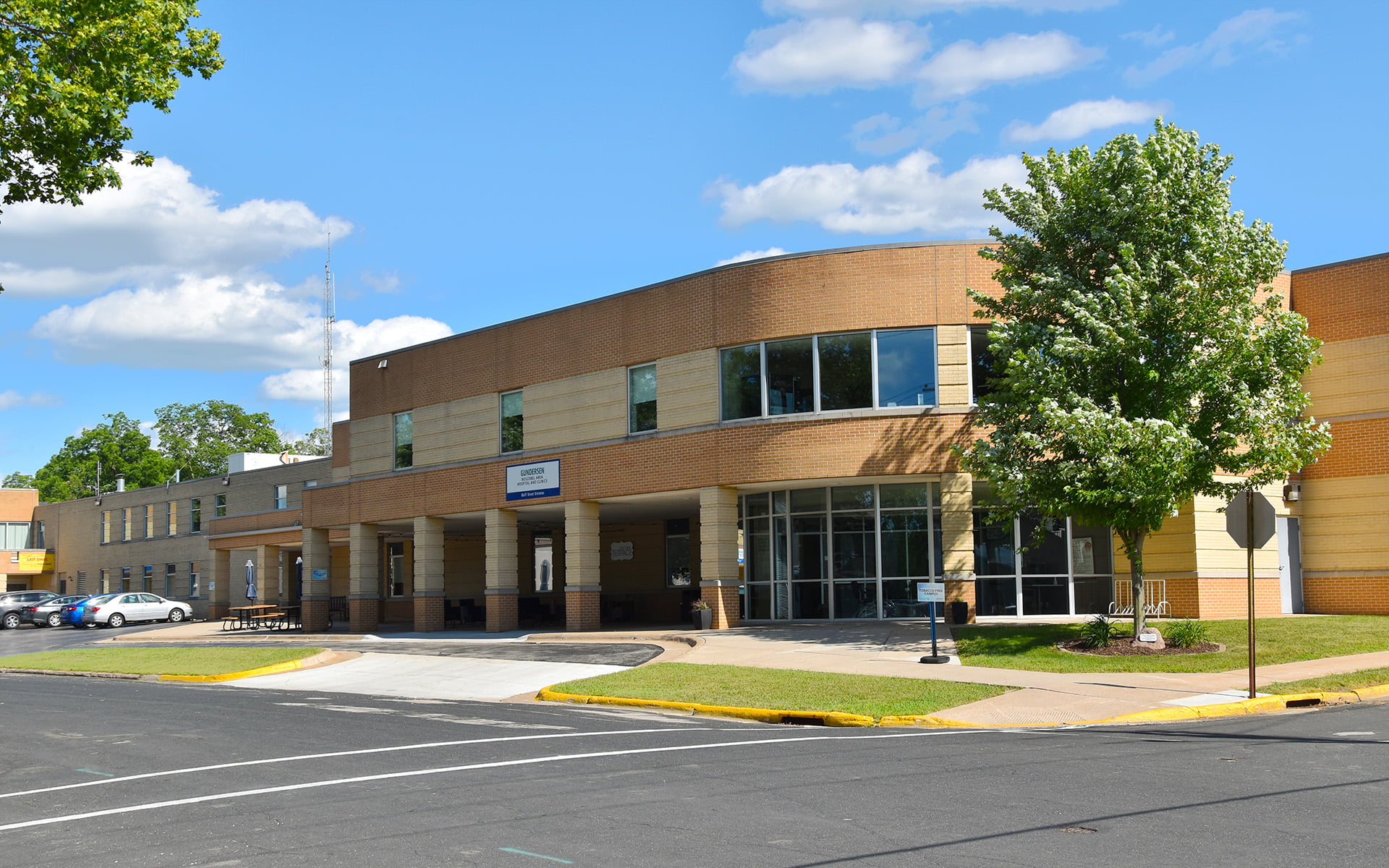
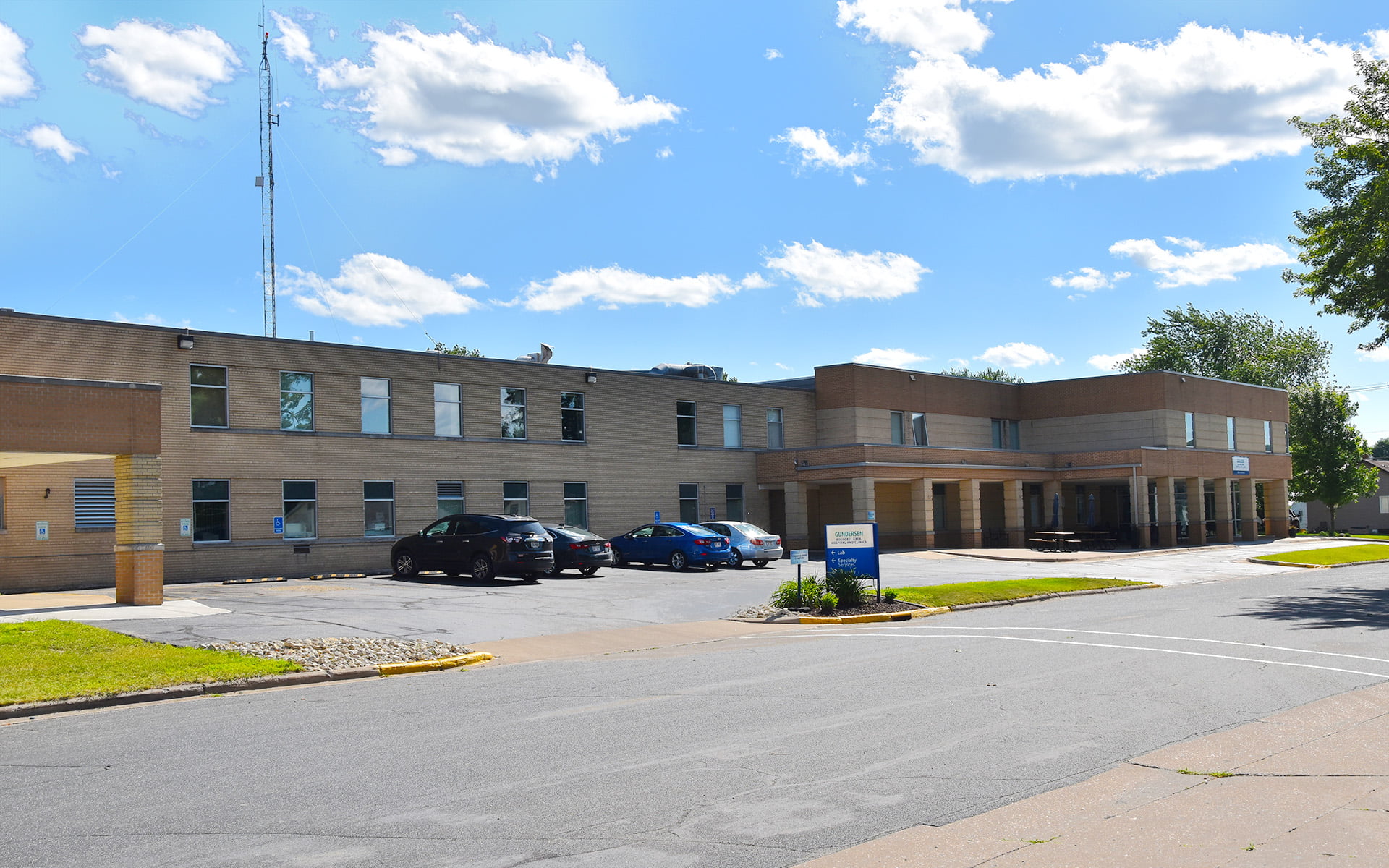
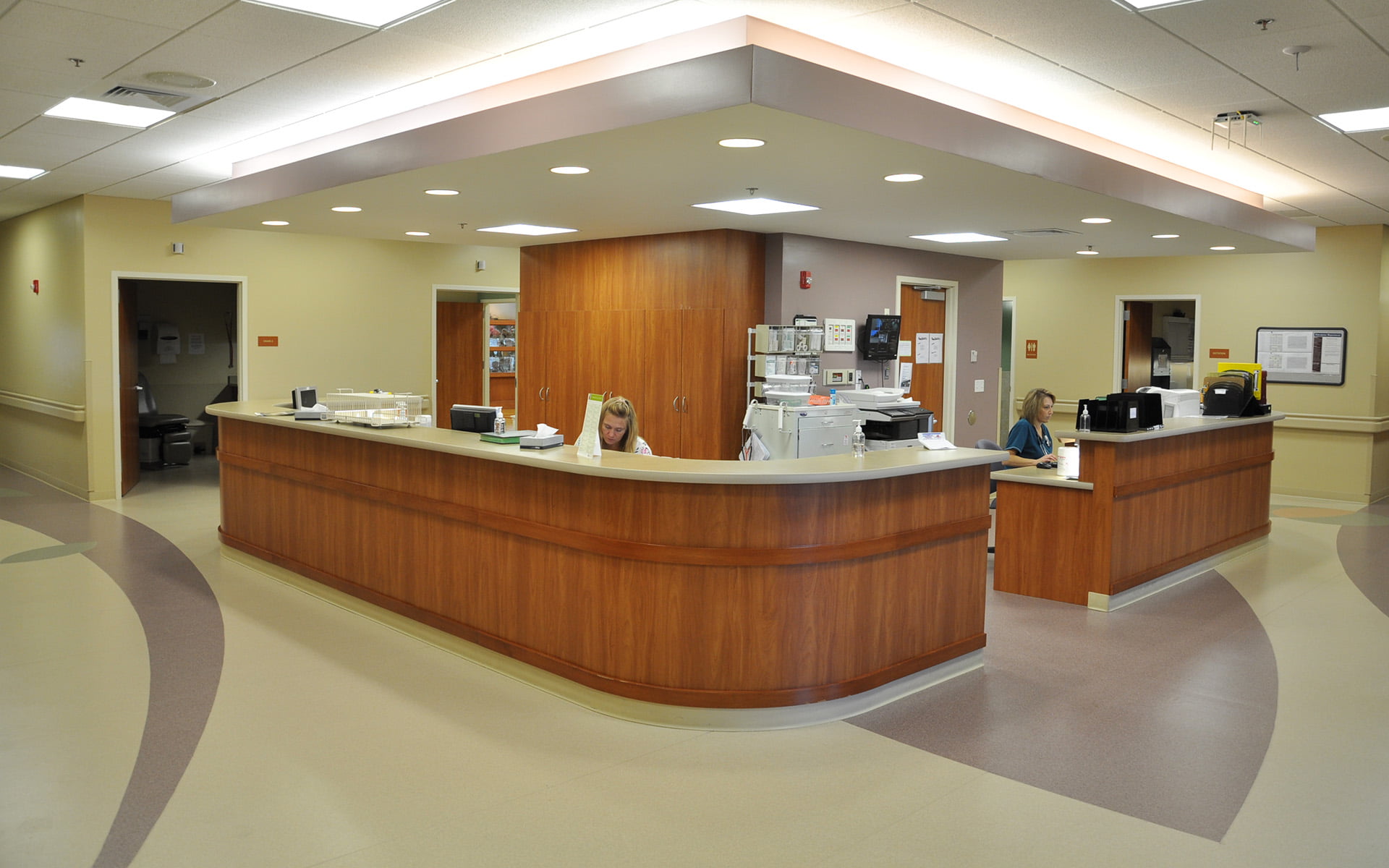
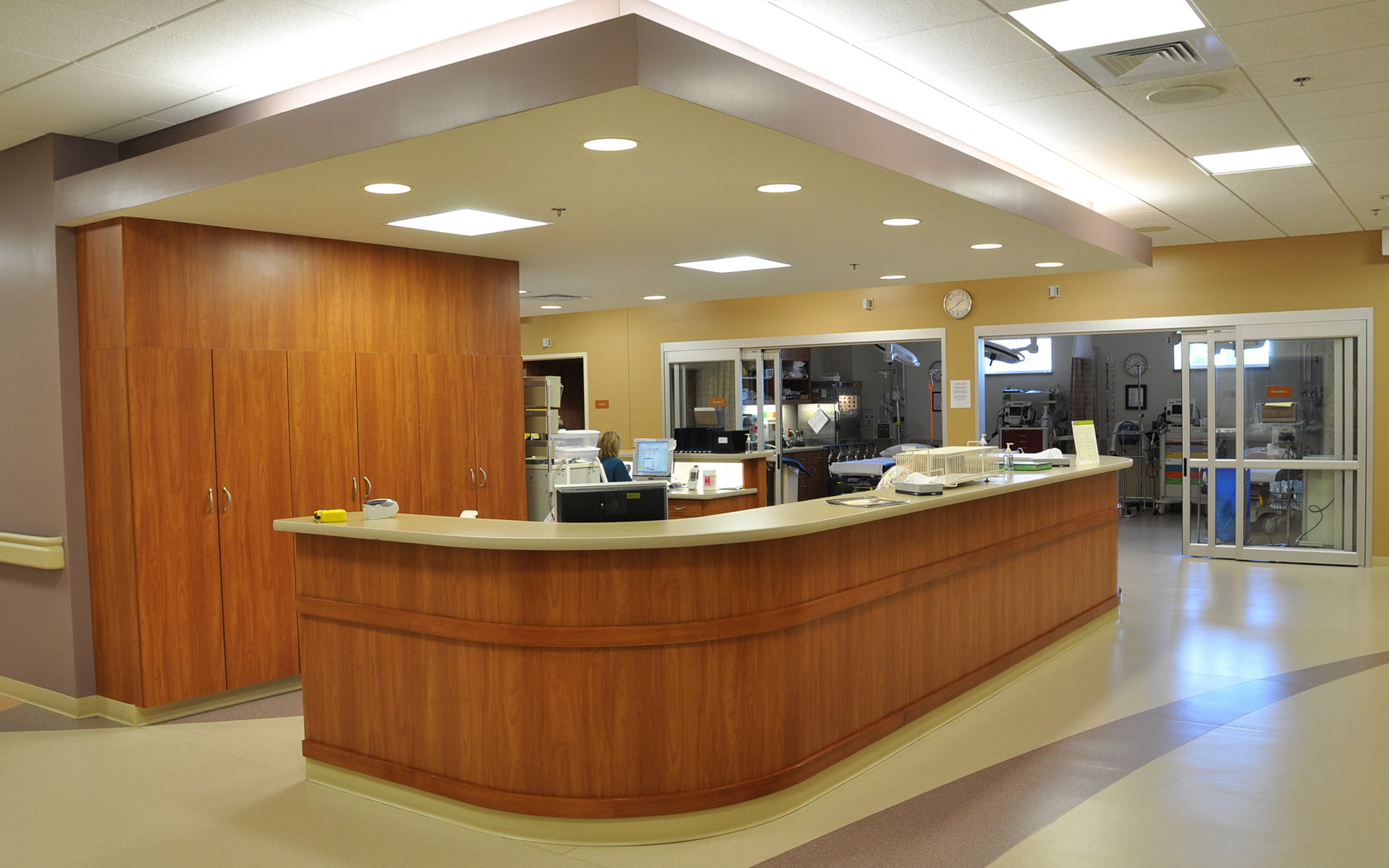
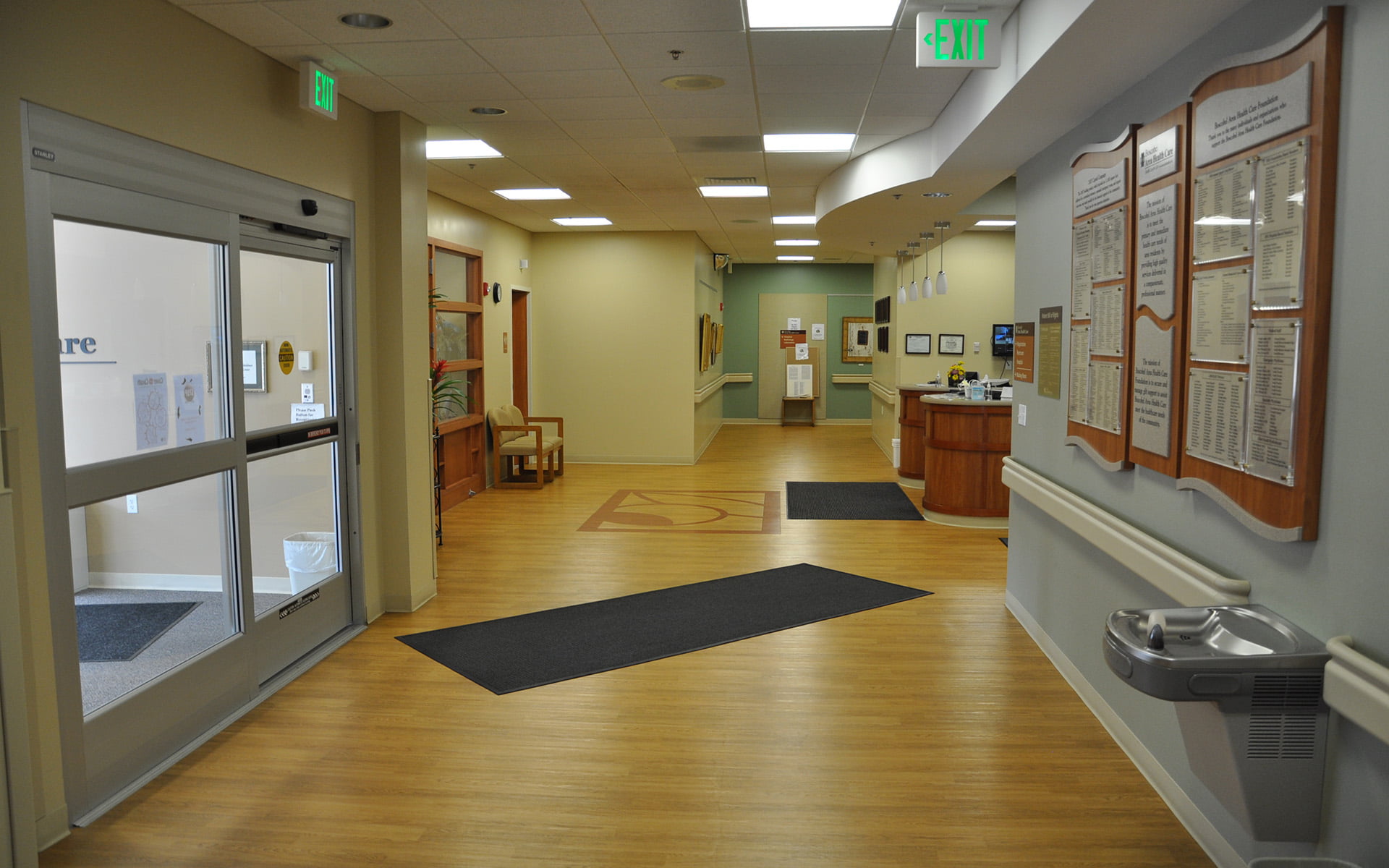
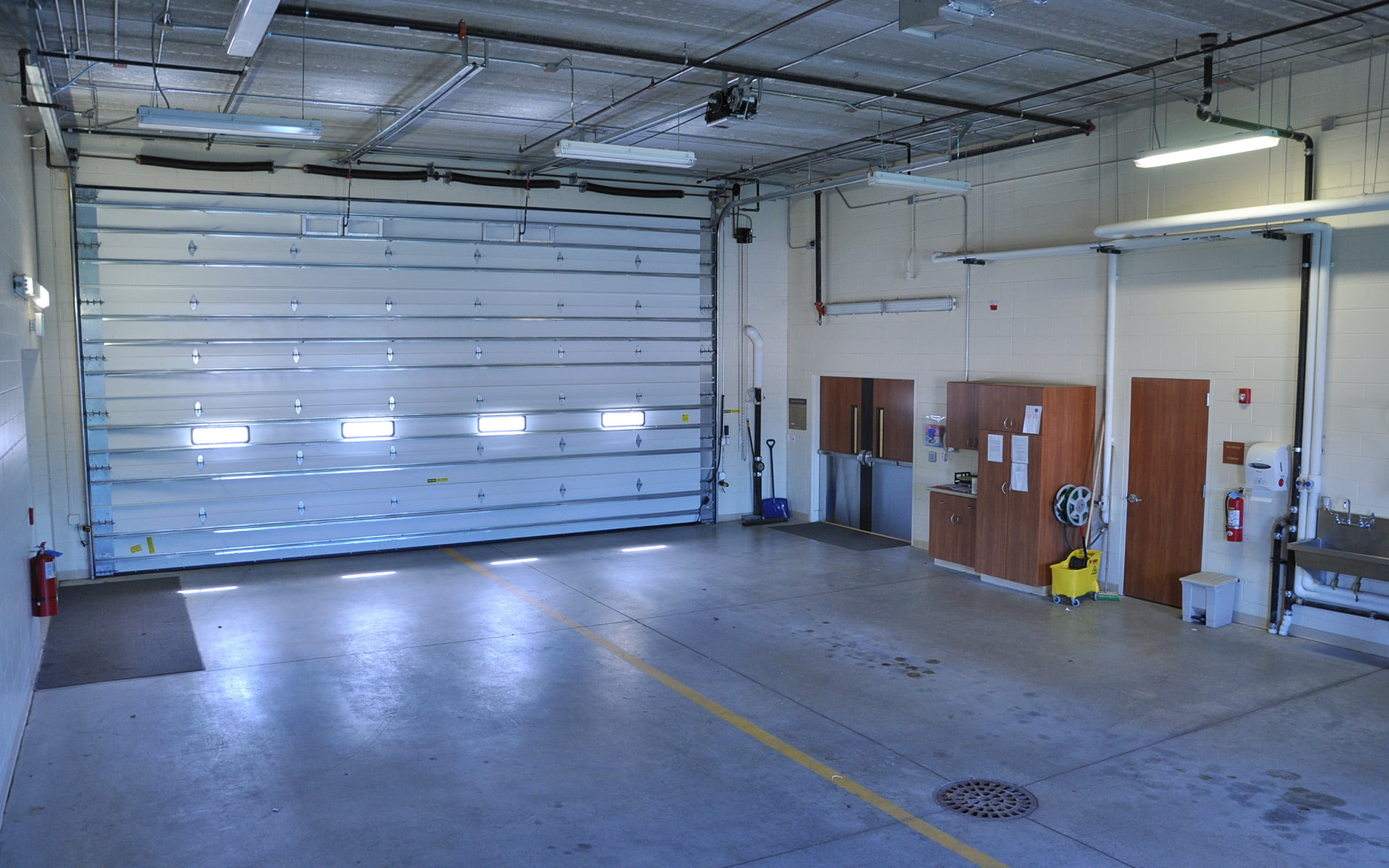
GUNDERSEN BOSCOBEL AREA HOSPITAL AND CLINICS
ER Addition & Renovations
ER ADDITION
The Gundersen Boscobel Area Hospital expanded its facility with a 11,700 square-foot addition allowing for expanded emergency services, including new exam rooms, a special decontamination room, a double ambulance garage, new helicopter pad, centralized entrance and registration area, and a holding cell for patients from Supermax. Another significant enhancement included the renovation of the facility’s mechanical rooms and two new boilers.
RENOVATIONS
Our most recent projects for Gundersen Health System consisted of remodeling the corridors and renovating the nurses’ station, a 5,300 square foot project. Bringing in our experience finish carpenters, we installed new flooring, walls, and ceiling, as well as applying new casework and cabinetry at the nurses’ station, repurposing the area to meet the hospital’s needs. While needing to keep the hospital operational, Kraemer Brothers crews worked closely with the hospital staff to plan the work. Preventing excess construction dust and contamination in the hospital, we added temporary partition walls with negative air pressure, keeping the outside areas clean. Soon after the renovation project finished, Gundersen Health System selected Kraemer Brothers to renovate two existing rooms into one 1,000 square foot infusion service suite with 5 new bays, a cleansing room, and an office. These projects have helped the hospital expand their services and provide an inviting atmosphere to patients.
RELATED
Bruker AXS
SCIENCE & TECHNOLOGY PORTFOLIO
BRUKER AXS
Madison, WI
Overview
ARCHITECT
Strang
Square Footage
46,000
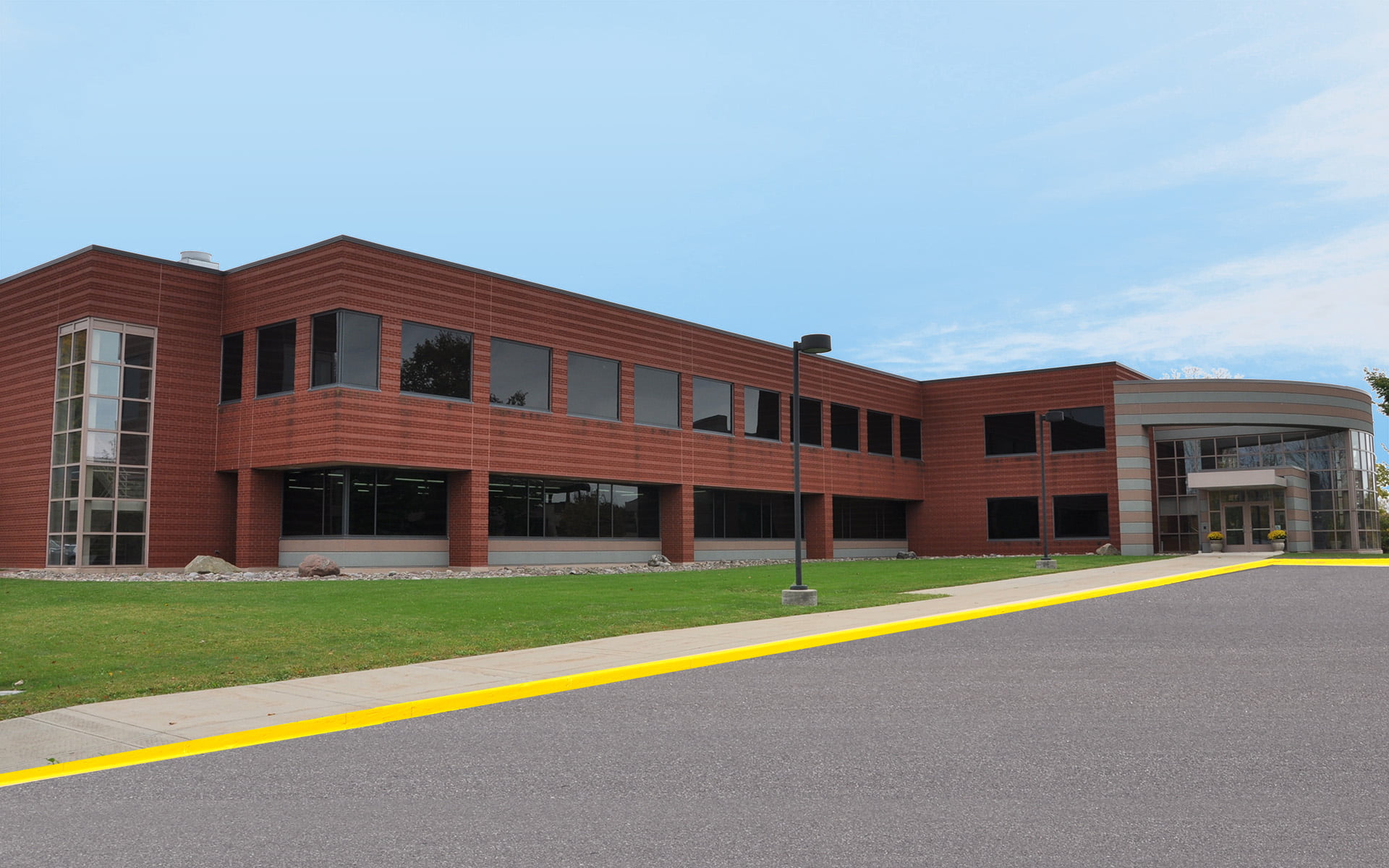
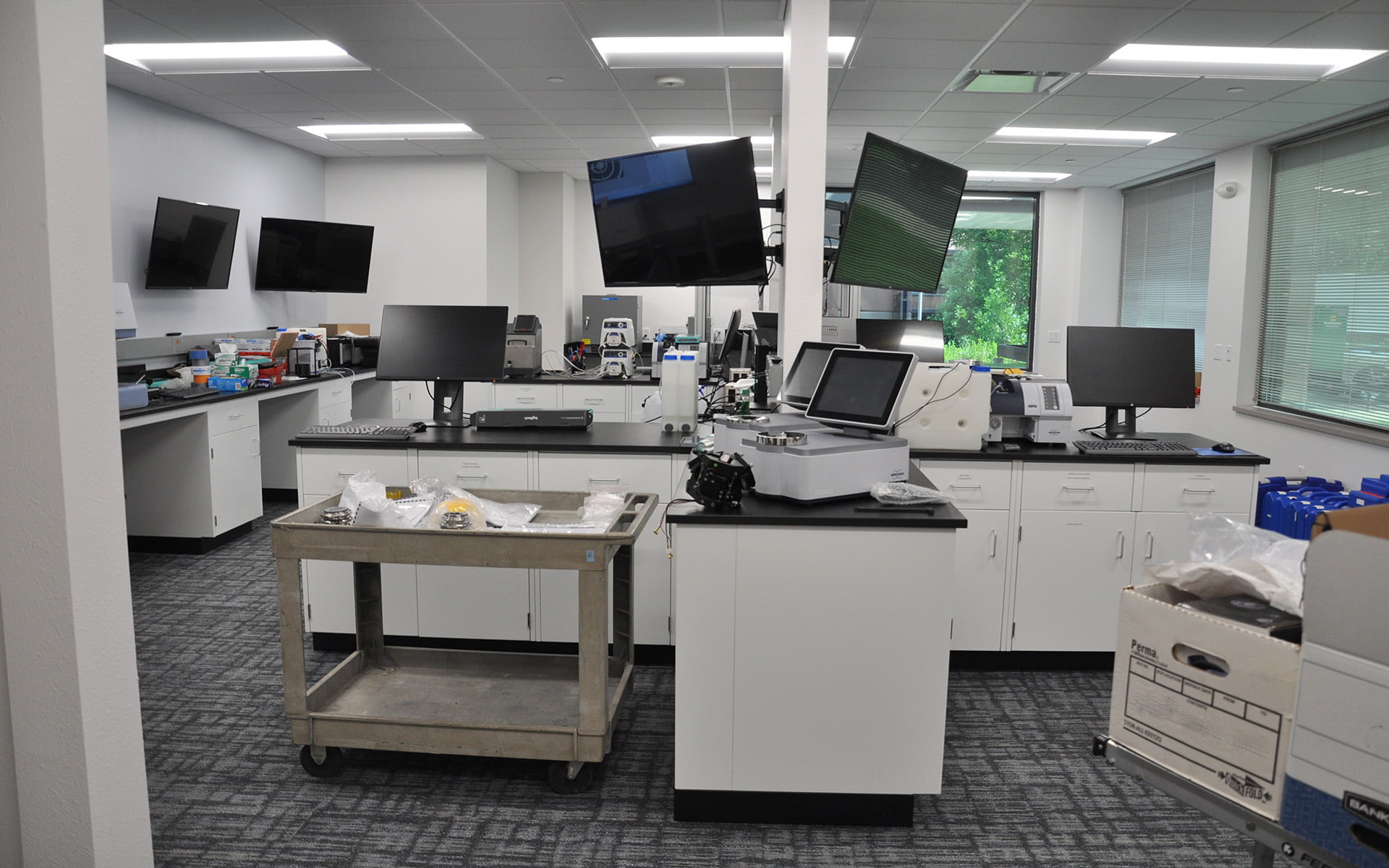
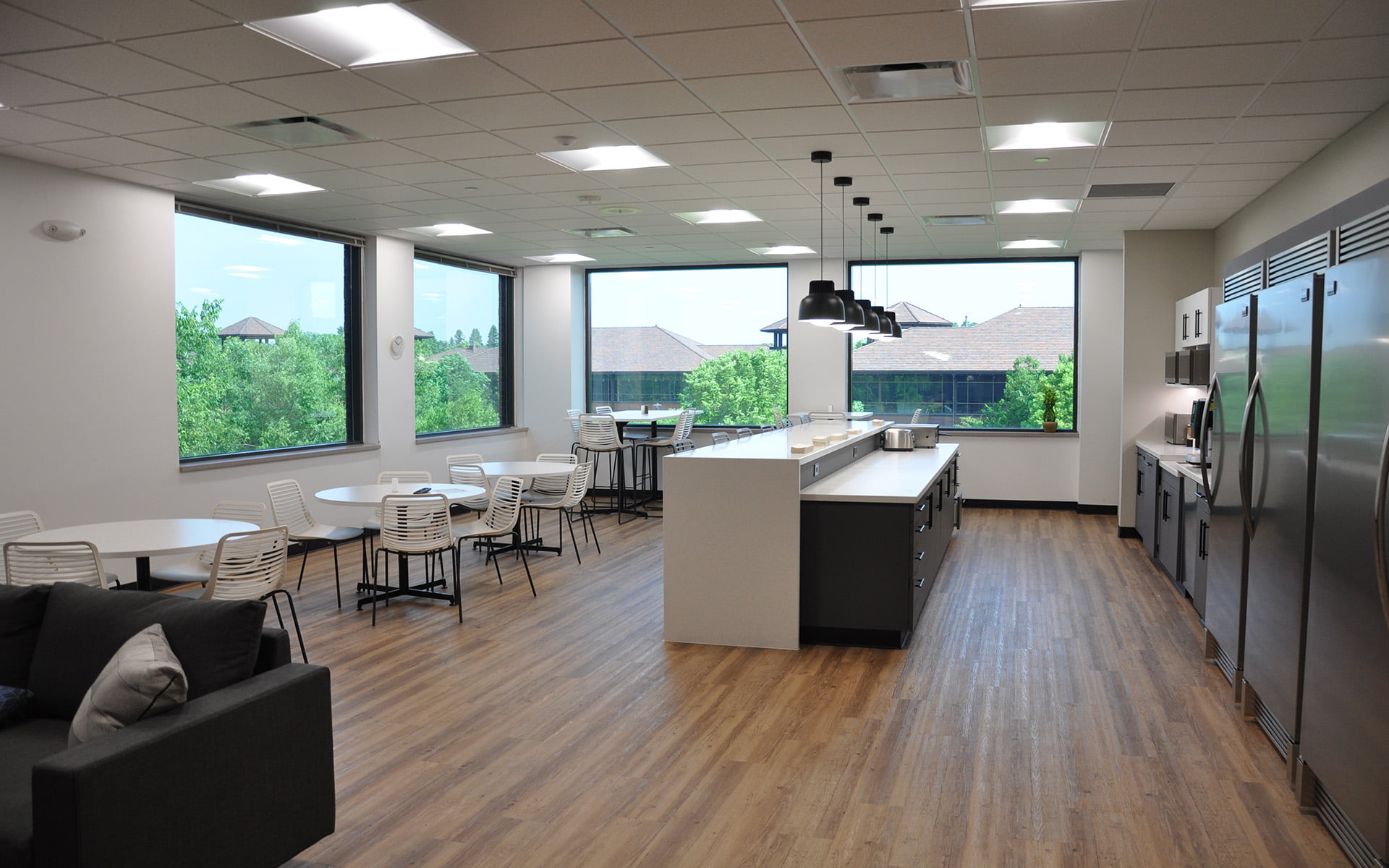
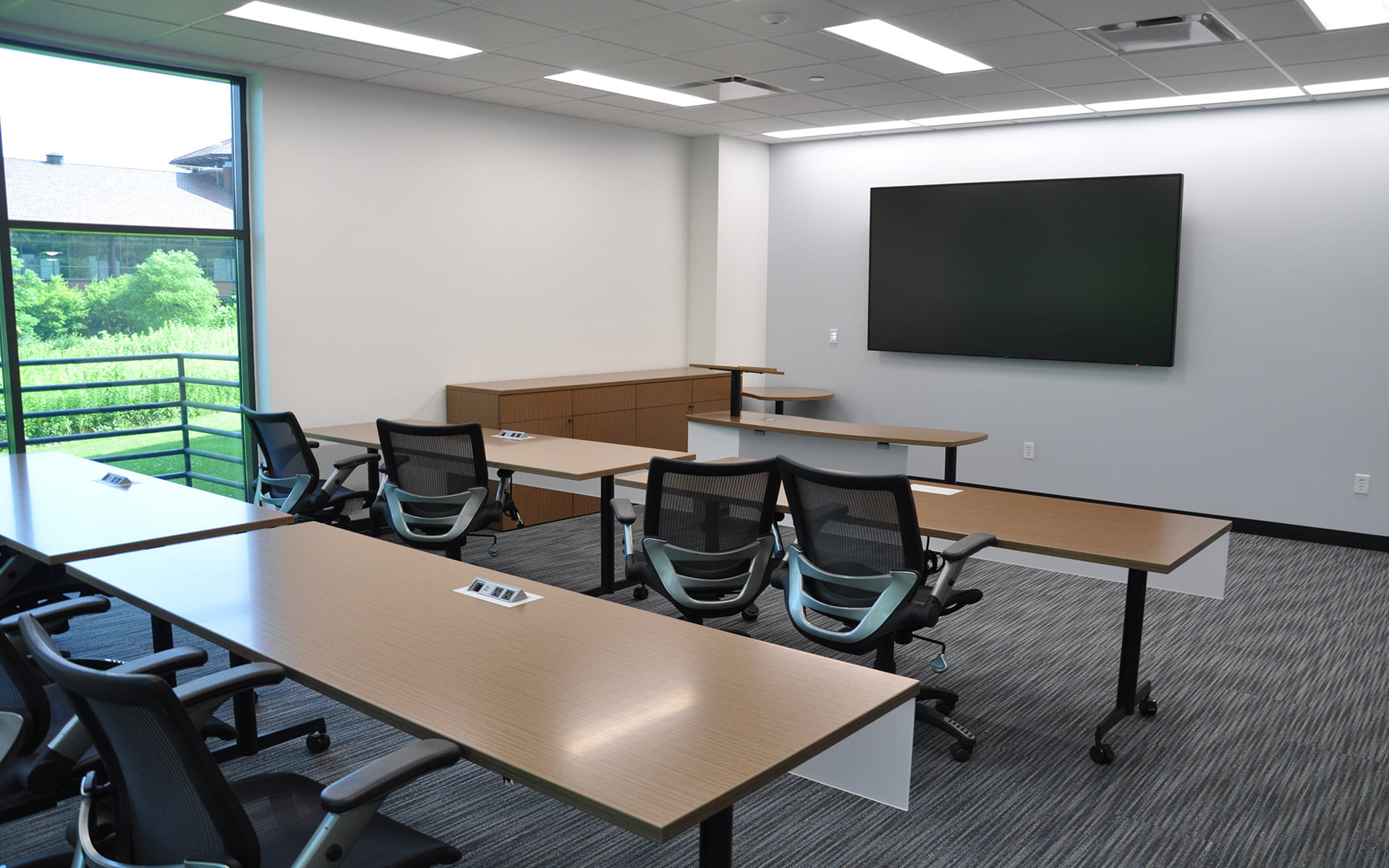
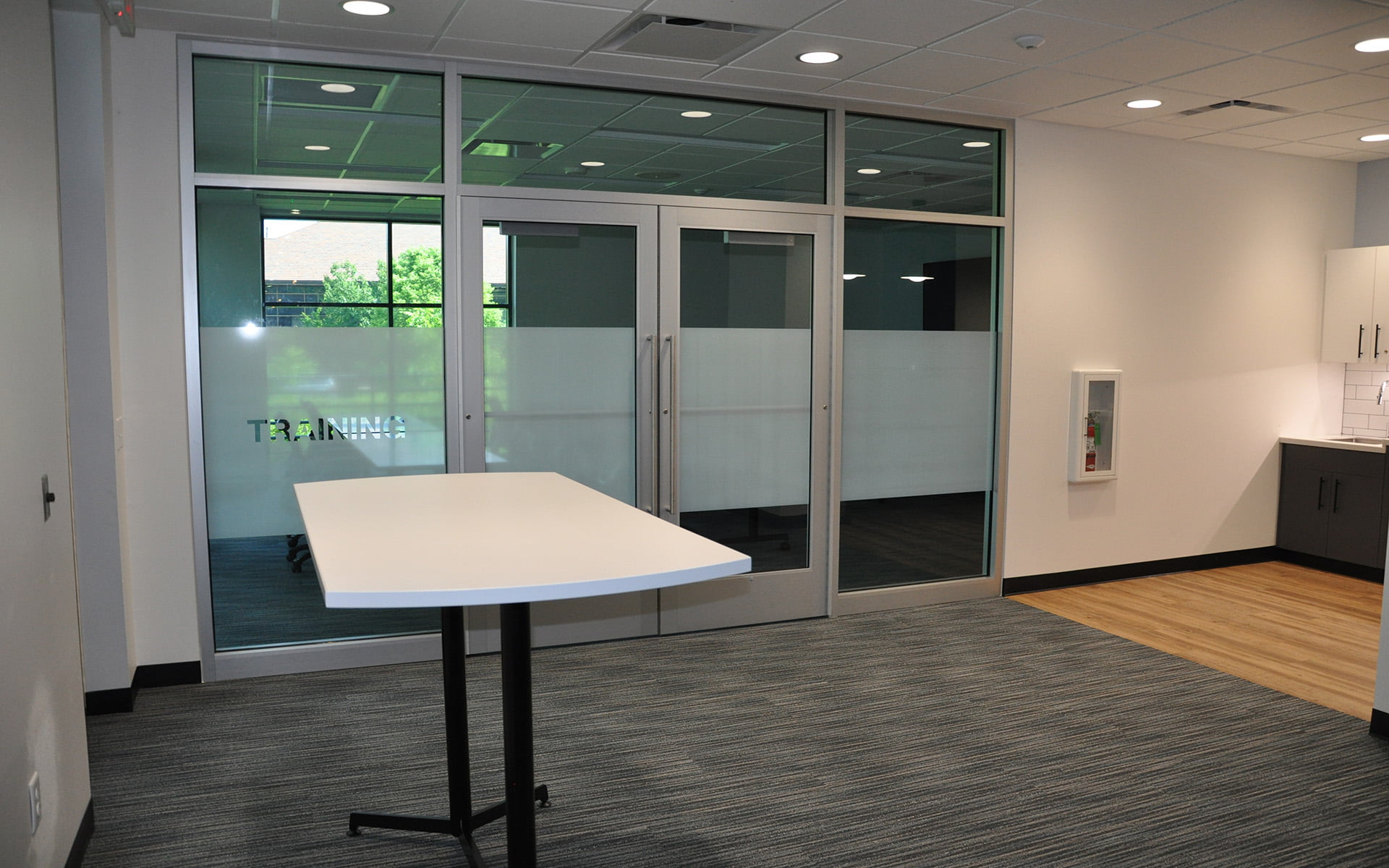
BRUKER AXS
Lab Renovation
When German-owned Bruker AXS, a manufacturer of analytical x-ray systems, wanted to build a new manufacturing plant and office facility in the Promega Research Park in 1999, they selected Kraemer Brothers to provide both the design and construction of their new facility. The 46,000 square foot facility has 18,000 square feet of a high-bay manufacturing area, which is outfitted with a white reflective floor surface, requiring very precise finishing on the part of Kraemer Brothers’ cement finishers. The balance of the space consists of offices and research labs for the growing company. The building layout was developed to reflect optimal workflow patterns to create a pleasant work environment throughout both the office and manufacturing spaces. Bruker AXS selected us again for their interior renovations in 2019, which consisted of converting 11,000 square feet into new lab space, allowing Bruker AXS to consolidate the operations of multiple divisions of the company into one building. Bruker AXS was able to remain fully operational during our renovation activities that required creating laser safe labs for the company’s operations.
RELATED
Promega Corporation – Rosalind Franklin Center
SCIENCE & TECHNOLOGY PORTFOLIO
PROMEGA CORPORATION
Rosalind Franklin Center
Madison, WI
Overview
ARCHITECT
Ramlow/Stein Architecture + Interiors
Square Footage
17,200 Renovation
10,000 Addition
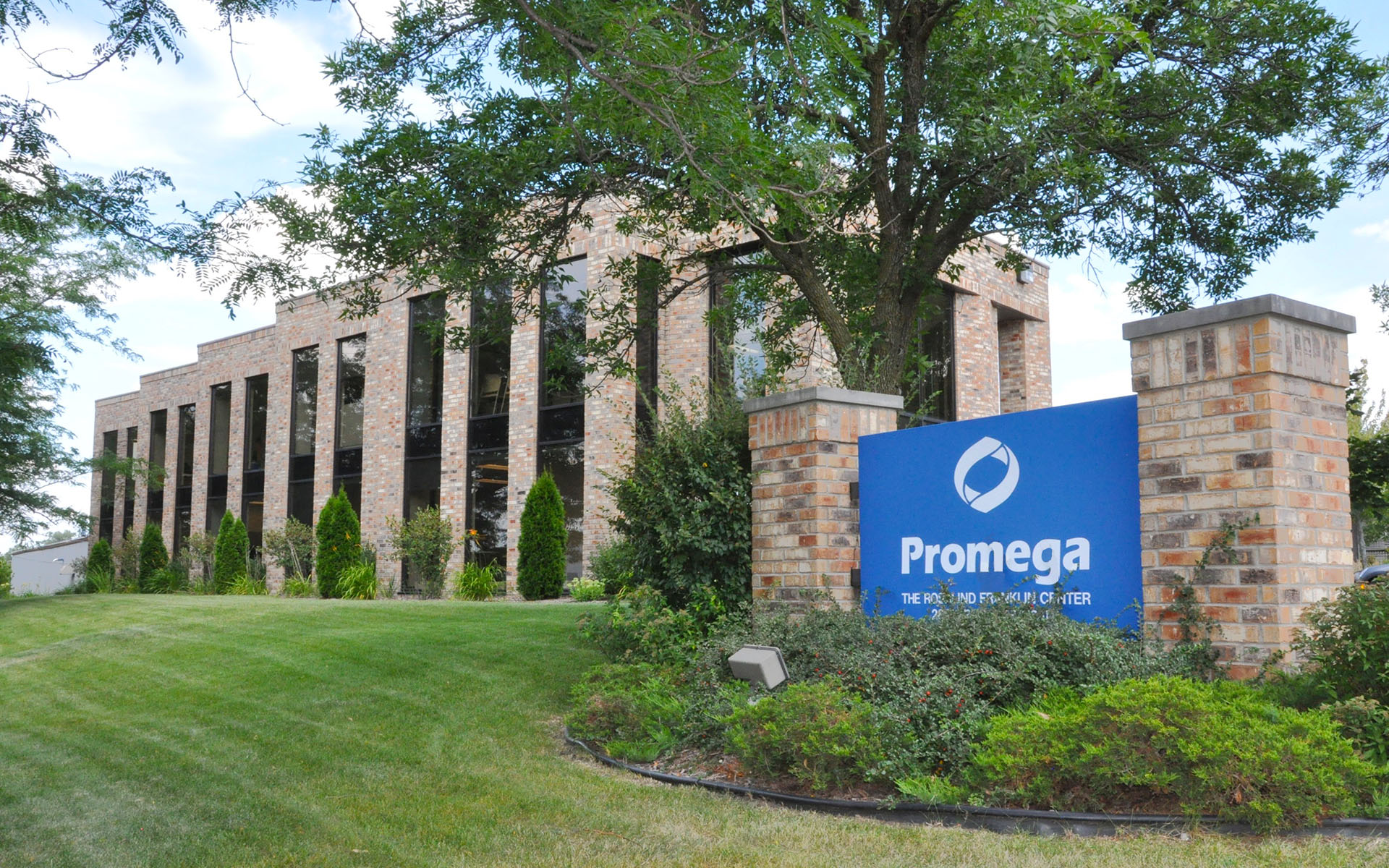
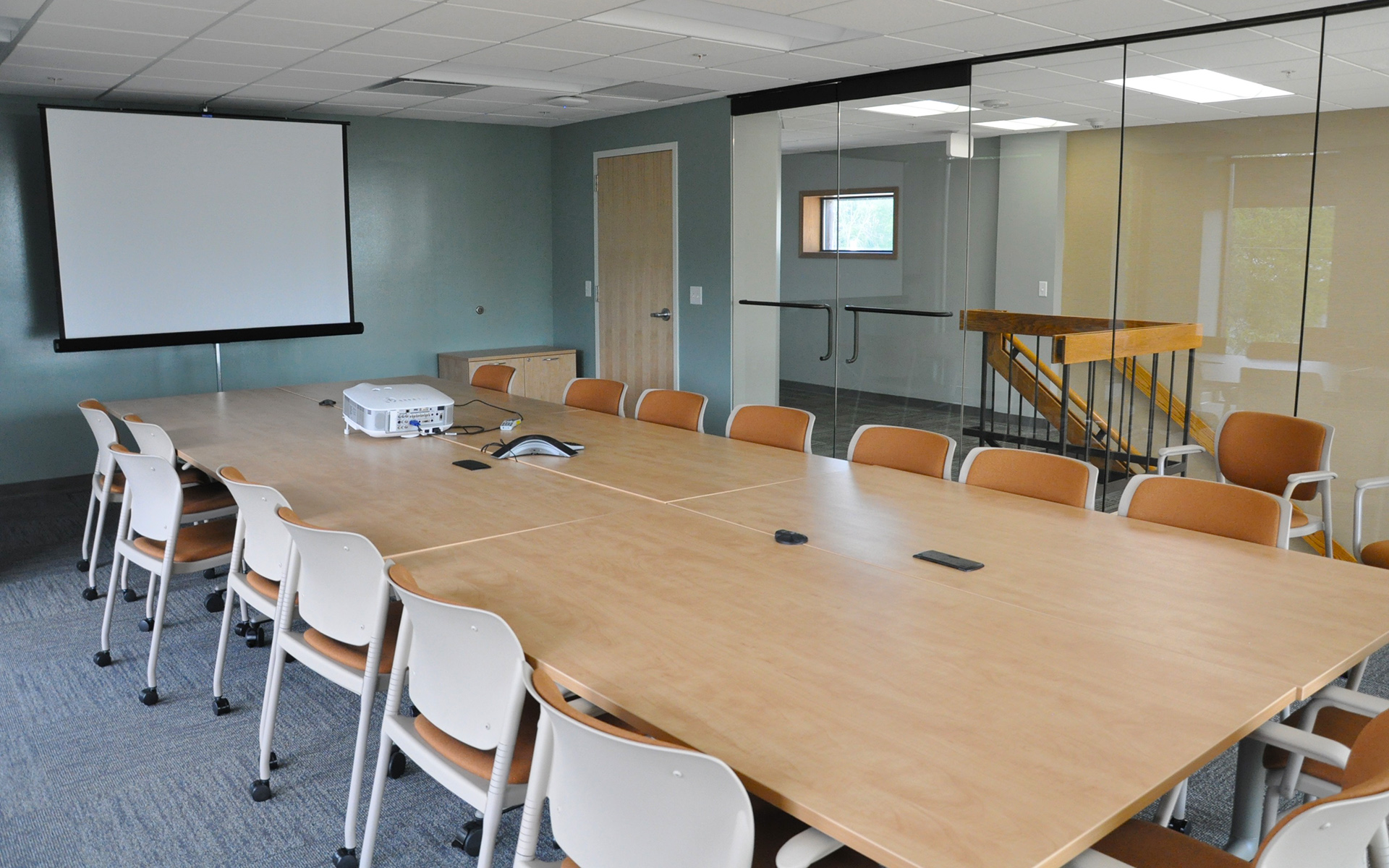
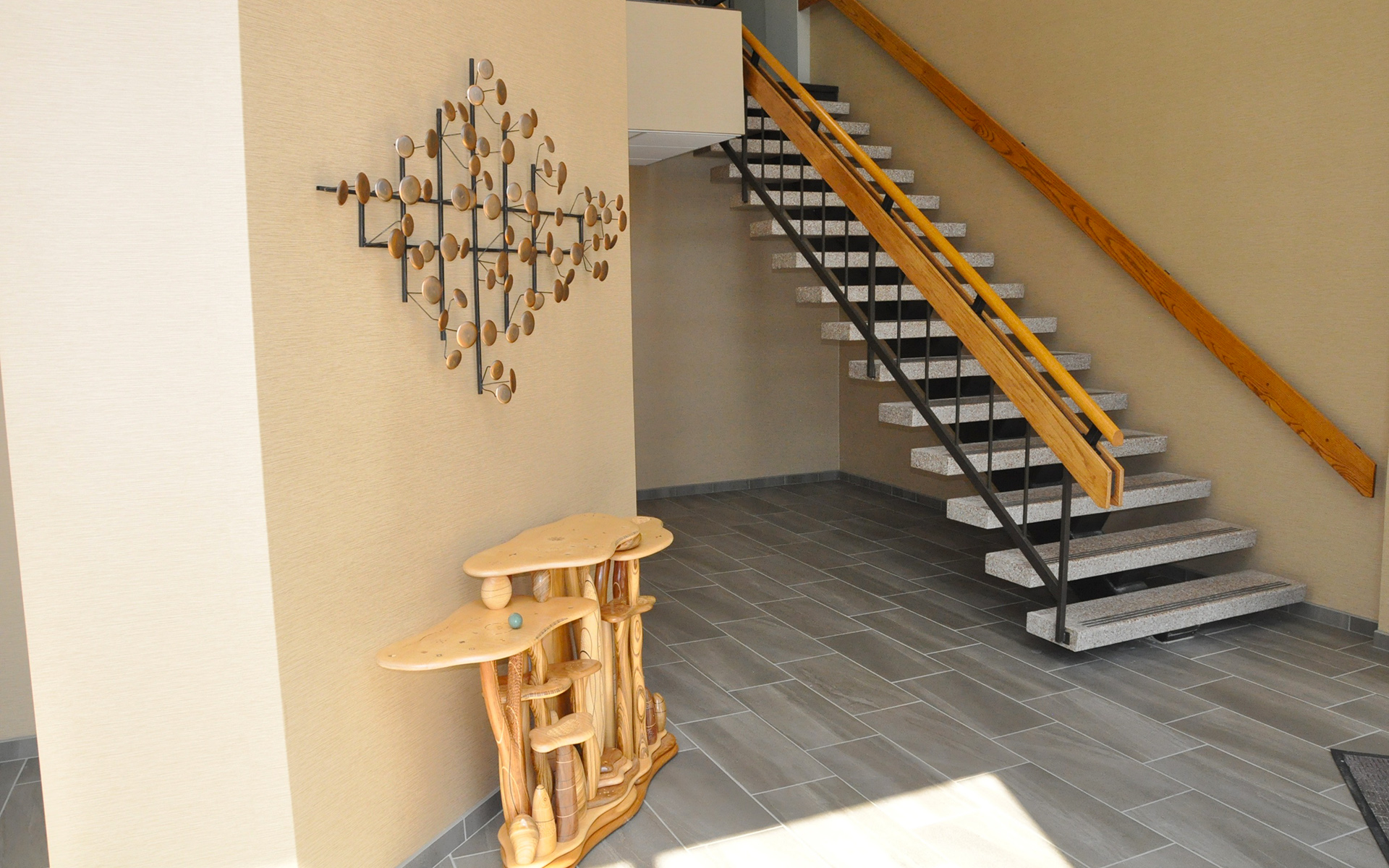
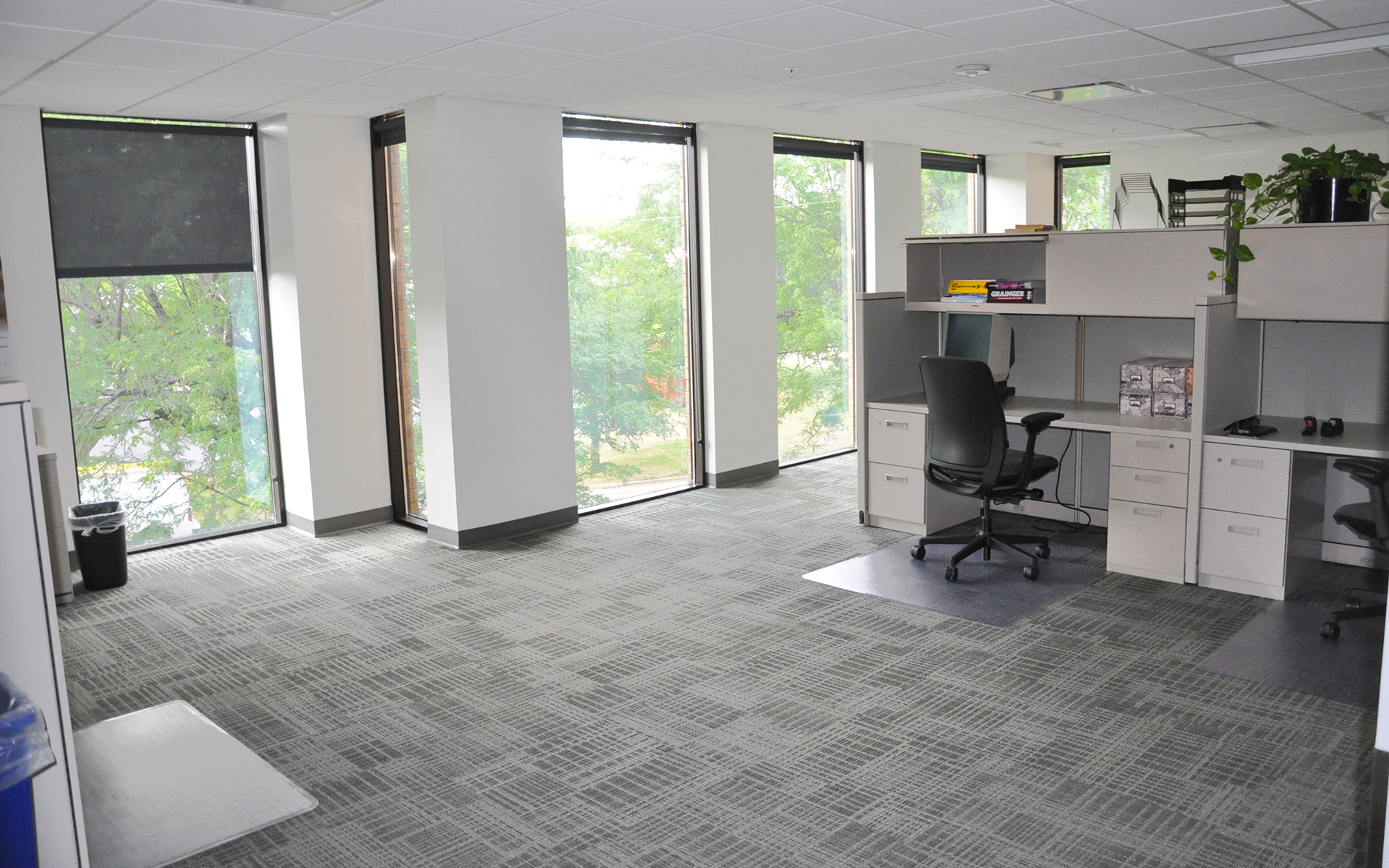
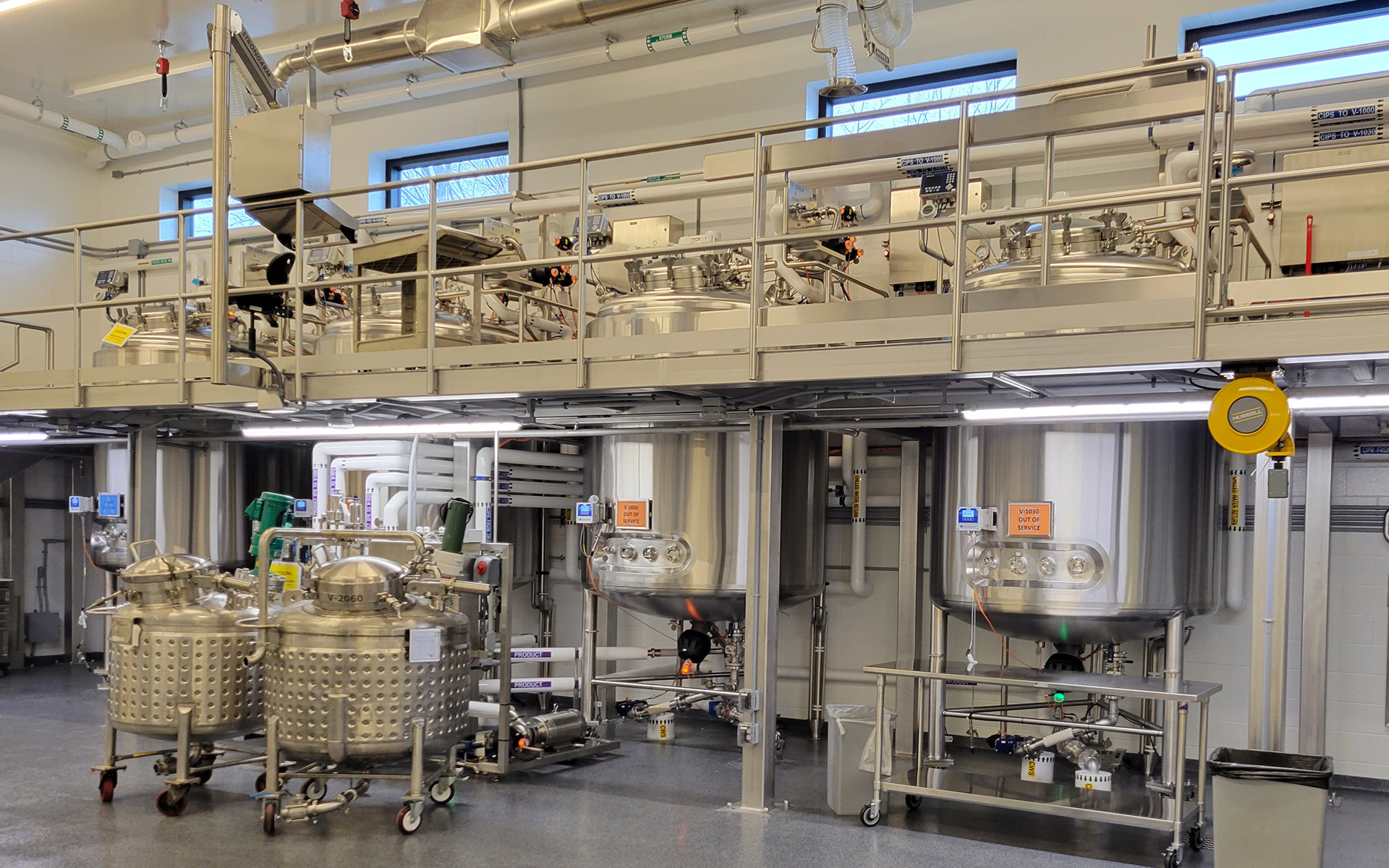
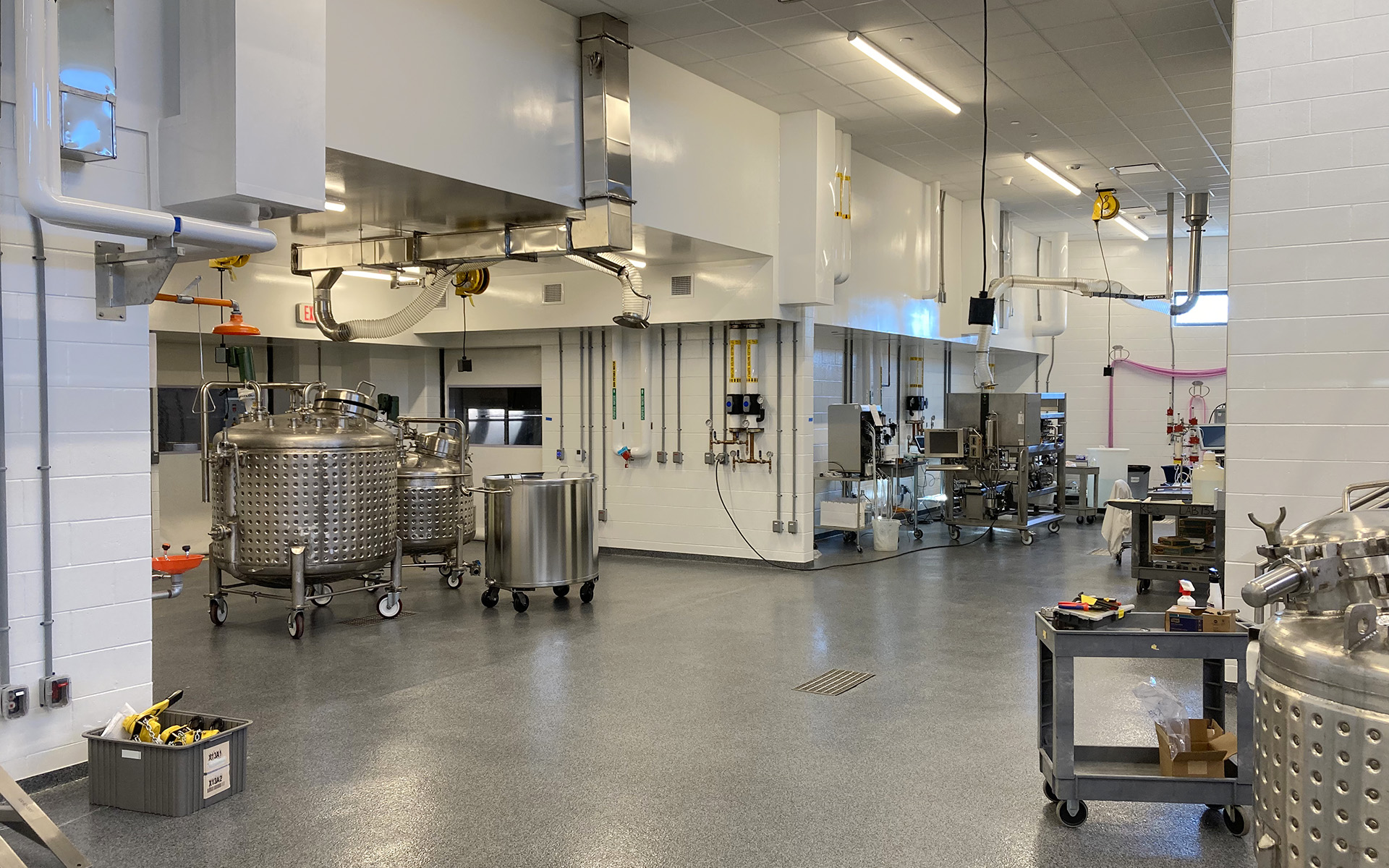
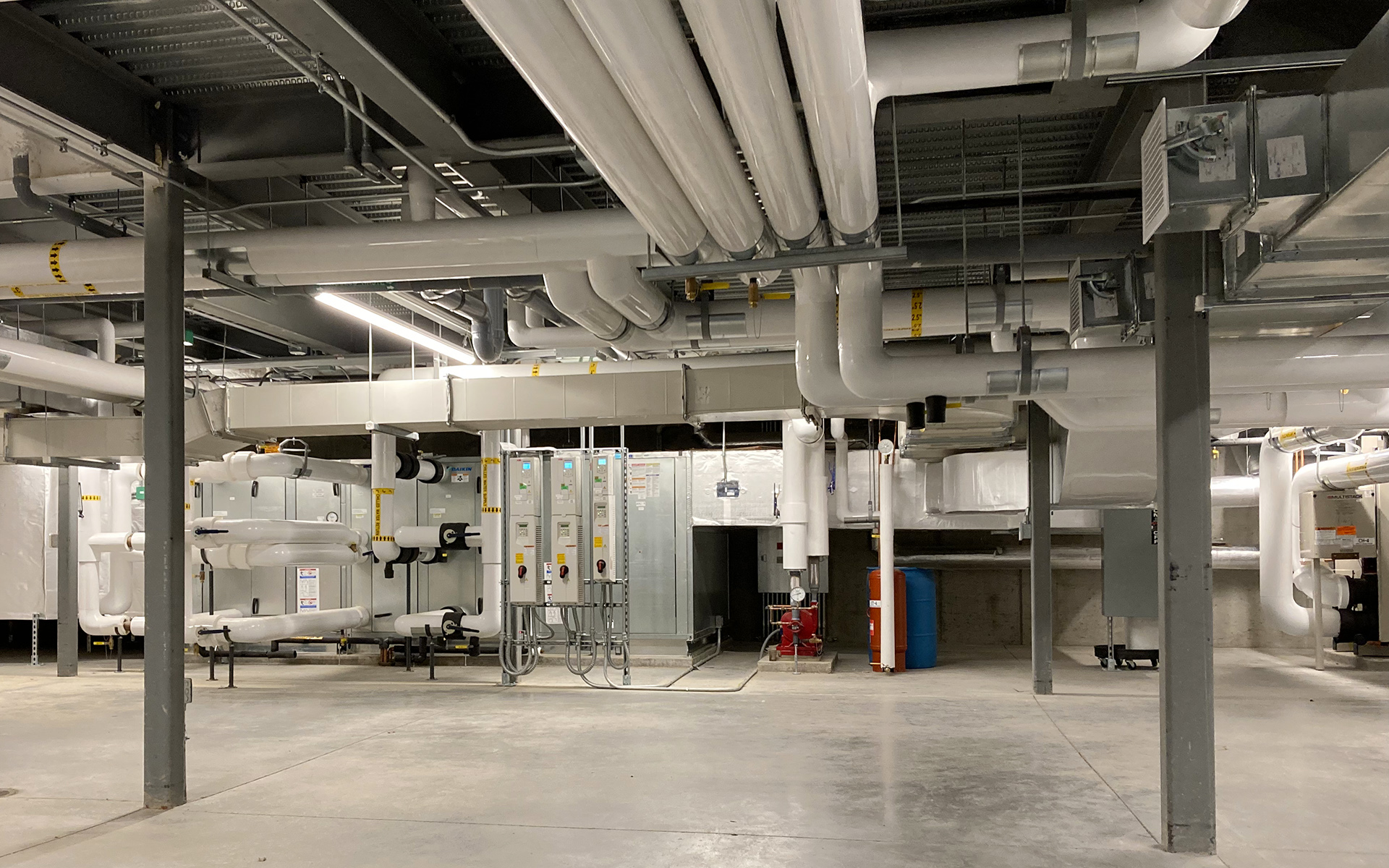
ROSALIND FRANKLIN CENTER
Manufacturing Facility
Named after chemist and x-ray crystallographer, Rosalind Franklin, this facility houses the large-scale manufacturing of proteins for various Promega products. Starting off this building program, Kraemer Brothers built out existing storage space into a wellness center and remodeled offices to an inviting open layout. Most recently Promega expanded their manufacturing operations to include production rooms, cold rooms, laboratories, and material storage rooms. Located in the large production room are four 4000-liter process tanks connected with a raised platform and the process panels used to control each tank. Sophisticated HVAC and specialized production equipment can be found throughout the addition. The mechanical systems used to run and power the production equipment, along with material storage rooms, are located in the basement. A ph-neutralization system, used for neutralizing all waste before being discharged, helps the surrounding environment and improves safety for the scientists. Finally, an automated CIP system is installed to help clean the 4,000-liter process and smaller portable tanks found throughout the production labs. Promega was able to remain fully operational during these renovations and additions.
RELATED